Statistical Batch-Based Bearing Fault Detection

0

Sign in to get full access
Overview
- The paper presents a statistical batch-based approach for bearing fault detection.
- It aims to address challenges in real-time fault detection by analyzing bearing vibration data in batches rather than individual measurements.
- The method uses statistical metrics to identify abnormal bearing behavior and trigger fault alarms.
Plain English Explanation
The paper describes a new way to detect problems with machine bearings, which are crucial components in many types of equipment. Bearings can wear out or develop faults over time, which can lead to equipment failure if not caught early.
The researchers propose a [object Object] for detecting bearing faults. Instead of analyzing individual vibration measurements from the bearing, their method looks at the data in batches or groups. This allows them to use statistical metrics, like the average and standard deviation of the vibration data, to identify abnormal behavior that could indicate a developing fault.
By analyzing the data in batches rather than one measurement at a time, the [object Object] can be more robust and reliable. This is important for real-world applications where the vibration data may be noisy or variable.
The key idea is to set thresholds for these statistical metrics that trigger a fault alarm when the data falls outside of the normal range. This provides an early warning system to alert operators of potential bearing issues before they escalate into major problems.
Technical Explanation
The paper proposes a [object Object] for bearing fault detection. The method analyzes vibration data from the bearing in batches rather than individual measurements.
For each batch of data, the approach calculates several statistical metrics, including:
- Mean
- Standard deviation
- Skewness
- Kurtosis
These metrics provide information about the overall distribution and variability of the vibration measurements within the batch. The researchers then use thresholds for these statistical features to identify abnormal bearing behavior that could indicate the onset of a fault.
This batch-based analysis is designed to be more robust to [object Object] in the vibration data compared to methods that look at individual measurements. By considering the overall statistical properties of the data, the fault detection system can better distinguish normal bearing operation from the early stages of a fault.
The paper evaluates the proposed approach on experimental data collected from a bearing test rig. The results demonstrate that the statistical batch-based method can effectively detect bearing faults and outperform traditional time-domain and frequency-domain analysis techniques.
Critical Analysis
The paper presents a well-designed study that addresses an important problem in machinery condition monitoring. The batch-based statistical approach offers a promising solution for improving the reliability and robustness of bearing fault detection.
One potential limitation is that the method may not be as sensitive to subtle changes in the vibration data as techniques that analyze individual measurements. There could be a tradeoff between the improved noise resilience and the ability to catch faults in their earliest stages.
Additionally, the [object Object] used to trigger fault alarms would likely need to be tuned for each specific application and bearing type. This could require additional data collection and model training to ensure optimal performance.
Further research could explore ways to adaptively set these thresholds or incorporate additional features to enhance the fault detection capabilities. Validating the approach on a wider range of bearing conditions and operating environments would also help demonstrate its real-world applicability.
Conclusion
This paper presents a novel [object Object] for detecting bearing faults in machinery. By analyzing vibration data in batches rather than individual measurements, the method can leverage statistical properties to identify abnormal bearing behavior indicative of developing faults.
The proposed technique offers improvements in robustness and reliability over traditional fault detection methods, which is crucial for real-time condition monitoring applications. While further research is needed to fully optimize the approach, this work represents an important step forward in enhancing the maintenance and reliability of industrial machinery.
This summary was produced with help from an AI and may contain inaccuracies - check out the links to read the original source documents!
Related Papers


