A Differentiable Dynamic Modeling Approach to Integrated Motion Planning and Actuator Physical Design for Mobile Manipulators
2405.00882

0

0
📉
Abstract
This paper investigates the differentiable dynamic modeling of mobile manipulators to facilitate efficient motion planning and physical design of actuators, where the actuator design is parameterized by physically meaningful motor geometry parameters. These parameters impact the manipulator's link mass, inertia, center-of-mass, torque constraints, and angular velocity constraints, influencing control authority in motion planning and trajectory tracking control. A motor's maximum torque/speed and how the design parameters affect the dynamics are modeled analytically, facilitating differentiable and analytical dynamic modeling. Additionally, an integrated locomotion and manipulation planning problem is formulated with direct collocation discretization, using the proposed differentiable dynamics and motor parameterization. Such dynamics are required to capture the dynamic coupling between the base and the manipulator. Numerical experiments demonstrate the effectiveness of differentiable dynamics in speeding up optimization and advantages in task completion time and energy consumption over established sequential motion planning approach. Finally, this paper introduces a simultaneous actuator design and motion planning framework, providing numerical results to validate the proposed differentiable modeling approach for co-design problems.
Create account to get full access
Overview
- The paper investigates differentiable dynamic modeling of mobile manipulators to enable efficient motion planning and physical design of actuators.
- The actuator design is parameterized by physically meaningful motor geometry parameters, which impact the manipulator's link mass, inertia, center-of-mass, torque constraints, and angular velocity constraints.
- An integrated locomotion and manipulation planning problem is formulated using the proposed differentiable dynamics and motor parameterization.
- Numerical experiments demonstrate the effectiveness of differentiable dynamics in speeding up optimization and advantages in task completion time and energy consumption.
- The paper introduces a simultaneous actuator design and motion planning framework, validating the proposed differentiable modeling approach for co-design problems.
Plain English Explanation
This research paper focuses on developing a more flexible and efficient way to design and control mobile robots with manipulator arms. The key idea is to model the dynamics of these robots in a differentiable way, meaning the model can be easily optimized and adjusted.
The researchers parameterized the robot's actuator design using physical properties like motor size and weight. These parameters affect the robot's overall dynamics, including how much force and speed the arms can produce. By modeling these relationships, the researchers can optimize the actuator design and the robot's movements at the same time.
This integrated approach allows the robots to complete tasks more quickly and efficiently compared to traditional methods that plan the movements and design the actuators separately. The paper demonstrates this through numerical simulations, showing the benefits of the differentiable dynamic modeling approach.
Overall, this work provides a powerful framework for designing and controlling mobile manipulator robots in an optimized and integrated way, which could lead to more capable and efficient robots for a variety of applications.
Technical Explanation
The paper presents a differentiable dynamic modeling approach for mobile manipulators, which enables efficient motion planning and physical design of the robot's actuators. The actuator design is parameterized using physically meaningful motor geometry parameters, such as rotor radius and motor length. These parameters directly impact the manipulator's link mass, inertia, center-of-mass, torque constraints, and angular velocity constraints, ultimately influencing the control authority during motion planning and trajectory tracking.
The researchers developed an analytical model to capture the maximum torque and speed capabilities of the motors, as well as how the design parameters affect the overall robot dynamics. This differentiable dynamics model is then integrated into a combined locomotion and manipulation planning problem, formulated using direct collocation discretization.
Numerical experiments demonstrate that the differentiable dynamics approach can significantly speed up the optimization process compared to established sequential motion planning methods. The integrated framework also shows advantages in terms of task completion time and energy consumption.
Finally, the paper introduces a simultaneous actuator design and motion planning framework, providing numerical results to validate the proposed differentiable modeling approach for co-design problems. This allows the robot's physical design and motion planning to be optimized together, leading to more efficient and capable mobile manipulator systems.
Critical Analysis
The paper presents a comprehensive and well-designed approach to integrating the physical design of mobile manipulator actuators with their motion planning. The use of differentiable dynamics is a key innovation that enables efficient optimization of the combined design and control problem.
One potential limitation is that the paper only validates the approach through numerical simulations, without any real-world experimental results. It would be helpful to see how the proposed framework performs on physical robot platforms to better understand its practical applicability and any challenges that may arise.
Additionally, the paper does not delve deeply into the specific optimization algorithms or solvers used, which could be an important consideration for scaling the approach to more complex robotic systems. Further details on the computational efficiency and scalability of the framework would strengthen the technical contribution.
Overall, this research represents an important step forward in integrated design and control of mobile manipulators. Extending the differentiable modeling approach to a wider range of robotic systems, and validating it on physical platforms, could lead to significant advancements in the capabilities and efficiency of next-generation robotic technologies. [See also: Adaptive Gait Modeling and Optimization for Principally Kinematic Systems, Differentiable Particles for General-Purpose Deformable Object Manipulation, and QuasiSim: Parameterized Quasi-physical Simulators for Dexterous Manipulations]
Conclusion
This paper presents a novel approach to modeling the dynamics of mobile manipulator robots in a differentiable way, enabling efficient optimization of both the physical actuator design and the robot's motion planning. By parameterizing the actuator design using physically meaningful motor geometry, the researchers were able to capture the complex relationships between the robot's capabilities and its physical properties.
The integrated locomotion and manipulation planning framework demonstrated significant advantages over traditional sequential approaches, including faster optimization times and improved task performance in terms of completion time and energy consumption. This work lays the groundwork for more advanced co-design techniques that can yield highly capable and efficient mobile manipulator systems. [See also: Linear MPC with Control Barrier Functions for Differential Drive and Optimized Design of Soft Actuator Considering Force/Torque and Bendability]
Overall, this research represents an important step forward in the field of mobile manipulation, with the potential to enable more capable, efficient, and adaptable robotic systems for a wide range of applications.
This summary was produced with help from an AI and may contain inaccuracies - check out the links to read the original source documents!
Related Papers

