Integrating knowledge-guided symbolic regression and model-based design of experiments to automate process flow diagram development

0
↗️
Sign in to get full access
Overview
- New products must be formulated rapidly to succeed in the global market, but key product indicators can be complex and poorly understood
- Current scale-up processes rely on expensive trial-and-error campaigns
- This work proposes a novel digital framework to automatically quantify process mechanisms by integrating symbolic regression within model-based design of experiments
- The framework can effectively discover ground-truth process mechanisms within a few iterations, indicating its potential for use in digital manufacturing and product innovation
Plain English Explanation
Developing new products quickly is crucial for success in the global market. However, the key indicators that show how well a product is performing can be complex and not well understood. This makes it difficult to scale up production from small-scale testing to full manufacturing. Companies currently have to rely on a lot of expensive trial-and-error to figure out the right production process.
This research proposes a new digital framework to automatically identify the underlying mechanisms driving product performance. It does this by combining two key techniques: symbolic regression and model-based design of experiments.
Symbolic regression can find simple mathematical expressions that explain the relationship between product properties and the manufacturing process. Then, the model-based design of experiments helps figure out the best new experiments to run in order to further improve the process.
By iterating between these two techniques, the framework can quickly zero in on the true mechanisms driving product performance. This could be a big help for companies trying to innovate and scale up new products in a fast-paced global market.
Technical Explanation
The researchers developed a novel digital framework that integrates symbolic regression and model-based design of experiments to automatically quantify the underlying process mechanisms governing formulated product synthesis.
In each iteration, the symbolic regression component proposes a Pareto front of interpretable mechanistic expressions that explain the relationships between process inputs and key product indicators. The model-based design of experiments then selects the most informative new experiments to run in order to further discriminate between the proposed models while also optimizing the overall process.
To investigate the framework's performance, the researchers constructed a new process model capable of simulating general formulated product synthesis. They used this model to generate in-silico data for different case studies. The results showed that the framework could effectively discover the ground-truth process mechanisms within just a few iterations.
This indicates the great potential of the proposed framework for accelerating digital manufacturing and product innovation in the chemical industry. By automatically uncovering the underlying process knowledge, it can help companies rapidly develop and scale up new formulated products to succeed in the global market.
Critical Analysis
The paper presents a promising framework for accelerating process optimization and knowledge discovery, but there are a few caveats to consider:
- The evaluation was limited to in-silico data generated by a synthetic process model, so further validation on real-world industrial data would be needed to fully assess the framework's capabilities [link to physics-constrained-robust-learning-open-form-partial].
- The paper does not address potential challenges in scaling the framework to highly complex, large-scale processes with many variables and constraints [link to gplasdi-gaussian-process-based-interpretable-latent-space].
- While the framework aims to provide interpretable mechanistic expressions, the fidelity and practicality of these models for industrial decision-making is not thoroughly discussed [link to mardiflow-cse-workflow-framework-abstracting-meta-data].
Overall, this research demonstrates an interesting approach to leverage model-based experimentation and symbolic regression for accelerating process development. Further work is needed to validate the framework's performance on real-world industrial problems and address scalability challenges for broader adoption in the chemical industry.
Conclusion
This paper presents a novel digital framework that integrates symbolic regression and model-based design of experiments to automatically uncover the underlying process mechanisms governing formulated product synthesis.
By iteratively proposing interpretable mechanistic models and designing informative experiments, the framework was shown to effectively discover the ground-truth process drivers within just a few iterations using synthetic data. This indicates its strong potential to accelerate digital manufacturing and product innovation in the chemical industry, where rapidly developing and scaling up new formulated products is crucial for success in the global market.
While further validation on real-world industrial data is needed, this research demonstrates an interesting approach to leverage advanced modeling and experimentation techniques to gain deep process understanding and enable more efficient product development.
This summary was produced with help from an AI and may contain inaccuracies - check out the links to read the original source documents!
Related Papers
↗️

0
Integrating knowledge-guided symbolic regression and model-based design of experiments to automate process flow diagram development
Alexander W. Rogers, Amanda Lane, Cesar Mendoza, Simon Watson, Adam Kowalski, Philip Martin, Dongda Zhang
New products must be formulated rapidly to succeed in the global formulated product market; however, key product indicators (KPIs) can be complex, poorly understood functions of the chemical composition and processing history. Consequently, scale-up must currently undergo expensive trial-and-error campaigns. To accelerate process flow diagram (PFD) optimisation and knowledge discovery, this work proposed a novel digital framework to automatically quantify process mechanisms by integrating symbolic regression (SR) within model-based design of experiments (MBDoE). Each iteration, SR proposed a Pareto front of interpretable mechanistic expressions, and then MBDoE designed a new experiment to discriminate between them while balancing PFD optimisation. To investigate the framework's performance, a new process model capable of simulating general formulated product synthesis was constructed to generate in-silico data for different case studies. The framework could effectively discover ground-truth process mechanisms within a few iterations, indicating its great potential for use within the general chemical industry for digital manufacturing and product innovation.
Read more5/9/2024


