Virtual Foundry Graphnet for Metal Sintering Deformation Prediction

0

Sign in to get full access
Overview
• This paper presents a novel graph neural network (GNN) architecture called the "Virtual Foundry Graphnet" for predicting deformation in metal sintering processes during additive manufacturing.
• The key ideas are to leverage the underlying physical structure and interactions in the sintering process to build a GNN that can accurately predict deformation, and to use this model as part of a digital twin system to optimize the manufacturing process.
Plain English Explanation
3D printing, or additive manufacturing, is a powerful technology for creating complex metal parts. One common 3D printing technique is metal sintering, where metal powder is fused together layer-by-layer. However, predicting how these parts will deform during the sintering process is challenging, as it involves complex physical interactions within the metal powder.
The researchers in this paper developed a new machine learning model called the "Virtual Foundry Graphnet" to address this challenge. The model is based on graph neural networks, which are well-suited for capturing the physical structure and interactions in the sintering process. By training this model on data from simulations and experiments, it can accurately predict how a 3D printed metal part will deform during sintering.
The researchers envision using this model as part of a "digital twin" system for additive manufacturing. A digital twin is a virtual model that mirrors a real-world process, allowing engineers to optimize the process before actually making physical parts. In this case, the Virtual Foundry Graphnet could be used to simulate and predict deformation, enabling manufacturers to adjust the 3D printing parameters to produce parts that meet their specifications.
Technical Explanation
The key innovations in this paper are the design of the Virtual Foundry Graphnet architecture and its application to the metal sintering deformation prediction problem.
The Virtual Foundry Graphnet is a graph neural network that is specifically tailored to capture the physical structure and interactions in the metal sintering process. It takes as input the spatial arrangement of metal powder particles and other process parameters, and outputs predictions of how the part will deform during sintering.
The graph neural network architecture comprises several stages:
- An encoding stage that maps the input powder particle positions and other features into a graph representation.
- A graph convolution stage that propagates information through the graph structure to capture the physical interactions.
- A pooling and decoding stage that aggregates the graph features and outputs the deformation predictions.
The researchers trained and evaluated this model using a combination of simulation data and experimental measurements of sintered parts. They showed that the Virtual Foundry Graphnet outperforms other machine learning approaches, demonstrating its ability to effectively model the complex physics of the sintering process.
Critical Analysis
The researchers thoroughly evaluate the performance of the Virtual Foundry Graphnet and provide a solid technical foundation for the work. However, there are a few potential limitations and areas for further research:
- The model was trained and evaluated on a relatively small dataset, so its performance may be limited by the availability of high-quality training data. [link to paper on automated machine learning for inkjet printing]
- The graph neural network architecture, while tailored to the sintering problem, may be complex and computationally intensive compared to other approaches. Further research is needed to optimize the model size and inference speed. [link to paper on lightweight geometric deep learning for molecular modelling]
- The digital twin application of the model was not fully implemented and evaluated in this work. More research is needed to demonstrate the practical benefits of integrating the Virtual Foundry Graphnet into a real-world additive manufacturing workflow. [link to paper on deep reinforcement learning for toolpath generation]
Overall, the Virtual Foundry Graphnet represents a promising step forward in using machine learning to predict and optimize metal sintering processes. With further refinement and real-world validation, this approach could become a valuable tool for additive manufacturing. [link to paper on lattice-based data-driven modeling for predicting effective Young's modulus]
Conclusion
This paper introduces the Virtual Foundry Graphnet, a novel graph neural network architecture for predicting deformation in metal sintering during additive manufacturing. By leveraging the underlying physical structure and interactions in the sintering process, the model can accurately forecast how 3D printed metal parts will deform.
The researchers envision integrating this model into a digital twin system to optimize the manufacturing process, potentially enabling more consistent and higher-quality metal parts. While further research is needed to address some limitations, the Virtual Foundry Graphnet represents an exciting advancement in the use of machine learning for additive manufacturing.
This summary was produced with help from an AI and may contain inaccuracies - check out the links to read the original source documents!
Related Papers


