Learning-based Position and Stiffness Feedforward Control of Antagonistic Soft Pneumatic Actuators using Gaussian Processes

0
👀
Sign in to get full access
Overview
- This paper presents a learning-based approach for controlling the position and stiffness of soft pneumatic variable stiffness actuators (VSAs).
- Conventional model-based control of these nonlinear systems can be challenging, but machine learning offers a promising alternative.
- The authors introduce a soft pneumatic VSA and use a test bench to automatically measure its variable joint stiffness.
- They then train Gaussian processes to predict the pressures required to achieve desired position and stiffness, with a feedforward error that is compensated by feedback control.
- Experiments show the learning-based approach allows continuous adjustment of position and stiffness without requiring explicit model knowledge.
Plain English Explanation
Variable stiffness actuators (VSAs) are a type of robotic component that can change their stiffness or "hardness" on the fly. This allows them to be both rigid and flexible, which can be useful for a variety of applications. Conventional model-based control of these systems can be challenging because they have a lot of nonlinear, or unpredictable, behaviors.
In this work, the researchers take a different approach - they use machine learning techniques to control the position and stiffness of a soft pneumatic VSA. Machine learning allows them to build models based on real data from the actuator, rather than relying on complicated mathematical models. This helps account for the nonlinearities in the system.
The key steps are:
- The researchers built a test bench that can automatically measure the variable stiffness of the soft actuator.
- They used this data to train Gaussian process models to predict the pressures needed to achieve desired positions and stiffness levels.
- During control, these Gaussian process models provide feedforward control, with a feedback loop to compensate for any errors.
The experiments show this learning-based approach works well, allowing the actuator's position and stiffness to be continuously adjusted without needing detailed knowledge of the actuator's internal mechanics. This could be very useful for real-world robotic applications that require variable stiffness, like assistive devices or delicate manipulation tasks.
Technical Explanation
The paper introduces a soft pneumatic variable stiffness actuator (VSA) and presents a universal, learning-based approach for controlling its position and stiffness. Conventional model-based control of these nonlinear systems can be challenging, as it requires significant effort and design-dependent assumptions.
To address this, the authors propose using machine learning techniques. They set up a test bench that enables automated measurement of the VSA's variable joint stiffness. This data is then used to train Gaussian process models [1] that can predict the pressures required to achieve desired positions and stiffness levels.
During control, the Gaussian process models provide feedforward control, predicting the pressures needed based on the target position and stiffness. A feedback control loop is then used to compensate for any errors in the feedforward predictions. Experiments with the soft pneumatic VSA show the learning-based approach can continuously adjust both position and stiffness without requiring explicit model knowledge of the actuator [2,3].
The average feedforward error is 11.5% of the total pressure range, which is compensated by the feedback control. This demonstrates the efficacy of the learning-based method in controlling the highly nonlinear soft VSA system [4,5].
Critical Analysis
The paper presents a compelling learning-based approach for controlling variable stiffness actuators, which addresses the challenges of conventional model-based control. The use of Gaussian process models to predict the actuator's behavior based on real measured data is a smart and effective strategy.
One potential limitation is that the training and testing was done on a single actuator prototype. It would be valuable to see how well the approach generalizes to other VSA designs or even different classes of soft actuators. The authors mention this as a direction for future work.
Additionally, the paper does not provide much detail on the robustness of the control approach. It would be helpful to understand how the system performs under perturbations, uncertainties, or changing environmental conditions.
Overall, this is a well-executed study that demonstrates the promise of learning-based control for soft robotic systems. The findings could have important implications for the design of variable stiffness devices, particularly in applications like human-robot interaction and delicate manipulation tasks. Continued research in this direction, including addressing the limitations mentioned, could further advance the field.
Conclusion
This paper presents a novel, learning-based approach for controlling the position and stiffness of soft pneumatic variable stiffness actuators (VSAs). By training Gaussian process models on real data from a custom test bench, the researchers were able to develop a control system that can continuously adjust the actuator's behavior without requiring detailed knowledge of its internal mechanics.
The key innovation is the use of machine learning to account for the highly nonlinear characteristics of soft VSAs, which can make conventional model-based control challenging. The experimental results show the learning-based approach can achieve good performance, with feedforward errors compensated by feedback control.
This work contributes an effective solution for controlling the versatile but complex behavior of soft robotic components. Further development and testing of this approach could lead to significant advances in the design of variable stiffness devices for a wide range of applications, from assistive technologies to delicate manipulation tasks.
This summary was produced with help from an AI and may contain inaccuracies - check out the links to read the original source documents!
Related Papers
👀

