Integrating supervised and unsupervised learning approaches to unveil critical process inputs

0
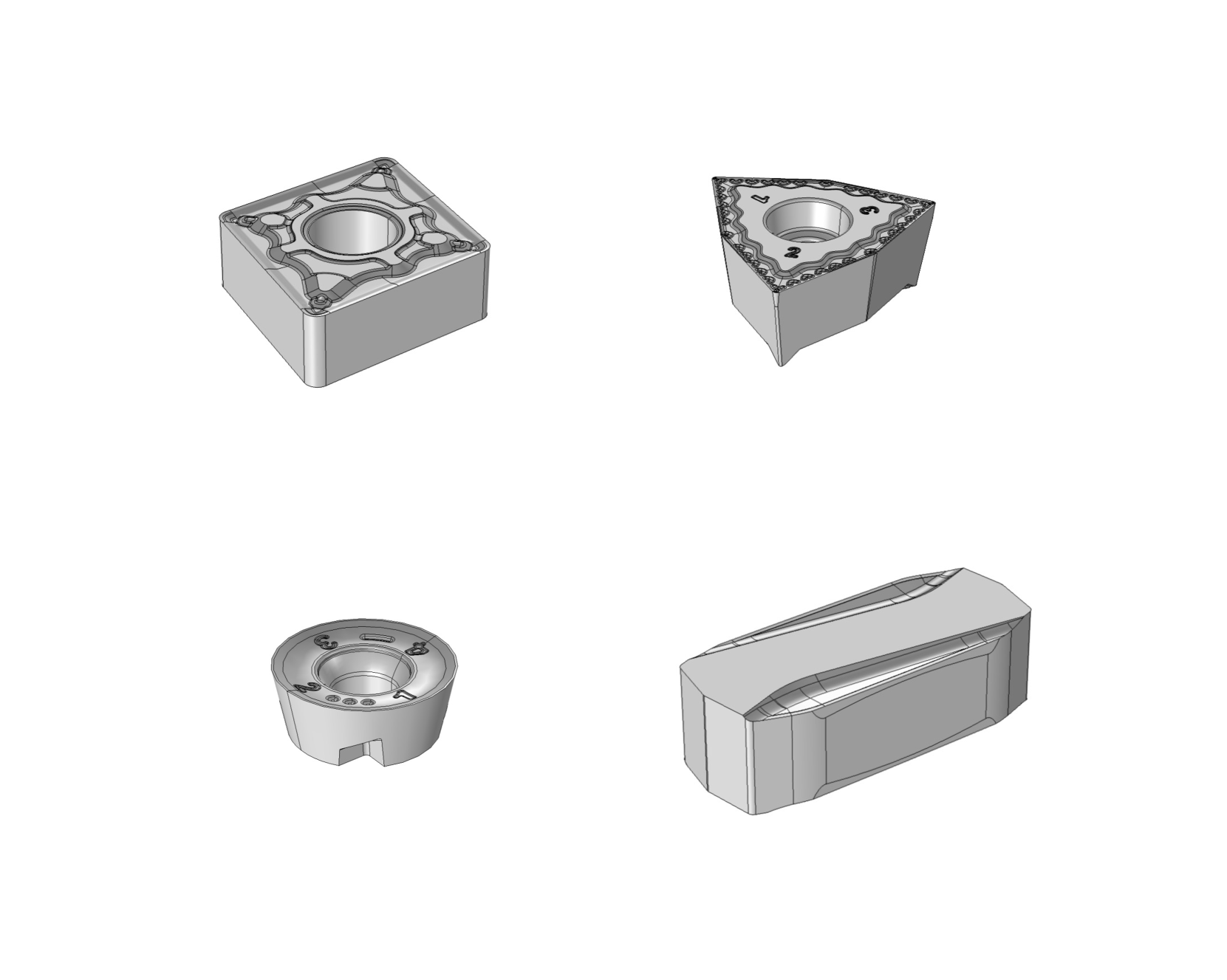
Sign in to get full access
Overview
- This paper explores an approach that combines supervised and unsupervised learning to identify critical process inputs in industrial settings.
- The proposed method aims to integrate the strengths of both supervised and unsupervised techniques to uncover key variables that impact process performance.
- The paper presents a case study demonstrating the application of this hybrid approach to a real-world industrial process.
Plain English Explanation
In industrial processes, understanding which input variables have the greatest impact on the final product or process outcome is crucial for optimizing performance and efficiency. This paper describes a method that combines two different machine learning approaches - supervised learning and unsupervised learning - to identify these critical process inputs.