0
Virtual Foundry Graphnet for Metal Sintering Deformation Prediction
Rachel (Lei), Chen, Juheon Lee, Chuang Gan, Zijiang Yang, Mohammad Amin Nabian, Jun Zeng
Metal Sintering is a necessary step for Metal Injection Molded parts and binder jet such as HP's metal 3D printer. The metal sintering process introduces large deformation varying from 25 to 50% depending on the green part porosity. In this paper, we use a graph-based deep learning approach to predict the part deformation, which can speed up the deformation simulation substantially at the voxel level. Running a well-trained Metal Sintering inferencing engine only takes a range of seconds to obtain the final sintering deformation value. The tested accuracy on example complex geometry achieves 0.7um mean deviation for a 63mm testing part.
Read more4/19/2024
🔮

0
3D object quality prediction for Metal Jet Printer with Multimodal thermal encoder
Rachel (Lei), Chen, Wenjia Zheng, Sandeep Jalui, Pavan Suri, Jun Zeng
With the advancements in 3D printing technologies, it is extremely important that the quality of 3D printed objects, and dimensional accuracies should meet the customer's specifications. Various factors during metal printing affect the printed parts' quality, including the power quality, the printing stage parameters, the print part's location inside the print bed, the curing stage parameters, and the metal sintering process. With the large data gathered from HP's MetJet printing process, AI techniques can be used to analyze, learn, and effectively infer the printed part quality metrics, as well as assist in improving the print yield. In-situ thermal sensing data captured by printer-installed thermal sensors contains the part thermal signature of fusing layers. Such part thermal signature contains a convoluted impact from various factors. In this paper, we use a multimodal thermal encoder network to fuse data of a different nature including the video data vectorized printer control data, and exact part thermal signatures with a trained encoder-decoder module. We explored the data fusing techniques and stages for data fusing, the optimized end-to-end model architecture indicates an improved part quality prediction accuracy.
Read more4/19/2024
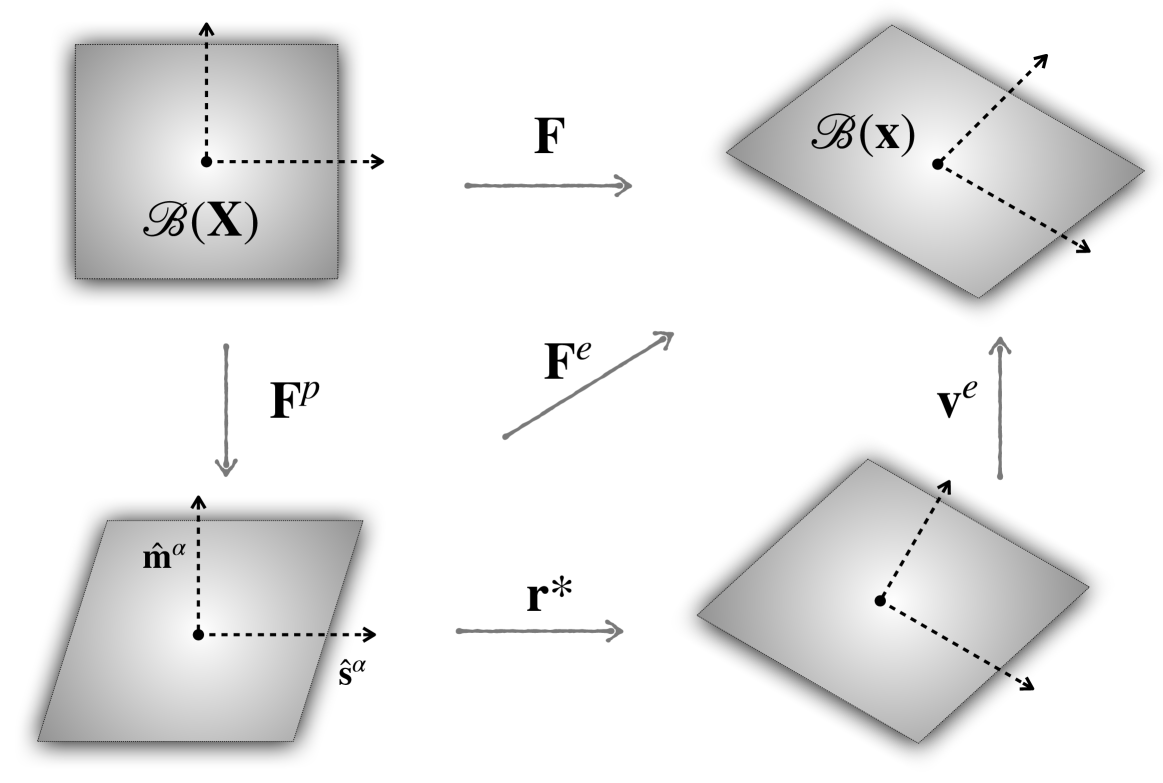

