Nonlinear Inverse Design of Mechanical Multi-Material Metamaterials Enabled by Video Denoising Diffusion and Structure Identifier

0
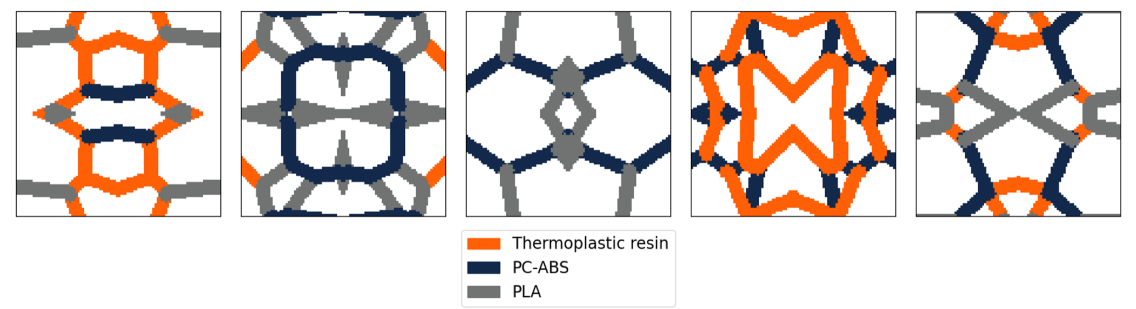
Sign in to get full access
Overview
- Researchers developed a novel approach for the inverse design of multi-material mechanical metamaterials.
- The method combines video denoising diffusion and a structure identifier to enable nonlinear inverse design.
- This allows for the creation of complex metamaterial structures with tailored mechanical properties.
Plain English Explanation
The researchers in this paper tackled the challenge of designing metamaterials - materials engineered to have unique properties not found in nature. Specifically, they focused on mechanical metamaterials, which are designed to have specific mechanical behaviors like flexibility or strength.
Traditionally, designing these metamaterials has been difficult because the relationship between the material's structure and its properties is complex and nonlinear. The researchers developed a new approach that combines two key technologies:
-
Video Denoising Diffusion: This is a machine learning technique that can "clean up" noisy images, like turning a blurry photo into a clear one. The researchers adapted this to work on 3D models of the metamaterial structures.
-
Structure Identifier: This component analyzes the 3D structure of the metamaterial and identifies key features that contribute to its mechanical properties.
By combining these two techniques, the researchers were able to inverse design the metamaterial structures - starting with the desired mechanical properties and then automatically generating the optimal 3D structure to achieve those properties. This enables the creation of highly complex, multi-material metamaterials with tailored behaviors.
Technical Explanation
The core of the researchers' approach is a novel inverse design framework that integrates video denoising diffusion and a structure identifier network.
The video denoising diffusion model takes a 3D voxel representation of the metamaterial structure as input and learns to progressively "denoise" it, removing high-frequency noise and artifacts. This allows the model to efficiently explore the space of valid metamaterial structures.
The structure identifier network then analyzes the denoised 3D structure and extracts key geometric features that contribute to the material's mechanical properties. This information is used to guide the inverse design process, ensuring the generated structures have the desired mechanical behavior.
By iterating between the denoising and structure identification components, the framework can converge on optimal multi-material metamaterial designs that meet target mechanical specifications. The researchers demonstrated this approach on a range of examples, showing how it enables the inverse design of complex, hierarchical metamaterial structures.
Critical Analysis
The researchers acknowledge several limitations of their approach. First, the method currently only supports linear elasticity - it cannot handle more complex, nonlinear mechanical behaviors. Extending the framework to handle nonlinear materials and large deformations would be an important area for future work.
Additionally, the computational cost of the method could be prohibitive for large-scale, high-resolution metamaterial designs. The researchers note that further optimizations to the neural network architectures and training procedures could help improve efficiency.
Finally, the paper does not provide a detailed analysis of the generated metamaterial structures or a comparison to human-designed alternatives. A more thorough evaluation of the mechanical properties and performance of the inverse-designed metamaterials would help validate the effectiveness of the approach.
Conclusion
This paper presents a novel inverse design framework that leverages video denoising diffusion and structure identification to enable the creation of complex, multi-material mechanical metamaterials. By automating the design process and extracting key geometric features, the researchers have developed a powerful tool for engineering metamaterials with tailored mechanical behaviors.
While the current implementation has some limitations, the core ideas demonstrate the potential of this approach to transform the way we design advanced functional materials. Further advancements in this direction could lead to new classes of high-performance metamaterials with a wide range of applications in engineering, robotics, and beyond.
This summary was produced with help from an AI and may contain inaccuracies - check out the links to read the original source documents!
Related Papers
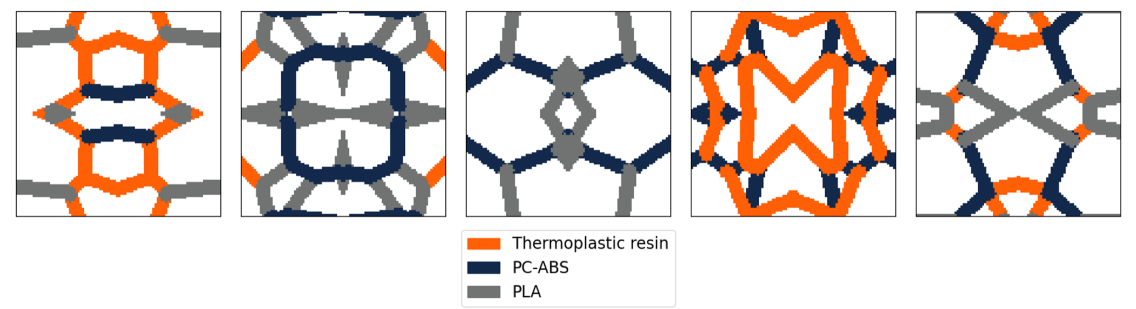