Physics-data hybrid dynamic model of a multi-axis manipulator for sensorless dexterous manipulation and high-performance motion planning
Wu-Te Yang, Jyun-Ming Liao, Pei-Chun Lin

0

0
We report on the development of an implementable physics-data hybrid dynamic model for an articulated manipulator to plan and operate in various scenarios. Meanwhile, the physics-based and data-driven dynamic models are studied in this research to select the best model for planning. The physics-based model is constructed using the Lagrangian method, and the loss terms include inertia loss, viscous loss, and friction loss. As for the data-driven model, three methods are explored, including DNN, LSTM, and XGBoost. Our modeling results demonstrate that, after comprehensive hyperparameter optimization, the XGBoost architecture outperforms DNN and LSTM in accurately representing manipulator dynamics. The hybrid model with physics-based and data-driven terms has the best performance among all models based on the RMSE criteria, and it only needs about 24k of training data. In addition, we developed a virtual force sensor of a manipulator using the observed external torque derived from the dynamic model and designed a motion planner through the physics-data hybrid dynamic model. The external torque contributes to forces and torque on the end effector, facilitating interaction with the surroundings, while the internal torque governs manipulator motion dynamics and compensates for internal losses. By estimating external torque via the difference between measured joint torque and internal losses, we implement a sensorless control strategy which is demonstrated through a peg-in-hole task. Lastly, a learning-based motion planner based on the hybrid dynamic model assists in planning time-efficient trajectories for the manipulator. This comprehensive approach underscores the efficacy of integrating physics-based and data-driven models for advanced manipulator control and planning in industrial environments.
5/8/2024

Distributed Motion Control of Multiple Mobile Manipulator System with Disturbance and Communication Delay
Wenhang Liu, Meng Ren, Kun Song, Michael Yu Wang, Zhenhua Xiong

