Machine Learning-Assisted Discovery of Flow Reactor Designs

0
📊
Sign in to get full access
Overview
- Additive manufacturing has enabled the creation of more complex and advanced reactor geometries.
- Identifying optimal configurations within these high-dimensional design spaces is a significant challenge.
- Existing parameterizations of reactor geometries are low-dimensional, with expensive optimization limiting more complex solutions.
- This paper presents a machine learning-assisted approach to designing the next generation of chemical reactors, using high-dimensional parameterizations, computational fluid dynamics, and multi-fidelity Bayesian optimization.
Plain English Explanation
Additive manufacturing, also known as 3D printing, has made it possible to create chemical reactors with more complex and advanced shapes. However, finding the best design for these reactors within the vast range of possible configurations is a major challenge. Current methods for describing reactor geometry are relatively simple, with expensive optimization processes that limit the ability to explore more complex solutions.
To address this, the researchers in this study developed a new approach that combines machine learning, computational fluid dynamics, and a type of optimization called Bayesian optimization. They focused on a specific type of reactor called a coiled reactor, and looked at how the flow of materials inside the reactor can be improved to enhance mixing and performance.
By using their advanced approach, the researchers were able to identify key characteristics of optimal reactor designs. They then used principles of fluid dynamics to select novel design features that led to a 60% improvement in experimental performance compared to conventional reactor designs. This demonstrates how combining advanced manufacturing techniques with "augmented intelligence" (a term for the integration of human and machine capabilities) can result in better-performing and more sustainable reactor designs.
Technical Explanation
The researchers established a machine learning-assisted approach for designing the next generation of chemical reactors. This involved:
- Using high-dimensional parameterizations to describe the reactor geometry, allowing for more complex design spaces.
- Applying computational fluid dynamics (CFD) simulations to model the fluid flow and performance within the reactor designs.
- Employing multi-fidelity Bayesian optimization to efficiently navigate the high-dimensional design space and identify promising configurations.
The team associated the development of mixing-enhancing vortical flow structures in novel coiled reactor designs with improved performance. By leveraging the principles of fluid dynamics, they were able to rationalize the selection of novel design features that led to a 60% improvement in experimental plug flow performance over conventional reactor designs.
Critical Analysis
The paper demonstrates a promising approach for tackling the challenge of identifying optimal reactor configurations within high-dimensional design spaces enabled by additive manufacturing. However, the study is focused on a specific reactor type (coiled reactors) and its findings may not directly translate to other reactor geometries.
Additionally, the reliance on CFD simulations, while necessary for exploring the design space, introduces potential uncertainties and simplifications that could impact the accuracy of the results. Further experimental validation would be needed to fully assess the performance improvements claimed.
The authors also note that the high-dimensional parameterization used in this study could be computationally intensive, which may limit the scalability of the approach for even more complex reactor designs. Exploring ways to improve the efficiency and scalability of the optimization process would be an important area for future research.
Conclusion
This study presents a novel machine learning-assisted approach for designing the next generation of chemical reactors, leveraging the capabilities of additive manufacturing. By combining high-dimensional parameterizations, computational fluid dynamics, and multi-fidelity Bayesian optimization, the researchers were able to identify key characteristics of optimal reactor designs and achieve significant performance improvements over conventional designs.
The integration of advanced manufacturing techniques with "augmented intelligence" approaches, as demonstrated in this work, holds great promise for driving innovation and sustainability in the field of chemical reactor design. Further research to address the limitations and scale the approach to even more complex geometries could lead to transformative advancements in reactor technology and their environmental impact.
This summary was produced with help from an AI and may contain inaccuracies - check out the links to read the original source documents!
Related Papers
📊