0
Towards Human-Level Understanding of Complex Process Engineering Schematics: A Pedagogical, Introspective Multi-Agent Framework for Open-Domain Question Answering
Sagar Srinivas Sakhinana, Geethan Sannidhi, Venkataramana Runkana
In the chemical and process industries, Process Flow Diagrams (PFDs) and Piping and Instrumentation Diagrams (P&IDs) are critical for design, construction, and maintenance. Recent advancements in Generative AI, such as Large Multimodal Models (LMMs) like GPT4 (Omni), have shown promise in understanding and interpreting process diagrams for Visual Question Answering (VQA). However, proprietary models pose data privacy risks, and their computational complexity prevents knowledge editing for domain-specific customization on consumer hardware. To overcome these challenges, we propose a secure, on-premises enterprise solution using a hierarchical, multi-agent Retrieval Augmented Generation (RAG) framework for open-domain question answering (ODQA) tasks, offering enhanced data privacy, explainability, and cost-effectiveness. Our novel multi-agent framework employs introspective and specialized sub-agents using open-source, small-scale multimodal models with the ReAct (Reason+Act) prompting technique for PFD and P&ID analysis, integrating multiple information sources to provide accurate and contextually relevant answers. Our approach, supported by iterative self-correction, aims to deliver superior performance in ODQA tasks. We conducted rigorous experimental studies, and the empirical results validated the proposed approach effectiveness.
Read more9/4/2024