0

0
In real-world object manipulation scenarios, multiple mobile manipulator systems may suffer from disturbances and asynchrony, leading to excessive interaction forces and causing object damage or emergency stops. This paper presents a novel distributed motion control approach aimed at reducing these unnecessary interaction forces. The control strategy only utilizes force information without the need for global position and velocity information. Disturbances are corrected through compensatory movements of the manipulators. Besides, the asymmetric, non-uniform, and time-varying communication delays between robots are also considered. The stability of the control law is rigorously proven by the Lyapunov theorem. Subsequently, the efficacy of the proposed control law is validated through simulations and experiments of collaborative object transportation by two robots. Experimental results demonstrate the effectiveness of the proposed control law in reducing interaction forces during object manipulation.
6/11/2024
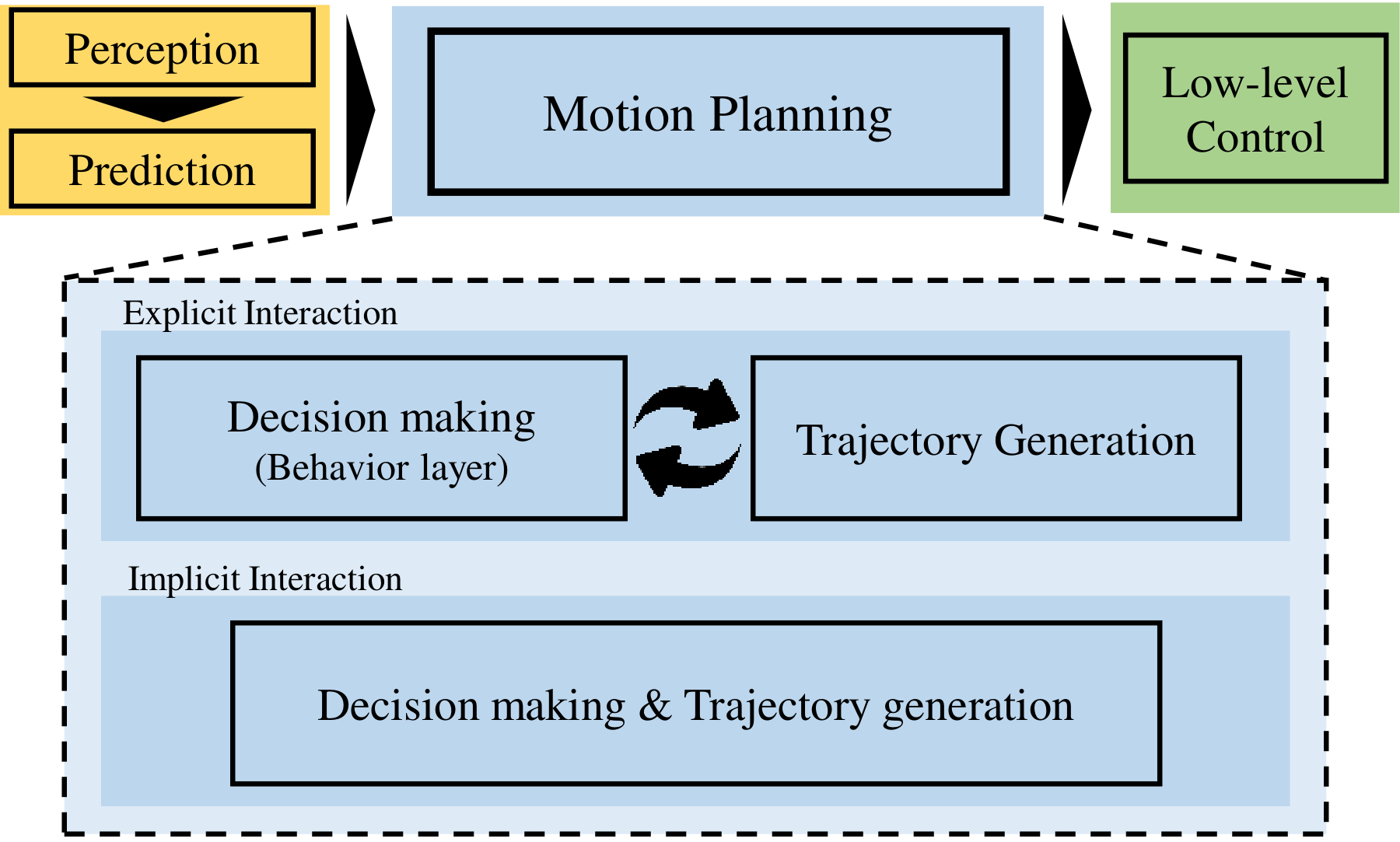
Towards A General-Purpose Motion Planning for Autonomous Vehicles Using Fluid Dynamics
MReza Alipour Sormoli, Konstantinos Koufos, Mehrdad Dianati, Roger Woodman