0
Machine Learning-Assisted Discovery of Flow Reactor Designs
Tom Savage, Nausheen Basha, Jonathan McDonough, James Krassowski, Omar K Matar, Ehecatl Antonio del Rio Chanona
Additive manufacturing has enabled the fabrication of advanced reactor geometries, permitting larger, more complex design spaces. Identifying promising configurations within such spaces presents a significant challenge for current approaches. Furthermore, existing parameterisations of reactor geometries are low-dimensional with expensive optimisation limiting more complex solutions. To address this challenge, we establish a machine learning-assisted approach for the design of the next-generation of chemical reactors, combining the application of high-dimensional parameterisations, computational fluid dynamics, and multi-fidelity Bayesian optimisation. We associate the development of mixing-enhancing vortical flow structures in novel coiled reactors with performance, and use our approach to identify key characteristics of optimal designs. By appealing to the principles of flow dynamics, we rationalise the selection of novel design features that lead to experimental plug flow performance improvements of 60% over conventional designs. Our results demonstrate that coupling advanced manufacturing techniques with `augmented-intelligence' approaches can lead to superior design performance and, consequently, emissions-reduction and sustainability.
Read more6/7/2024
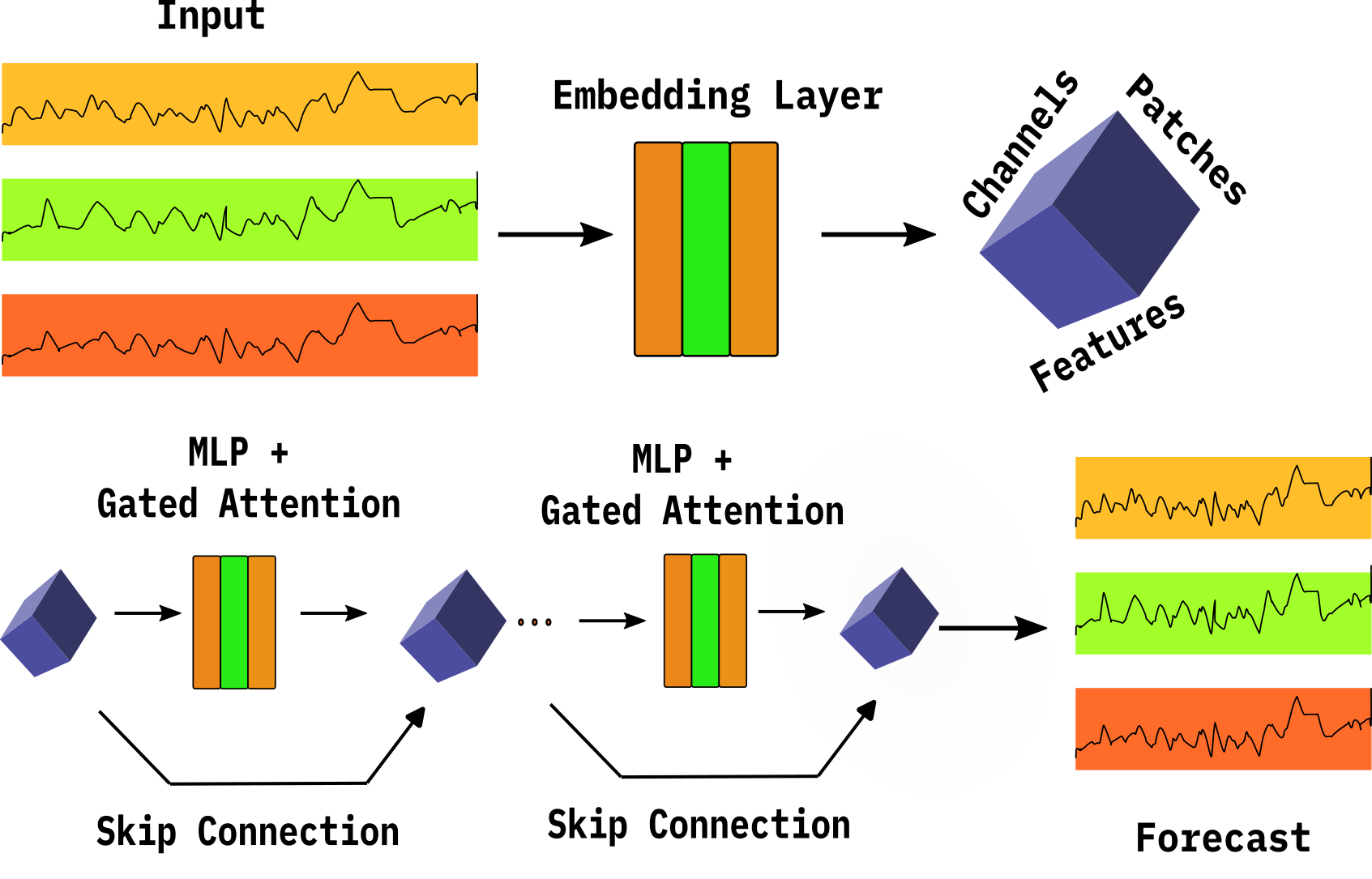

