Dual-Arm Construction Robot for Automatic Fixation of Structural Parts to Concrete Surfaces in Narrow Environments

0

Sign in to get full access
INTRODUCTION
The provided text discusses the challenges facing the construction industry, particularly the labor shortage and the decline in younger workers. Construction work often involves physically demanding manual tasks performed outdoors, which has made it less appealing to younger generations. This has led to a shortage of skilled workers, and there are concerns that the necessary skills may not be passed down to future generations, potentially leading to the collapse of the industry.
To address these issues, efforts have been made to automate construction tasks using industrial robots. One such task is the installation of mechanical, electrical, and plumbing (MEP) support systems in concrete surfaces. This involves positioning the structural parts, drilling holes, inserting anchor bolts, and tightening nuts to fix the parts, such as brackets and hangers, to concrete walls and ceilings. Automating these repetitive and precise tasks using robots may help alleviate the labor shortage and maintain the necessary skills in the construction industry.
This paper proposes a robotic system for the complete installation of structural parts on concrete surfaces in construction environments.
The system uses two robot arms - one to position the structural part and the other to fix it in place. This enables both positioning and fixing to be automated, unlike prior systems that only handled hole drilling or anchor bolt insertion.
The robots are designed to be smaller and more mobile than previous solutions, which were large and heavy. This allows the system to operate in the narrow, unstructured spaces common in construction sites. The robots use custom tools that reduce the reaction forces, enabling them to handle heavy-duty tasks like hole drilling despite their smaller size.
The modular design also allows the system to be easily transported to the worksite, overcoming the challenges of maneuvering large, heavy robots through narrow corridors.
The key contributions are: 1) A robotic system design for complete structural part installation in construction environments, 2) Custom tools to enable smaller, low-payload robots to perform heavy tasks, and 3) An efficient procedure for fixing parts in unstructured environments.
PROPOSED DESIGNS AND PROCEDURE
The paper proposes a structural part fixing system design that uses two industrial robots to automate the process of fixing structural parts to concrete. The key aspects of the design are:
-
Independent modular structure: The two robots work in parallel without sharing the same workspace, enabling higher throughput. This also allows for easier integration into construction sites.
-
Custom tool designs: To address the challenges of working in narrow spaces and handling heavy-duty tasks, the paper presents custom designs for the hole drilling tool, anchor hammering tool, and nut tightening tool. These tools minimize reaction forces on the robot.
-
Fixation procedure: The paper outlines a multi-step procedure for the robots to detect the target surface, pick up and position the structural part, drill holes, insert anchors, and tighten the anchor nuts. This procedure is designed to avoid potential errors and efficiently complete the fixation task.
The paper emphasizes that the system is only feasible with short robot arms under 1.3 m, as longer arms would be difficult to operate in narrow construction environments. The custom tool designs are necessary to enable these short arms to handle the required heavy-duty tasks.
IMPLEMENTATION
The experimental setup used to test the proposed custom tools and structural part fixing procedure is described. The setup includes two Denso robots, VM-60B1, that are smaller than robots used in previous approaches. The overall system size is also more compact than in previous work, allowing for easier transportation.
The robots are equipped with various sensors and tools to enable the proposed procedures:
- Force and torque sensors to detect tool contact and overload
- Laser distance sensors to monitor tool and anchor depth
- Tool changers to attach and detach tools
- Cameras with image processing for target detection
Custom control programs were written in the Denso Robot language to allow the robots to adapt their trajectories based on the detected wall orientations and target positions.
The paper describes the implementation of the various tools used, including:
- Hole drilling tools with regular and constant load springs
- An anchor hammering tool with a rubber gripper
- A nut tightening tool with a pulse mechanism to reduce reaction moments
The paper also outlines the methods used for wall orientation estimation and hole detection, which rely on laser distance measurements and image processing techniques, respectively.
V EXPERIMENTAL RESULTS
The paper evaluates the performance of different drilling, anchor hammering, and nut tightening tools for a robotic structural part fixation system.
For drilling, the results show that the tool with a constant load spring, which compensates for the moment caused by the offset drill, was able to successfully drill holes in concrete. Tools without compensation or with a regular spring faced moment overload issues.
The anchor hammering tool was able to successfully hammer anchors into pre-drilled holes without exceeding moment limits.
The nut tightening tool was able to tighten nuts up to 50 Nm of torque without exceeding moment limits, demonstrating its ability to reduce reaction forces on the robot arm.
The overall structural part fixation procedure, including drilling, anchor hammering, and nut tightening, was evaluated and found to be feasible, though the anchor hammering step took the longest due to challenges in finding the pre-drilled hole. Suggestions are made to improve the procedure's efficiency, such as increasing robot speed and using deep learning for hole searching.
CONCLUSION
This study proposes a robot system for automating the complete fixation of structural parts to concrete surfaces. The system has a dual-arm structure that enables it to fix the structural parts. The researchers also developed custom tools that allow smaller robots with lower payloads to be used in narrow environments. The system is designed to be transported in parts to the work environment, and a structural part fixation procedure is proposed.
Experimental results show the proposed robot system, tool designs, and fixation procedure can successfully fix a structural part automatically. Although the system is still a concept and has not been extensively tested, the results indicate its potential for application in the construction field. The fixation procedure is currently fixed, but a study has been conducted to enable dynamic changes to the procedure to recover from failures.
This summary was produced with help from an AI and may contain inaccuracies - check out the links to read the original source documents!
Related Papers