Supervised learning is a type of machine learning where the algorithm is trained on a dataset with known outcomes, allowing it to learn patterns and make predictions. Unsupervised learning, on the other hand, does not rely on pre-labeled data and instead tries to uncover hidden structures and relationships within the data.
The researchers in this paper hypothesized that by integrating these two approaches, they could leverage the strengths of each to better understand the key factors influencing the industrial process. The supervised learning component could help identify the most important variables, while the unsupervised learning component could reveal previously unknown relationships or patterns in the data.
To test this, the researchers applied their hybrid approach to a real-world industrial case study. They collected data on various input variables (such as temperatures, pressures, and flow rates) as well as the final process outcomes. By combining supervised and unsupervised techniques, they were able to pinpoint the critical process inputs that had the greatest impact on the desired outcomes.
This type of analysis can be incredibly valuable for industrial operators, as it allows them to focus their efforts on optimizing the most important process variables, leading to improved quality, increased efficiency, and reduced waste.
Technical Explanation
The paper presents a novel approach that integrates supervised and unsupervised learning methods to identify critical process inputs in industrial settings. The proposed framework combines the strengths of both techniques to uncover key variables that influence process performance.
The supervised learning component of the approach uses regression models to quantify the relationship between process inputs and outputs. This allows the researchers to rank the variables based on their relative importance in predicting the desired process outcomes.
The unsupervised learning component, on the other hand, leverages clustering algorithms to identify hidden patterns and relationships within the process data. By grouping similar observations together, the unsupervised analysis can reveal underlying structures or subgroups that may not be obvious from the supervised modeling alone.
The researchers then integrate the insights from the supervised and unsupervised analyses to develop a comprehensive understanding of the critical process inputs. This hybrid approach is demonstrated through a case study involving a real-world industrial process, where the authors successfully identify the key variables driving the desired process outputs.
The findings from this research can have significant implications for industrial process optimization. By pinpointing the most influential process inputs, operators can focus their efforts on controlling and fine-tuning these variables, leading to improved quality, increased efficiency, and reduced waste. The integration of supervised and unsupervised techniques also provides a more holistic view of the process dynamics, potentially uncovering relationships that would not be captured by either approach in isolation.
Critical Analysis
The authors of this paper have put forth a compelling approach that leverages the complementary strengths of supervised and unsupervised learning to uncover critical process inputs. The case study demonstration provided valuable insights into the practical application of this hybrid methodology.
One notable aspect of the research is the authors' recognition of the limitations of using either supervised or unsupervised learning alone. By combining these two techniques, they were able to obtain a more comprehensive understanding of the underlying process dynamics, which is a significant contribution to the field of industrial process optimization.
However, the paper does not extensively discuss the potential challenges or caveats associated with the proposed approach. For example, the researchers could have explored the sensitivity of the results to the choice of supervised and unsupervised algorithms, or the impact of data quality and availability on the performance of the hybrid method.
Additionally, while the case study provided a valuable demonstration, it would be informative to see the approach applied to a wider range of industrial processes to assess its generalizability and robustness. Expanding the evaluation to include processes with different characteristics, such as complex nonlinear relationships or limited process supervision, could further validate the utility of the proposed framework.
Another area for potential exploration is the integration of domain-specific knowledge or process models into the hybrid approach. Incorporating such prior information could enhance the interpretability of the identified critical inputs and potentially lead to even more accurate and reliable process optimization strategies.
Overall, this paper presents a promising direction for leveraging the synergies between supervised and unsupervised learning to address an important challenge in industrial process management. The authors' work serves as a solid foundation for future research to build upon, exploring ways to further refine and expand the capabilities of this hybrid methodology.
Conclusion
This paper introduces a novel approach that combines supervised and unsupervised learning techniques to identify critical process inputs in industrial settings. By integrating the strengths of both methods, the researchers were able to develop a more comprehensive understanding of the key variables driving process performance.
The proposed hybrid approach was demonstrated through a case study, where the authors successfully applied the method to a real-world industrial process. The findings from this research can have significant implications for industrial operators, as the ability to pinpoint the most influential process inputs can lead to improved quality, increased efficiency, and reduced waste.
The critical analysis highlights the potential of this approach, as well as areas for future research and refinement. Exploring the sensitivity of the results, expanding the evaluation to a broader range of industrial processes, and incorporating domain-specific knowledge or process models could further enhance the capabilities of this hybrid methodology.
Overall, this work represents an important step forward in the integration of machine learning techniques for industrial process optimization. By leveraging the complementary strengths of supervised and unsupervised learning, researchers and practitioners can uncover valuable insights and drive continuous improvement in complex industrial systems.