0
Learning polycrystal plasticity using mesh-based subgraph geometric deep learning
Hanfeng Zhai
Polycrystal plasticity in metals is characterized by nonlinear behavior and strain hardening, making numerical models computationally intensive. We employ Graph Neural Network (GNN) to surrogate polycrystal plasticity from finite element method (FEM) simulations. We present a novel message-passing GNN that encodes nodal strain and edge distances between FEM mesh cells, aggregates them to obtain embeddings, and combines the decoded embeddings with the nodal strains to predict stress tensors on graph nodes. We demonstrate training GNN based on subgraphs generated from FEM mesh-graphs, in which the mesh cells are converted to nodes and edges are created between adjacent cells. The GNN is trained on 72 graphs and tested on 18 graphs. We apply the trained GNN to periodic polycrystals and learn the stress-strain maps based on strain-gradient plasticity theory. The GNN is accurately trained based on FEM graphs, in which the $R^2$ for both training and testing sets are 0.993. The proposed GNN plasticity constitutive model speeds up more than 150 times compared with the benchmark FEM method on randomly selected test polycrystals. We also apply the trained GNN to 30 unseen FEM simulations and the GNN generalizes well with an overall $R^2$ of 0.992. Analysis of the von Mises stress distributions in polycrystals shows that the GNN model accurately learns the stress distribution with low error. By comparing the error distribution across training, testing, and unseen datasets, we can deduce that the proposed model does not overfit and generalizes well beyond the training data. This work is expected to pave the way for using graphs as surrogates in polycrystal plasticity modeling.
Read more9/10/2024
🔮

0
Temperature Distribution Prediction in Laser Powder Bed Fusion using Transferable and Scalable Graph Neural Networks
Riddhiman Raut, Amit Kumar Ball, Amrita Basak
This study presents novel predictive models using Graph Neural Networks (GNNs) for simulating thermal dynamics in Laser Powder Bed Fusion (L-PBF) processes. By developing and validating Single-Laser GNN (SL-GNN) and Multi-Laser GNN (ML-GNN) surrogates, the research introduces a scalable data-driven approach that learns fundamental physics from small-scale Finite Element Analysis (FEA) simulations and applies them to larger domains. Achieving a Mean Absolute Percentage Error (MAPE) of 3.77% with the baseline SL-GNN model, GNNs effectively learn from high-resolution simulations and generalize well across larger geometries. The proposed models capture the complexity of the heat transfer process in L-PBF while significantly reducing computational costs. For example, a thermomechanical simulation for a 2 mm x 2 mm domain typically requires about 4 hours, whereas the SL-GNN model can predict thermal distributions almost instantly. Calibrating models to larger domains enhances predictive performance, with significant drops in MAPE for 3 mm x 3 mm and 4 mm x 4 mm domains, highlighting the scalability and efficiency of this approach. Additionally, models show a decreasing trend in Root Mean Square Error (RMSE) when tuned to larger domains, suggesting potential for becoming geometry-agnostic. The interaction of multiple lasers complicates heat transfer, necessitating larger model architectures and advanced feature engineering. Using hyperparameters from Gaussian process-based Bayesian optimization, the best ML-GNN model demonstrates a 46.4% improvement in MAPE over the baseline ML-GNN model. In summary, this approach enables more efficient and flexible predictive modeling in L-PBF additive manufacturing.
Read more7/22/2024