Examining the simulation-to-reality gap of a wheel loader digging in deformable terrain
2310.05765

0

0
🛠️
Abstract
We investigate how well a physics-based simulator can replicate a real wheel loader performing bucket filling in a pile of soil. The comparison is made using field test time series of the vehicle motion and actuation forces, loaded mass, and total work. The vehicle was modeled as a rigid multibody system with frictional contacts, driveline, and linear actuators. For the soil, we tested discrete element models of different resolutions, with and without multiscale acceleration. The spatio-temporal resolution ranged between 50-400 mm and 2-500 ms, and the computational speed was between 1/10,000 to 5 times faster than real-time. The simulation-to-reality gap was found to be around 10% and exhibited a weak dependence on the level of fidelity, e.g., compatible with real-time simulation. Furthermore, the sensitivity of an optimized force feedback controller under transfer between different simulation domains was investigated. The domain bias was observed to cause a performance reduction of 5% despite the domain gap being about 15%.
Create account to get full access
Overview
- Investigates how well a physics-based simulator can replicate the real-world performance of a wheel loader during bucket filling in a soil pile
- Compares simulation results to field test data on vehicle motion, actuation forces, loaded mass, and total work
- Explores the impact of simulation fidelity, from low to high, and its effect on computational speed
- Examines the sensitivity of an optimized force feedback controller when transferred between different simulation domains
Plain English Explanation
This research paper explores how well a computer simulation can mimic the real-world performance of a wheel loader as it fills its bucket with soil. The researchers compared the simulation results to actual field test data, looking at things like the vehicle's motion, the forces acting on it, the weight of the loaded soil, and the total amount of work done.
They tested different levels of detail in the simulation, from low to high, and found that the simulation was able to closely match the real-world results, with an accuracy of around 90%. Interestingly, they also found that the level of detail in the simulation didn't have a huge impact on the accuracy - even a relatively simple simulation could provide results that were close to reality.
The researchers also looked at how a controller designed to provide feedback to the wheel loader operator would perform when transferred between different simulation environments. They found that even a small difference between the simulations could cause the controller to perform slightly worse, with a 5% reduction in performance.
Overall, this research suggests that physics-based simulations can be a powerful tool for studying the performance of heavy machinery like wheel loaders, and that even relatively simple simulations can provide useful insights. The findings could help engineers design better equipment and control systems, and could also be useful for transferring skills from simulation to the real world or optimizing the design of virtual reality systems for biomechanical testing.
Technical Explanation
The researchers modeled the wheel loader as a rigid multibody system with frictional contacts, a driveline, and linear actuators. For the soil, they tested different discrete element models with varying levels of spatial and temporal resolution, ranging from 50-400 mm and 2-500 ms, respectively. The computational speed of the simulations ranged from 1/10,000 to 5 times faster than real-time.
The researchers compared the simulation results to field test data on the vehicle's motion, actuation forces, loaded mass, and total work. They found that the simulation-to-reality gap was around 10%, and that this gap exhibited a weak dependence on the level of simulation fidelity, suggesting that even a relatively low-fidelity simulation could provide accurate results.
Furthermore, the researchers investigated the sensitivity of an optimized force feedback controller when transferred between different simulation domains. They observed a performance reduction of 5% due to the domain bias, despite the overall simulation-to-reality gap being around 15%.
Critical Analysis
The paper provides a comprehensive evaluation of the ability of physics-based simulations to replicate the real-world performance of a wheel loader during bucket filling. The researchers have thoroughly tested the simulation models across a range of fidelity levels and computational speeds, and their findings suggest that even relatively simple simulations can achieve a high degree of accuracy.
One potential limitation of the study is that it focuses on a single scenario, namely bucket filling in a pile of soil. It would be interesting to see how the simulation performance holds up in other operating conditions, such as motion planning and trajectory optimization or different types of terrain and soil conditions.
Additionally, the researchers note that the sensitivity of the force feedback controller to the simulation domain could be an important consideration for applications that rely on transferring control systems between simulation and the real world. Further investigation into the factors that contribute to this domain bias could help researchers develop more robust control strategies.
Overall, this paper makes a valuable contribution to the field of physics-based simulation for heavy machinery, and its findings could have implications for a variety of applications, from equipment design to virtual training and testing.
Conclusion
This research paper demonstrates the impressive capabilities of physics-based simulations in replicating the real-world performance of a wheel loader during bucket filling operations. The researchers found that the simulation-to-reality gap was only around 10%, and that this gap was relatively insensitive to the level of simulation fidelity. This suggests that even relatively simple simulations can provide accurate results, which could be useful for a range of applications, from equipment design to virtual training and testing.
The paper also highlights the importance of considering the impact of simulation domain bias when transferring control systems between simulation and the real world. This is a crucial consideration for skill transfer and trajectory optimization applications, and further research in this area could lead to the development of more robust control strategies.
Overall, this research represents an important step forward in the field of physics-based simulation for heavy machinery, and its findings could have far-reaching implications for a variety of industries and applications.
This summary was produced with help from an AI and may contain inaccuracies - check out the links to read the original source documents!
Related Papers
🧠
World Modeling for Autonomous Wheel Loaders
Koji Aoshima, Arvid Falldin, Eddie Wadbro, Martin Servin