This summary was produced with help from an AI and may contain inaccuracies - check out the links to read the original source documents!
Related Papers
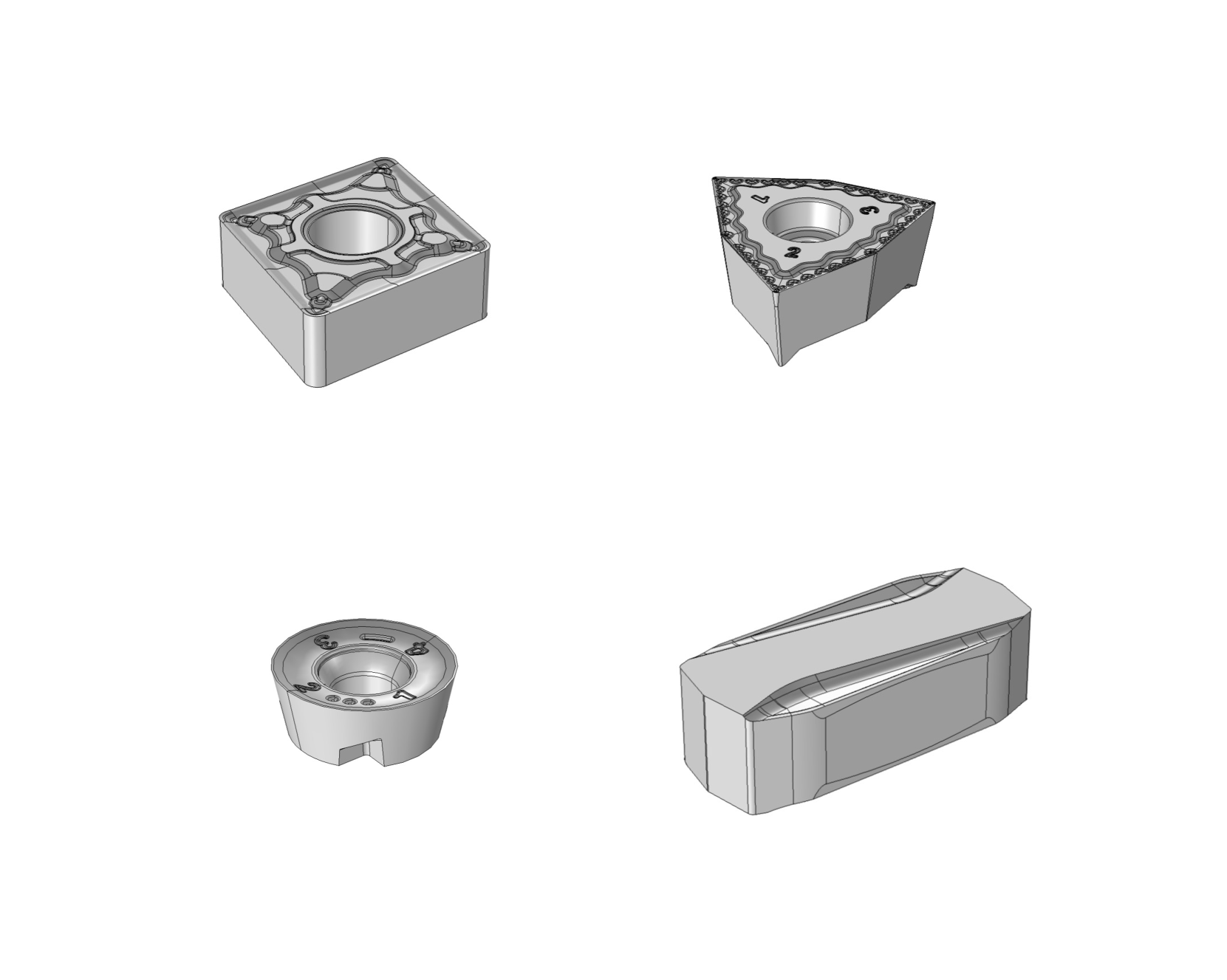

0
Integrating supervised and unsupervised learning approaches to unveil critical process inputs
Paris Papavasileiou, Dimitrios G. Giovanis, Gabriele Pozzetti, Martin Kathrein, Christoph Czettl, Ioannis G. Kevrekidis, Andreas G. Boudouvis, St'ephane P. A. Bordas, Eleni D. Koronaki
This study introduces a machine learning framework tailored to large-scale industrial processes characterized by a plethora of numerical and categorical inputs. The framework aims to (i) discern critical parameters influencing the output and (ii) generate accurate out-of-sample qualitative and quantitative predictions of production outcomes. Specifically, we address the pivotal question of the significance of each input in shaping the process outcome, using an industrial Chemical Vapor Deposition (CVD) process as an example. The initial objective involves merging subject matter expertise and clustering techniques exclusively on the process output, here, coating thickness measurements at various positions in the reactor. This approach identifies groups of production runs that share similar qualitative characteristics, such as film mean thickness and standard deviation. In particular, the differences of the outcomes represented by the different clusters can be attributed to differences in specific inputs, indicating that these inputs are critical for the production outcome. Leveraging this insight, we subsequently implement supervised classification and regression methods using the identified critical process inputs. The proposed methodology proves to be valuable in scenarios with a multitude of inputs and insufficient data for the direct application of deep learning techniques, providing meaningful insights into the underlying processes.