0
Statistical Batch-Based Bearing Fault Detection
Victoria Jorry, Zina-Sabrina Duma, Tuomas Sihvonen, Satu-Pia Reinikainen, Lassi Roininen
In the domain of rotating machinery, bearings are vulnerable to different mechanical faults, including ball, inner, and outer race faults. Various techniques can be used in condition-based monitoring, from classical signal analysis to deep learning methods. Based on the complex working conditions of rotary machines, multivariate statistical process control charts such as Hotelling's $T^2$ and Squared Prediction Error are useful for providing early warnings. However, these methods are rarely applied to condition monitoring of rotating machinery due to the univariate nature of the datasets. In the present paper, we propose a multivariate statistical process control-based fault detection method that utilizes multivariate data composed of Fourier transform features extracted for fixed-time batches. Our approach makes use of the multidimensional nature of Fourier transform characteristics, which record more detailed information about the machine's status, in an effort to enhance early defect detection and diagnosis. Experiments with varying vibration measurement locations (Fan End, Drive End), fault types (ball, inner, and outer race faults), and motor loads (0-3 horsepower) are used to validate the suggested approach. The outcomes illustrate our method's effectiveness in fault detection and point to possible broader uses in industrial maintenance.
Read more7/26/2024
🛸

0
Data-driven Machinery Fault Detection: A Comprehensive Review
Dhiraj Neupane, Mohamed Reda Bouadjenek, Richard Dazeley, Sunil Aryal
In this era of advanced manufacturing, it's now more crucial than ever to diagnose machine faults as early as possible to guarantee their safe and efficient operation. With the massive surge in industrial big data and advancement in sensing and computational technologies, data-driven Machinery Fault Diagnosis (MFD) solutions based on machine/deep learning approaches have been used ubiquitously in manufacturing. Timely and accurately identifying faulty machine signals is vital in industrial applications for which many relevant solutions have been proposed and are reviewed in many articles. Despite the availability of numerous solutions and reviews on MFD, existing works often lack several aspects. Most of the available literature has limited applicability in a wide range of manufacturing settings due to their concentration on a particular type of equipment or method of analysis. Additionally, discussions regarding the challenges associated with implementing data-driven approaches, such as dealing with noisy data, selecting appropriate features, and adapting models to accommodate new or unforeseen faults, are often superficial or completely overlooked. Thus, this survey provides a comprehensive review of the articles using different types of machine learning approaches for the detection and diagnosis of various types of machinery faults, highlights their strengths and limitations, provides a review of the methods used for condition-based analyses, comprehensively discusses the available machinery fault datasets, introduces future researchers to the possible challenges they have to encounter while using these approaches for MFD and recommends the probable solutions to mitigate those problems. The future research prospects are also pointed out for a better understanding of the field. We believe this article will help researchers and contribute to the further development of the field.
Read more5/30/2024