0
Dual-Arm Construction Robot for Automatic Fixation of Structural Parts to Concrete Surfaces in Narrow Environments
Andr'e Yuji Yasutomi, Toshiaki Hatano, Kanta Hamasaki, Makoto Hattori, Daisuke Matsuka
Fixation of structural parts to concrete is a repetitive, heavy-duty, and time-consuming task that requires automation due to the lack of skilled construction workers. Previously developed automation techniques have not achieved the complete fixation of structural parts and are difficult to implement in narrow construction environments. In this study, we propose a construction robot system that enables the complete installation of structural parts to concrete and can be easily introduced to unstructured and narrow construction environments. The system includes two arms that simultaneously position and fix the structural parts, and custom tools that reduce the reaction force applied to the robots so that smaller robots can be used with lower payloads. Due to the modular design of the proposed system, it can be transported in parts for easy introduction to the construction environment. We also propose a procedure for fixing structural parts. Experimental results demonstrate that the custom tools make it possible to use smaller robots without moment overload in the robot joints. Moreover, the results show that the proposed robot system and fixation procedure enable automatic fixation of a structural part to concrete.
Read more4/1/2024


0
Autonomous Robotic Assembly: From Part Singulation to Precise Assembly
Kei Ota, Devesh K. Jha, Siddarth Jain, Bill Yerazunis, Radu Corcodel, Yash Shukla, Antonia Bronars, Diego Romeres
Imagine a robot that can assemble a functional product from the individual parts presented in any configuration to the robot. Designing such a robotic system is a complex problem which presents several open challenges. To bypass these challenges, the current generation of assembly systems is built with a lot of system integration effort to provide the structure and precision necessary for assembly. These systems are mostly responsible for part singulation, part kitting, and part detection, which is accomplished by intelligent system design. In this paper, we present autonomous assembly of a gear box with minimum requirements on structure. The assembly parts are randomly placed in a two-dimensional work environment for the robot. The proposed system makes use of several different manipulation skills such as sliding for grasping, in-hand manipulation, and insertion to assemble the gear box. All these tasks are run in a closed-loop fashion using vision, tactile, and Force-Torque (F/T) sensors. We perform extensive hardware experiments to show the robustness of the proposed methods as well as the overall system. See supplementary video at https://www.youtube.com/watch?v=cZ9M1DQ23OI.
Read more6/12/2024
👁️