Read more5/14/2024


0
Discovering deposition process regimes: leveraging unsupervised learning for process insights, surrogate modeling, and sensitivity analysis
Geremy Loacham'in Suntaxi, Paris Papavasileiou, Eleni D. Koronaki, Dimitrios G. Giovanis, Georgios Gakis, Ioannis G. Aviziotis, Martin Kathrein, Gabriele Pozzetti, Christoph Czettl, St'ephane P. A. Bordas, Andreas G. Boudouvis
This work introduces a comprehensive approach utilizing data-driven methods to elucidate the deposition process regimes in Chemical Vapor Deposition (CVD) reactors and the interplay of physical mechanism that dominate in each one of them. Through this work, we address three key objectives. Firstly, our methodology relies on process outcomes, derived by a detailed CFD model, to identify clusters of outcomes corresponding to distinct process regimes, wherein the relative influence of input variables undergoes notable shifts. This phenomenon is experimentally validated through Arrhenius plot analysis, affirming the efficacy of our approach. Secondly, we demonstrate the development of an efficient surrogate model, based on Polynomial Chaos Expansion (PCE), that maintains accuracy, facilitating streamlined computational analyses. Finally, as a result of PCE, sensitivity analysis is made possible by means of Sobol' indices, that quantify the impact of process inputs across identified regimes. The insights gained from our analysis contribute to the formulation of hypotheses regarding phenomena occurring beyond the transition regime. Notably, the significance of temperature even in the diffusion-limited regime, as evidenced by the Arrhenius plot, suggests activation of gas phase reactions at elevated temperatures. Importantly, our proposed methods yield insights that align with experimental observations and theoretical principles, aiding decision-making in process design and optimization. By circumventing the need for costly and time-consuming experiments, our approach offers a pragmatic pathway towards enhanced process efficiency. Moreover, this study underscores the potential of data-driven computational methods for innovating reactor design paradigms.
Read more5/30/2024


0
Hybrid Unsupervised Learning Strategy for Monitoring Industrial Batch Processes
Christian W. Frey
Industrial production processes, especially in the pharmaceutical industry, are complex systems that require continuous monitoring to ensure efficiency, product quality, and safety. This paper presents a hybrid unsupervised learning strategy (HULS) for monitoring complex industrial processes. Addressing the limitations of traditional Self-Organizing Maps (SOMs), especially in scenarios with unbalanced data sets and highly correlated process variables, HULS combines existing unsupervised learning techniques to address these challenges. To evaluate the performance of the HULS concept, comparative experiments are performed based on a laboratory batch
Read more4/5/2024


0
Machine learning for structure-guided materials and process design
Lukas Morand, Tarek Iraki, Johannes Dornheim, Stefan Sandfeld, Norbert Link, Dirk Helm
In recent years, there has been a growing interest in accelerated materials innovation in the context of the process-structure-property chain. In this regard, it is essential to take into account manufacturing processes and tailor materials design approaches to support downstream process design approaches. As a major step into this direction, we present a holistic optimization approach that covers the entire process-structure-property chain in materials engineering. Our approach specifically employs machine learning to address two critical identification problems: a materials design problem, which involves identifying near-optimal material structures that exhibit desired properties, and a process design problem that is to find an optimal processing path to manufacture these structures. Both identification problems are typically ill-posed, which presents a significant challenge for solution approaches. However, the non-unique nature of these problems offers an important advantage for processing: By having several target structures that perform similarly well, processes can be efficiently guided towards manufacturing the best reachable structure. The functionality of the approach will be demonstrated manufacturing crystallographic textures with desired properties in a metal forming process.
Read more7/29/2024