0
Learning-based Position and Stiffness Feedforward Control of Antagonistic Soft Pneumatic Actuators using Gaussian Processes
Tim-Lukas Habich, Sarah Kleinjohann, Moritz Schappler
Variable stiffness actuator (VSA) designs are manifold. Conventional model-based control of these nonlinear systems is associated with high effort and design-dependent assumptions. In contrast, machine learning offers a promising alternative as models are trained on real measured data and nonlinearities are inherently taken into account. Our work presents a universal, learning-based approach for position and stiffness control of soft actuators. After introducing a soft pneumatic VSA, the model is learned with input-output data. For this purpose, a test bench was set up which enables automated measurement of the variable joint stiffness. During control, Gaussian processes are used to predict pressures for achieving desired position and stiffness. The feedforward error is on average 11.5% of the total pressure range and is compensated by feedback control. Experiments with the soft actuator show that the learning-based approach allows continuous adjustment of position and stiffness without model knowledge.
Read more4/17/2024
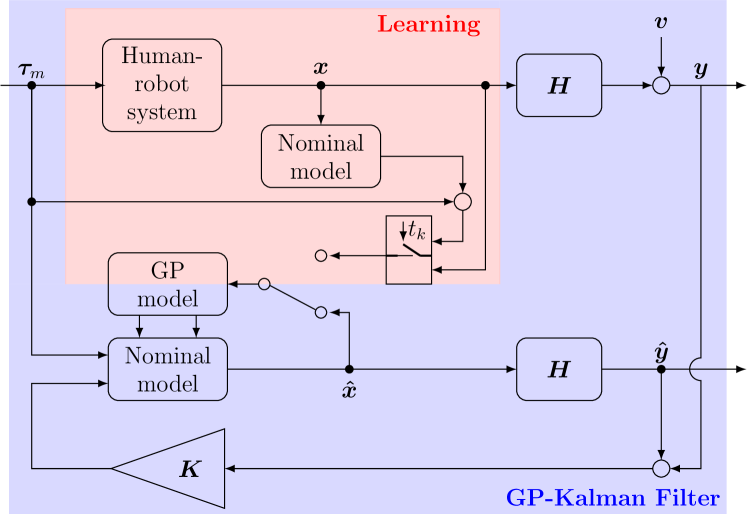

0
Data-driven Force Observer for Human-Robot Interaction with Series Elastic Actuators using Gaussian Processes
Samuel Tesfazgi, Markus Ke{ss}ler, Emilio Trigili, Armin Lederer, Sandra Hirche
Ensuring safety and adapting to the user's behavior are of paramount importance in physical human-robot interaction. Thus, incorporating elastic actuators in the robot's mechanical design has become popular, since it offers intrinsic compliance and additionally provide a coarse estimate for the interaction force by measuring the deformation of the elastic components. While observer-based methods have been shown to improve these estimates, they rely on accurate models of the system, which are challenging to obtain in complex operating environments. In this work, we overcome this issue by learning the unknown dynamics components using Gaussian process (GP) regression. By employing the learned model in a Bayesian filtering framework, we improve the estimation accuracy and additionally obtain an observer that explicitly considers local model uncertainty in the confidence measure of the state estimate. Furthermore, we derive guaranteed estimation error bounds, thus, facilitating the use in safety-critical applications. We demonstrate the effectiveness of the proposed approach experimentally in a human-exoskeleton interaction scenario.
Read more5/15/2024
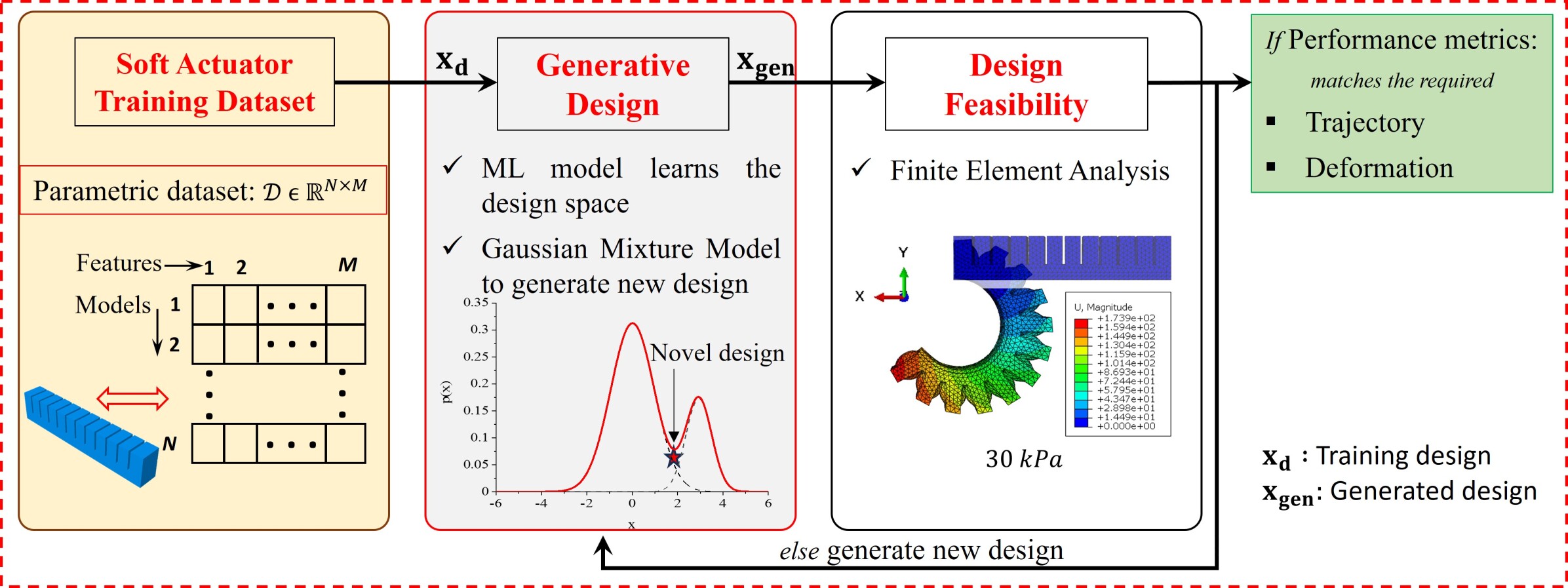