0
Vision-Based Adaptive Robotics for Autonomous Surface Crack Repair
Joshua Genova, Eric Cabrera, Vedhus Hoskere
Surface cracks in infrastructure can lead to significant deterioration and costly maintenance if not efficiently repaired. Manual repair methods are labor-intensive, time-consuming, and imprecise and thus difficult to scale to large areas. Breakthroughs in robotic perception and manipulation have advanced autonomous crack repair, but proposed methods lack end-to-end testing and adaptability to changing crack size. This paper presents an adaptive, autonomous system for surface crack detection and repair using robotics with advanced sensing technologies. The system uses an RGB-D camera for crack detection, a laser scanner for precise measurement, and an extruder and pump for material deposition. A novel validation procedure with 3D-printed crack specimens simulates real-world cracks and ensures testing repeatability. Our study shows that an adaptive system for crack filling is more efficient and effective than a fixed-speed approach, with experimental results confirming precision and consistency. This research paves the way for versatile, reliable robotic infrastructure maintenance.
Read more7/25/2024
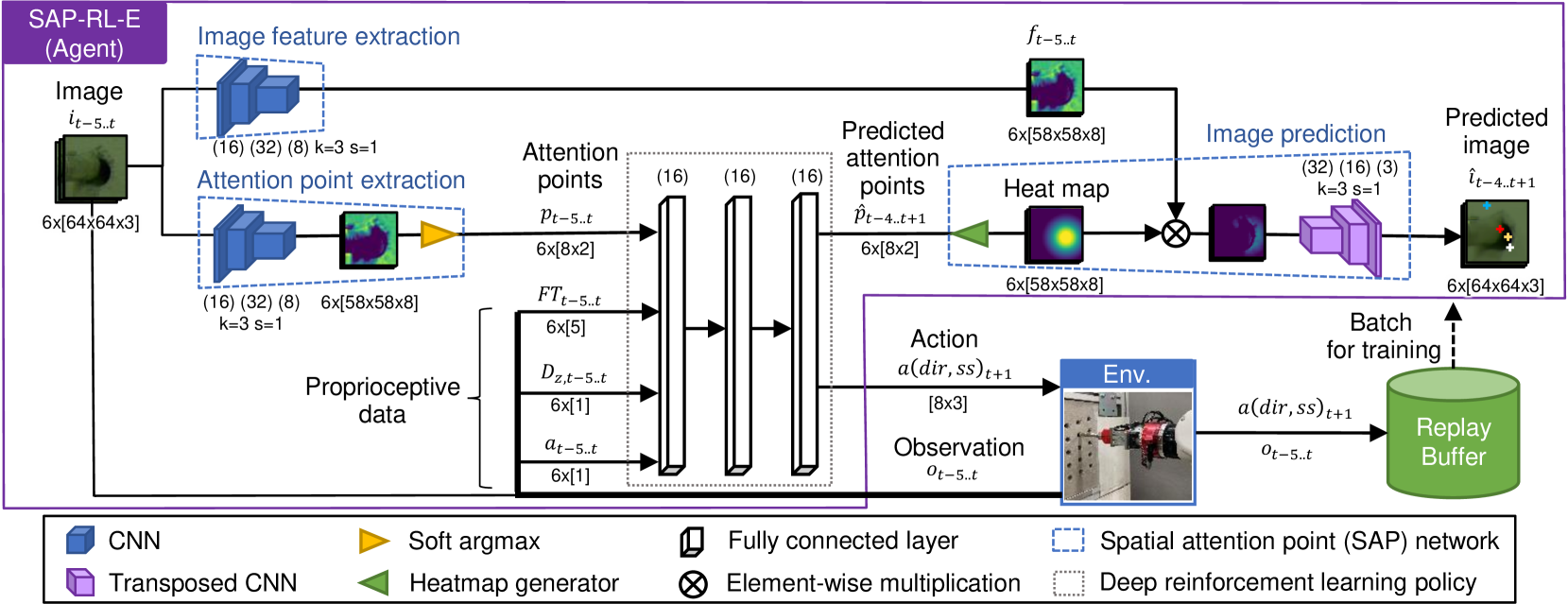

0
Visual Spatial Attention and Proprioceptive Data-Driven Reinforcement Learning for Robust Peg-in-Hole Task Under Variable Conditions
Andr'e Yuji Yasutomi, Hideyuki Ichiwara, Hiroshi Ito, Hiroki Mori, Tetsuya Ogata
Anchor-bolt insertion is a peg-in-hole task performed in the construction field for holes in concrete. Efforts have been made to automate this task, but the variable lighting and hole surface conditions, as well as the requirements for short setup and task execution time make the automation challenging. In this study, we introduce a vision and proprioceptive data-driven robot control model for this task that is robust to challenging lighting and hole surface conditions. This model consists of a spatial attention point network (SAP) and a deep reinforcement learning (DRL) policy that are trained jointly end-to-end to control the robot. The model is trained in an offline manner, with a sample-efficient framework designed to reduce training time and minimize the reality gap when transferring the model to the physical world. Through evaluations with an industrial robot performing the task in 12 unknown holes, starting from 16 different initial positions, and under three different lighting conditions (two with misleading shadows), we demonstrate that SAP can generate relevant attention points of the image even in challenging lighting conditions. We also show that the proposed model enables task execution with higher success rate and shorter task completion time than various baselines. Due to the proposed model's high effectiveness even in severe lighting, initial positions, and hole conditions, and the offline training framework's high sample-efficiency and short training time, this approach can be easily applied to construction.
Read more4/1/2024