0
FaultFormer: Pretraining Transformers for Adaptable Bearing Fault Classification
Anthony Zhou, Amir Barati Farimani
The growth of global consumption has motivated important applications of deep learning to smart manufacturing and machine health monitoring. In particular, analyzing vibration data offers great potential to extract meaningful insights into predictive maintenance by the detection of bearing faults. Deep learning can be a powerful method to predict these mechanical failures; however, they lack generalizability to new tasks or datasets and require expensive, labeled mechanical data. We address this by presenting a novel self-supervised pretraining and fine-tuning framework based on transformer models. In particular, we investigate different tokenization and data augmentation strategies to reach state-of-the-art accuracies using transformer models. Furthermore, we demonstrate self-supervised masked pretraining for vibration signals and its application to low-data regimes, task adaptation, and dataset adaptation. Pretraining is able to improve performance on scarce, unseen training samples, as well as when fine-tuning on fault classes outside of the pretraining distribution. Furthermore, pretrained transformers are shown to be able to generalize to a different dataset in a few-shot manner. This introduces a new paradigm where models can be pretrained on unlabeled data from different bearings, faults, and machinery and quickly deployed to new, data-scarce applications to suit specific manufacturing needs.
Read more5/30/2024
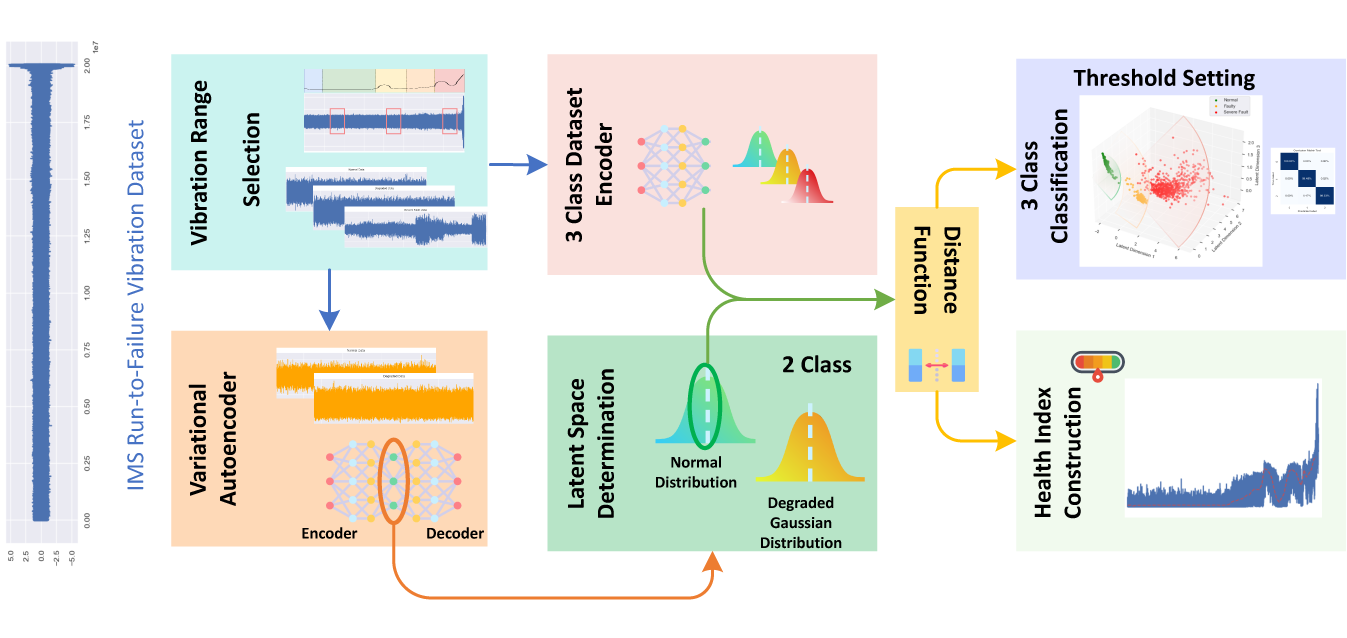

0
Condition Monitoring with Incomplete Data: An Integrated Variational Autoencoder and Distance Metric Framework
Maryam Ahang, Mostafa Abbasi, Todd Charter, Homayoun Najjaran
Condition monitoring of industrial systems is crucial for ensuring safety and maintenance planning, yet notable challenges arise in real-world settings due to the limited or non-existent availability of fault samples. This paper introduces an innovative solution to this problem by proposing a new method for fault detection and condition monitoring for unseen data. Adopting an approach inspired by zero-shot learning, our method can identify faults and assign a relative health index to various operational conditions. Typically, we have plenty of data on normal operations, some data on compromised conditions, and very few (if any) samples of severe faults. We use a variational autoencoder to capture the probabilistic distribution of previously seen and new unseen conditions. The health status is determined by comparing each sample's deviation from a normal operation reference distribution in the latent space. Faults are detected by establishing a threshold for the health indexes, allowing the model to identify severe, unseen faults with high accuracy, even amidst noise. We validate our approach using the run-to-failure IMS-bearing dataset and compare it with other methods. The health indexes generated by our model closely match the established descriptive model of bearing wear, attesting to the robustness and reliability of our method. These findings highlight the potential of our methodology in augmenting fault detection capabilities within industrial domains, thereby contributing to heightened safety protocols and optimized maintenance practices.
Read more7/1/2024