0
Generative Design of Multimodal Soft Pneumatic Actuators
Saswath Ghosh, Sitikantha Roy
The recent advancements in machine learning techniques have steered us towards the data-driven design of products. Motivated by this objective, the present study proposes an automated design methodology that employs data-driven methods to generate new designs of soft actuators. One of the bottlenecks in the data-driven automated design process is having publicly available data to train the model. Due to its unavailability, a synthetic data set of soft pneumatic network (Pneu-net) actuators has been created. The parametric design data set for the training of the generative model is created using data augmentation. Next, the Gaussian mixture model has been applied to generate novel parametric designs of Pneu-net actuators. The distance-based metric defines the novelty and diversity of the generated designs. In addition, it is noteworthy that the model has the potential to generate a multimodal Pneu-net actuator that could perform in-plane bending and out-of-plane twisting. Later, the novel design is passed through finite element analysis to evaluate the quality of the generated design. Moreover, the trajectory of each category of Pneu-net actuators evaluates the performance of the generated Pneu-net actuators and emphasizes the necessity of multimodal actuation. The proposed model could accelerate the design of new soft robots by selecting a soft actuator from the developed novel pool of soft actuators.
Read more8/13/2024


0
Control Pneumatic Soft Bending Actuator with Feedforward Hysteresis Compensation by Pneumatic Physical Reservoir Computing
Junyi Shen, Tetsuro Miyazaki, Kenji Kawashima
The nonlinearities of soft robots bring control challenges like hysteresis but also provide them with computational capacities. This paper introduces a fuzzy pneumatic physical reservoir computing (FPRC) model for feedforward hysteresis compensation in motion tracking control of soft actuators. Our method utilizes a pneumatic bending actuator as a physical reservoir with nonlinear computing capacities to control another pneumatic bending actuator. The FPRC model employs a Takagi-Sugeno (T-S) fuzzy model to process outputs from the physical reservoir. In comparative evaluations, the FPRC model shows equivalent training performance to an Echo State Network (ESN) model, whereas it exhibits better test accuracies with significantly reduced execution time. Experiments validate the proposed FPRC model's effectiveness in controlling the bending motion of the pneumatic soft actuator with open and closed-loop control systems. The proposed FPRC model's robustness against environmental disturbances has also been experimentally verified. To the authors' knowledge, this is the first implementation of a physical system in the feedforward hysteresis compensation model for controlling soft actuators. This study is expected to advance physical reservoir computing in nonlinear control applications and extend the feedforward hysteresis compensation methods for controlling soft actuators.
Read more9/12/2024