0

0
General-purpose motion planners for automated/autonomous vehicles promise to handle the task of motion planning (including tactical decision-making and trajectory generation) for various automated driving functions (ADF) in a diverse range of operational design domains (ODDs). The challenges of designing a general-purpose motion planner arise from several factors: a) A plethora of scenarios with different semantic information in each driving scene should be addressed, b) a strong coupling between long-term decision-making and short-term trajectory generation shall be taken into account, c) the nonholonomic constraints of the vehicle dynamics must be considered, and d) the motion planner must be computationally efficient to run in real-time. The existing methods in the literature are either limited to specific scenarios (logic-based) or are data-driven (learning-based) and therefore lack explainability, which is important for safety-critical automated driving systems (ADS). This paper proposes a novel general-purpose motion planning solution for ADS inspired by the theory of fluid mechanics. A computationally efficient technique, i.e., the lattice Boltzmann method, is then adopted to generate a spatiotemporal vector field, which in accordance with the nonholonomic dynamic model of the Ego vehicle is employed to generate feasible candidate trajectories. The trajectory optimising ride quality, efficiency and safety is finally selected to calculate the imminent control signals, i.e., throttle/brake and steering angle. The performance of the proposed approach is evaluated by simulations in highway driving, on-ramp merging, and intersection crossing scenarios, and it is found to outperform traditional motion planning solutions based on model predictive control (MPC).
6/11/2024

Adaptive Gait Modeling and Optimization for Principally Kinematic Systems
Siming Deng, Noah J. Cowan, Brian A. Bittner

0

0
Robotic adaptation to unanticipated operating conditions is crucial to achieving persistence and robustness in complex real world settings. For a wide range of cutting-edge robotic systems, such as micro- and nano-scale robots, soft robots, medical robots, and bio-hybrid robots, it is infeasible to anticipate the operating environment a priori due to complexities that arise from numerous factors including imprecision in manufacturing, chemo-mechanical forces, and poorly understood contact mechanics. Drawing inspiration from data-driven modeling, geometric mechanics (or gauge theory), and adaptive control, we employ an adaptive system identification framework and demonstrate its efficacy in enhancing the performance of principally kinematic locomotors (those governed by Rayleigh dissipation or zero momentum conservation). We showcase the capability of the adaptive model to efficiently accommodate varying terrains and iteratively modified behaviors within a behavior optimization framework. This provides both the ability to improve fundamental behaviors and perform motion tracking to precision. Notably, we are capable of optimizing the gaits of the Purcell swimmer using approximately 10 cycles per link, which for the nine-link Purcell swimmer provides a factor of ten improvement in optimization speed over the state of the art. Beyond simply a computational speed up, this ten-fold improvement may enable this method to be successfully deployed for in-situ behavior refinement, injury recovery, and terrain adaptation, particularly in domains where simulations provide poor guides for the real world.
4/19/2024