0
Discovering deposition process regimes: leveraging unsupervised learning for process insights, surrogate modeling, and sensitivity analysis
Geremy Loacham'in Suntaxi, Paris Papavasileiou, Eleni D. Koronaki, Dimitrios G. Giovanis, Georgios Gakis, Ioannis G. Aviziotis, Martin Kathrein, Gabriele Pozzetti, Christoph Czettl, St'ephane P. A. Bordas, Andreas G. Boudouvis
This work introduces a comprehensive approach utilizing data-driven methods to elucidate the deposition process regimes in Chemical Vapor Deposition (CVD) reactors and the interplay of physical mechanism that dominate in each one of them. Through this work, we address three key objectives. Firstly, our methodology relies on process outcomes, derived by a detailed CFD model, to identify clusters of outcomes corresponding to distinct process regimes, wherein the relative influence of input variables undergoes notable shifts. This phenomenon is experimentally validated through Arrhenius plot analysis, affirming the efficacy of our approach. Secondly, we demonstrate the development of an efficient surrogate model, based on Polynomial Chaos Expansion (PCE), that maintains accuracy, facilitating streamlined computational analyses. Finally, as a result of PCE, sensitivity analysis is made possible by means of Sobol' indices, that quantify the impact of process inputs across identified regimes. The insights gained from our analysis contribute to the formulation of hypotheses regarding phenomena occurring beyond the transition regime. Notably, the significance of temperature even in the diffusion-limited regime, as evidenced by the Arrhenius plot, suggests activation of gas phase reactions at elevated temperatures. Importantly, our proposed methods yield insights that align with experimental observations and theoretical principles, aiding decision-making in process design and optimization. By circumventing the need for costly and time-consuming experiments, our approach offers a pragmatic pathway towards enhanced process efficiency. Moreover, this study underscores the potential of data-driven computational methods for innovating reactor design paradigms.
Read more5/30/2024
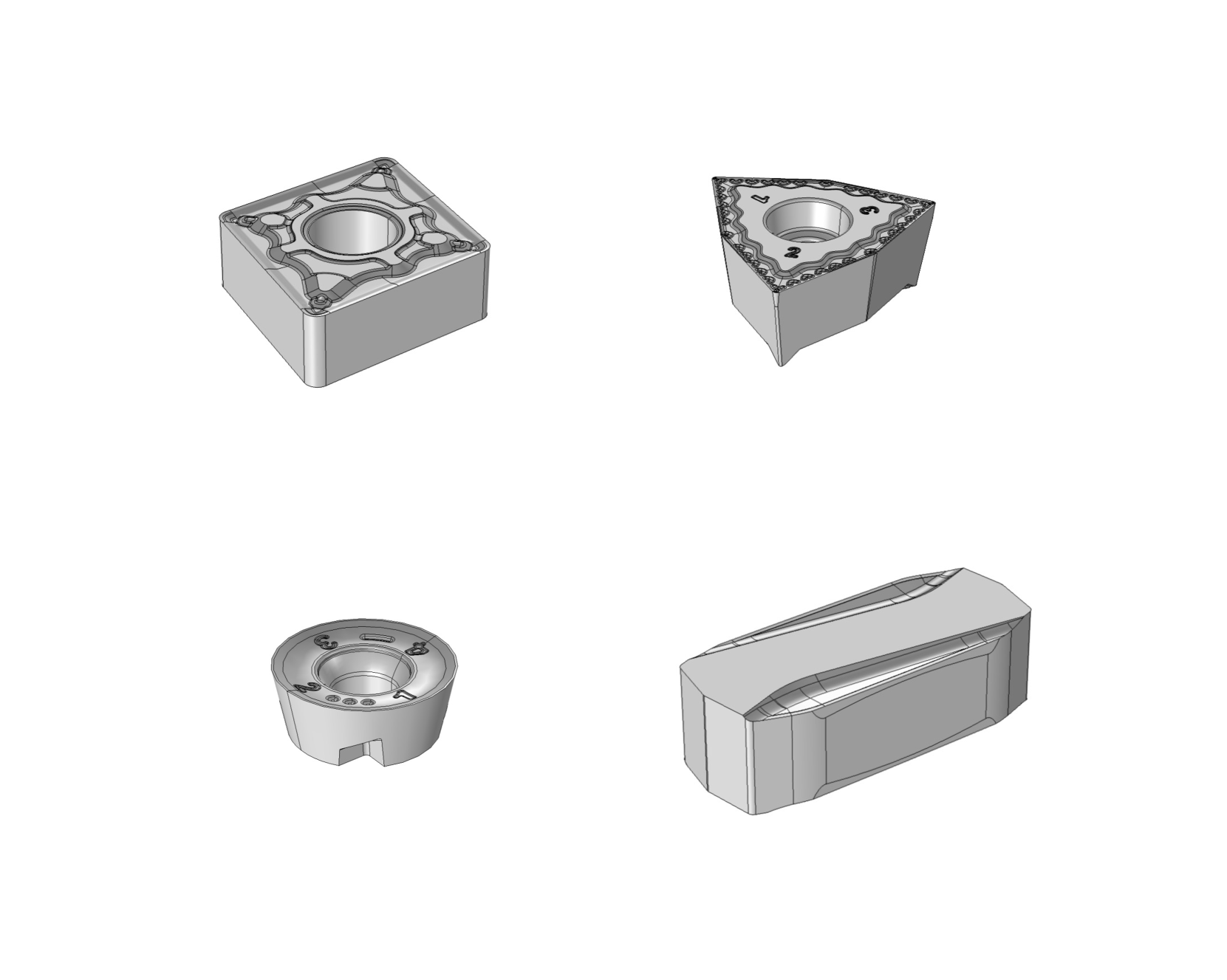

0
Integrating supervised and unsupervised learning approaches to unveil critical process inputs
Paris Papavasileiou, Dimitrios G. Giovanis, Gabriele Pozzetti, Martin Kathrein, Christoph Czettl, Ioannis G. Kevrekidis, Andreas G. Boudouvis, St'ephane P. A. Bordas, Eleni D. Koronaki
This study introduces a machine learning framework tailored to large-scale industrial processes characterized by a plethora of numerical and categorical inputs. The framework aims to (i) discern critical parameters influencing the output and (ii) generate accurate out-of-sample qualitative and quantitative predictions of production outcomes. Specifically, we address the pivotal question of the significance of each input in shaping the process outcome, using an industrial Chemical Vapor Deposition (CVD) process as an example. The initial objective involves merging subject matter expertise and clustering techniques exclusively on the process output, here, coating thickness measurements at various positions in the reactor. This approach identifies groups of production runs that share similar qualitative characteristics, such as film mean thickness and standard deviation. In particular, the differences of the outcomes represented by the different clusters can be attributed to differences in specific inputs, indicating that these inputs are critical for the production outcome. Leveraging this insight, we subsequently implement supervised classification and regression methods using the identified critical process inputs. The proposed methodology proves to be valuable in scenarios with a multitude of inputs and insufficient data for the direct application of deep learning techniques, providing meaningful insights into the underlying processes.
Read more5/14/2024