0
Nonlinear Inverse Design of Mechanical Multi-Material Metamaterials Enabled by Video Denoising Diffusion and Structure Identifier
Jaewan Park, Shashank Kushwaha, Junyan He, Seid Koric, Qibang Liu, Iwona Jasiuk, Diab Abueidda
Metamaterials, synthetic materials with customized properties, have emerged as a promising field due to advancements in additive manufacturing. These materials derive unique mechanical properties from their internal lattice structures, which are often composed of multiple materials that repeat geometric patterns. While traditional inverse design approaches have shown potential, they struggle to map nonlinear material behavior to multiple possible structural configurations. This paper presents a novel framework leveraging video diffusion models, a type of generative artificial Intelligence (AI), for inverse multi-material design based on nonlinear stress-strain responses. Our approach consists of two key components: (1) a fields generator using a video diffusion model to create solution fields based on target nonlinear stress-strain responses, and (2) a structure identifier employing two UNet models to determine the corresponding multi-material 2D design. By incorporating multiple materials, plasticity, and large deformation, our innovative design method allows for enhanced control over the highly nonlinear mechanical behavior of metamaterials commonly seen in real-world applications. It offers a promising solution for generating next-generation metamaterials with finely tuned mechanical characteristics.
Read more9/24/2024


0
Guided Diffusion for Fast Inverse Design of Density-based Mechanical Metamaterials
Yanyan Yang, Lili Wang, Xiaoya Zhai, Kai Chen, Wenming Wu, Yunkai Zhao, Ligang Liu, Xiao-Ming Fu
Mechanical metamaterial is a synthetic material that can possess extraordinary physical characteristics, such as abnormal elasticity, stiffness, and stability, by carefully designing its internal structure. To make metamaterials contain delicate local structures with unique mechanical properties, it is a potential method to represent them through high-resolution voxels. However, it brings a substantial computational burden. To this end, this paper proposes a fast inverse design method, whose core is an advanced deep generative AI algorithm, to generate voxel-based mechanical metamaterials. Specifically, we use the self-conditioned diffusion model, capable of generating a microstructure with a resolution of $128^3$ to approach the specified homogenized tensor matrix in just 3 seconds. Accordingly, this rapid reverse design tool facilitates the exploration of extreme metamaterials, the sequence interpolation in metamaterials, and the generation of diverse microstructures for multi-scale design. This flexible and adaptive generative tool is of great value in structural engineering or other mechanical systems and can stimulate more subsequent research.
Read more6/11/2024
📊

0
Inverse designing metamaterials with programmable nonlinear functional responses in graph space
Marco Maurizi, Derek Xu, Yu-Tong Wang, Desheng Yao, David Hahn, Mourad Oudich, Anish Satpati, Mathieu Bauchy, Wei Wang, Yizhou Sun, Yun Jing, Xiaoyu Rayne Zheng
Material responses to static and dynamic stimuli, represented as nonlinear curves, are design targets for engineering functionalities like structural support, impact protection, and acoustic and photonic bandgaps. Three-dimensional metamaterials offer significant tunability due to their internal structure, yet existing methods struggle to capture their complex behavior-to-structure relationships. We present GraphMetaMat, a graph-based framework capable of designing three-dimensional metamaterials with programmable responses and arbitrary manufacturing constraints. Integrating graph networks, physics biases, reinforcement learning, and tree search, GraphMetaMat can target stress-strain curves spanning four orders of magnitude and complex behaviors, as well as viscoelastic transmission responses with varying attenuation gaps. GraphMetaMat can create cushioning materials for protective equipment and vibration-damping panels for electric vehicles, outperforming commercial materials, and enabling the automatic design of materials with on-demand functionalities.
Read more8/13/2024


0
An Uncertainty-aware Deep Learning Framework-based Robust Design Optimization of Metamaterial Units
Zihan Wang, Anindya Bhaduri, Hongyi Xu, Liping Wang
Mechanical metamaterials represent an innovative class of artificial structures, distinguished by their extraordinary mechanical characteristics, which are beyond the scope of traditional natural materials. The use of deep generative models has become increasingly popular in the design of metamaterial units. The effectiveness of using deep generative models lies in their capacity to compress complex input data into a simplified, lower-dimensional latent space, while also enabling the creation of novel optimal designs through sampling within this space. However, the design process does not take into account the effect of model uncertainty due to data sparsity or the effect of input data uncertainty due to inherent randomness in the data. This might lead to the generation of undesirable structures with high sensitivity to the uncertainties in the system. To address this issue, a novel uncertainty-aware deep learning framework-based robust design approach is proposed for the design of metamaterial units with optimal target properties. The proposed approach utilizes the probabilistic nature of the deep learning framework and quantifies both aleatoric and epistemic uncertainties associated with surrogate-based design optimization. We demonstrate that the proposed design approach is capable of designing high-performance metamaterial units with high reliability. To showcase the effectiveness of the proposed design approach, a single-objective design optimization problem and a multi-objective design optimization problem are presented. The optimal robust designs obtained are validated by comparing them to the designs obtained from the topology optimization method as well as the designs obtained from a deterministic deep learning framework-based design optimization where none of the uncertainties in the system are explicitly considered.
Read more7/31/2024