0

0
This paper presents a method for learning world models for wheel loaders performing automatic loading actions on a pile of soil. Data-driven models were learned to output the resulting pile state, loaded mass, time, and work for a single loading cycle given inputs that include a heightmap of the initial pile shape and action parameters for an automatic bucket-filling controller. Long-horizon planning of sequential loading in a dynamically changing environment is thus enabled as repeated model inference. The models, consisting of deep neural networks, were trained on data from 3D multibody dynamics simulation of over 10,000 random loading actions in gravel piles of different shapes. The accuracy and inference time for predicting the loading performance and the resulting pile state were, on average, 95% in 1.2 ms and 97% in 4.5 ms, respectively. Long-horizon predictions were found feasible over 40 sequential loading actions.
5/30/2024
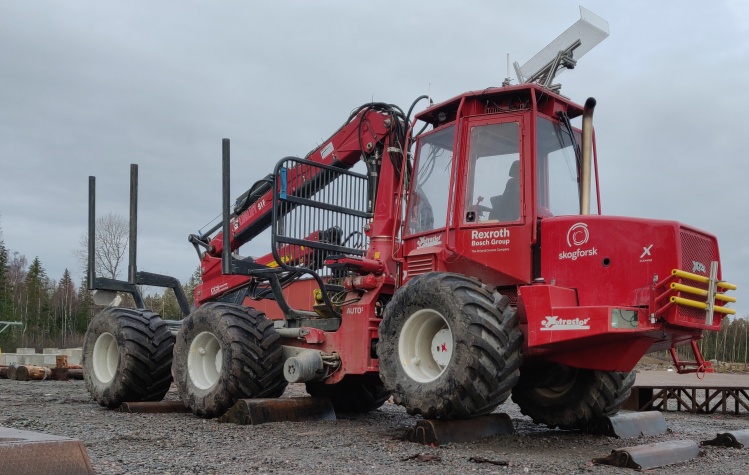
Sim-to-real transfer of active suspension control using deep reinforcement learning
Viktor Wiberg, Erik Wallin, Arvid Falldin, Tobias Semberg, Morgan Rossander, Eddie Wadbro, Martin Servin

0

0
We explore sim-to-real transfer of deep reinforcement learning controllers for a heavy vehicle with active suspensions designed for traversing rough terrain. While related research primarily focuses on lightweight robots with electric motors and fast actuation, this study uses a forestry vehicle with a complex hydraulic driveline and slow actuation. We simulate the vehicle using multibody dynamics and apply system identification to find an appropriate set of simulation parameters. We then train policies in simulation using various techniques to mitigate the sim-to-real gap, including domain randomization, action delays, and a reward penalty to encourage smooth control. In reality, the policies trained with action delays and a penalty for erratic actions perform nearly at the same level as in simulation. In experiments on level ground, the motion trajectories closely overlap when turning to either side, as well as in a route tracking scenario. When faced with a ramp that requires active use of the suspensions, the simulated and real motions are in close alignment. This shows that the actuator model together with system identification yields a sufficiently accurate model of the actuators. We observe that policies trained without the additional action penalty exhibit fast switching or bang-bang control. These present smooth motions and high performance in simulation but transfer poorly to reality. We find that policies make marginal use of the local height map for perception, showing no indications of predictive planning. However, the strong transfer capabilities entail that further development concerning perception and performance can be largely confined to simulation.
5/1/2024

Using physics-based simulation towards eliminating empiricism in extraterrestrial terramechanics applications
Wei Hu, Pei Li, Arno Rogg, Alexander Schepelmann, Colin Creager, Samuel Chandler, Ken Kamrin, Dan Negrut

0

0
Recently, there has been a surge of international interest in extraterrestrial exploration targeting the Moon, Mars, the moons of Mars, and various asteroids. This contribution discusses how current state-of-the-art Earth-based testing for designing rovers and landers for these missions currently leads to overly optimistic conclusions about the behavior of these devices upon deployment on the targeted celestial bodies. The key misconception is that gravitational offset is necessary during the textit{terramechanics} testing of rover and lander prototypes on Earth. The body of evidence supporting our argument is tied to a small number of studies conducted during parabolic flights and insights derived from newly revised scaling laws. We argue that what has prevented the community from fully diagnosing the problem at hand is the absence of effective physics-based models capable of simulating terramechanics under low gravity conditions. We developed such a physics-based simulator and utilized it to gauge the mobility of early prototypes of the Volatiles Investigating Polar Exploration Rover (VIPER), which is slated to depart for the Moon in November 2024. This contribution discusses the results generated by this simulator, how they correlate with physical test results from the NASA-Glenn SLOPE lab, and the fallacy of the gravitational offset in rover and lander testing. The simulator developed is open sourced and made publicly available for unfettered use; it can support principled studies that extend beyond trafficability analysis to provide insights into in-situ resource utilization activities, e.g., digging, bulldozing, and berming in low gravity.
5/21/2024

A High-Fidelity Simulation Framework for Grasping Stability Analysis in Human Casualty Manipulation
Qianwen Zhao, Rajarshi Roy, Chad Spurlock, Kevin Lister, Long Wang

0

0
Recently, there has been a growing interest in rescue robots due to their vital role in addressing emergency scenarios and providing crucial support in challenging or hazardous situations where human intervention is difficult. However, very few of these robots are capable of actively engaging with humans and undertaking physical manipulation tasks. This limitation is largely attributed to the absence of tools that can realistically simulate physical interactions, especially the contact mechanisms between a robotic gripper and a human body. In this letter, we aim to address key limitations in current developments towards robotic casualty manipulation. Firstly, we present an integrative simulation framework for casualty manipulation. We adapt a finite element method (FEM) tool into the grasping and manipulation scenario, and the developed framework can provide accurate biomechanical reactions resulting from manipulation. Secondly, we conduct a detailed assessment of grasping stability during casualty grasping and manipulation simulations. To validate the necessity and superior performance of the proposed high-fidelity simulation framework, we conducted a qualitative and quantitative comparison of grasping stability analyses between the proposed framework and the state-of-the-art multi-body physics simulations. Through these efforts, we have taken the first step towards a feasible solution for robotic casualty manipulation.
4/8/2024