0
Towards Foundation Models for the Industrial Forecasting of Chemical Kinetics
Imran Nasim, Joa~o Lucas de Sousa Almeida
Scientific Machine Learning is transforming traditional engineering industries by enhancing the efficiency of existing technologies and accelerating innovation, particularly in modeling chemical reactions. Despite recent advancements, the issue of solving stiff chemically reacting problems within computational fluid dynamics remains a significant issue. In this study we propose a novel approach utilizing a multi-layer-perceptron mixer architecture (MLP-Mixer) to model the time-series of stiff chemical kinetics. We evaluate this method using the ROBER system, a benchmark model in chemical kinetics, to compare its performance with traditional numerical techniques. This study provides insight into the industrial utility of the recently developed MLP-Mixer architecture to model chemical kinetics and provides motivation for such neural architecture to be used as a base for time-series foundation models.
Read more8/21/2024


0
Machine learning for structure-guided materials and process design
Lukas Morand, Tarek Iraki, Johannes Dornheim, Stefan Sandfeld, Norbert Link, Dirk Helm
In recent years, there has been a growing interest in accelerated materials innovation in the context of the process-structure-property chain. In this regard, it is essential to take into account manufacturing processes and tailor materials design approaches to support downstream process design approaches. As a major step into this direction, we present a holistic optimization approach that covers the entire process-structure-property chain in materials engineering. Our approach specifically employs machine learning to address two critical identification problems: a materials design problem, which involves identifying near-optimal material structures that exhibit desired properties, and a process design problem that is to find an optimal processing path to manufacture these structures. Both identification problems are typically ill-posed, which presents a significant challenge for solution approaches. However, the non-unique nature of these problems offers an important advantage for processing: By having several target structures that perform similarly well, processes can be efficiently guided towards manufacturing the best reachable structure. The functionality of the approach will be demonstrated manufacturing crystallographic textures with desired properties in a metal forming process.
Read more7/29/2024


0
Deep learning modelling of manufacturing and build variations on multi-stage axial compressors aerodynamics
Giuseppe Bruni, Sepehr Maleki, Senthil K. Krishnababu
Applications of deep learning to physical simulations such as Computational Fluid Dynamics have recently experienced a surge in interest, and their viability has been demonstrated in different domains. However, due to the highly complex, turbulent and three-dimensional flows, they have not yet been proven usable for turbomachinery applications. Multi-stage axial compressors for gas turbine applications represent a remarkably challenging case, due to the high-dimensionality of the regression of the flow-field from geometrical and operational variables. This paper demonstrates the development and application of a deep learning framework for predictions of the flow field and aerodynamic performance of multi-stage axial compressors. A physics-based dimensionality reduction unlocks the potential for flow-field predictions, as it re-formulates the regression problem from an un-structured to a structured one, as well as reducing the number of degrees of freedom. Compared to traditional black-box surrogate models, it provides explainability to the predictions of overall performance by identifying the corresponding aerodynamic drivers. This is applied to model the effect of manufacturing and build variations, as the associated performance scatter is known to have a significant impact on $CO_2$ emissions, therefore posing a challenge of great industrial and environmental relevance. The proposed architecture is proven to achieve an accuracy comparable to that of the CFD benchmark, in real-time, for an industrially relevant application. The deployed model, is readily integrated within the manufacturing and build process of gas turbines, thus providing the opportunity to analytically assess the impact on performance with actionable and explainable data.
Read more9/9/2024