Predicting Peak Stresses In Microstructured Materials Using Convolutional Encoder-Decoder Learning

0
🗣️
Sign in to get full access
Overview
- Presents a machine learning approach to predict peak-stress clusters in heterogeneous polycrystalline materials
- Prior work on using machine learning in mechanics has focused on predicting the effective response and overall stress fields, but not peak stresses which are critical for failure
- This work develops a deep-learning based Convolutional Encoder-Decoder method to predict the size and characteristics of peak-stress clusters in the framework of heterogeneous linear elasticity
Plain English Explanation
This research develops a new machine learning model to predict the locations and characteristics of the highest stress points, or "peak stress clusters," within complex, heterogeneous materials like polycrystalline metals. Prior machine learning work in mechanics has been able to predict the overall stress patterns in these materials, but has not been able to accurately capture the small, critical regions of peak stress that can lead to material failure.
The key innovation here is a deep learning model based on convolutional filters that can learn the relationship between a material's microstructure (the arrangement of its internal grains and defects) and the resulting stress fields. The model is first trained on synthetic microstructures and corresponding stress fields calculated using traditional engineering methods. It then uses this training to predict the stress field, including the location and size of peak stress clusters, when given a new microstructure as input.
The researchers show that this model is able to accurately capture the geometric details of the peak stress regions, especially for the highest stress areas that are most critical for failure. This suggests the model could be a powerful tool for designing and optimizing materials to avoid failure-causing defects.
Technical Explanation
The paper presents a Convolutional Encoder-Decoder approach to predict the characteristics of peak-stress clusters in heterogeneous polycrystalline materials. Prior work on using machine learning in the context of mechanics [https://aimodels.fyi/papers/arxiv/introducing-microstructure-embedded-autoencoder-approach-reconstructing-high], [https://aimodels.fyi/papers/arxiv/equivariant-graph-convolutional-neural-networks-representation-homogenized], [https://aimodels.fyi/papers/arxiv/physically-recurrent-neural-network-rate-path-dependent], [https://aimodels.fyi/papers/arxiv/kinematic-analysis-structural-mechanics-based-convolutional-neural] has focused on predicting the effective response and overall structure of stress fields, but not the critical peak stresses.
The proposed method uses convolutional filters to model the local spatial relations between microstructures and stress fields using spatially weighted averaging operations. The model is first trained on synthetically-generated microstructures and corresponding linear elastic stress fields calculated using traditional engineering methods. It then uses this training to predict the stress field, including the location and geometric characteristics of peak-stress clusters, when given a new microstructure as input.
The accuracy of the peak-stress predictions is evaluated using the cosine similarity metric and by comparing the predicted versus ground-truth geometric properties of the peak-stress clusters. The results show the model is able to effectively capture the details of the peak-stress regions, with improved performance for higher (normalized) values of peak stress compared to lower values.
Critical Analysis
The paper makes a valuable contribution by demonstrating the ability of a deep learning model to accurately predict the critical peak-stress clusters in heterogeneous materials, which is a longstanding challenge in computational mechanics. By focusing on these localized high-stress regions rather than just the overall stress field, the model provides insights that are directly relevant to failure prediction and materials design.
However, the training approach relies on synthetically-generated microstructures, which may not fully capture the complexity of real-world materials. Additional validation on experimental microstructure data would help strengthen the conclusions. Additionally, the paper does not explore the model's generalization to different types of materials or loading conditions beyond the linear elastic regime considered here. [https://aimodels.fyi/papers/arxiv/physically-recurrent-neural-network-rate-path-dependent]
Further research is needed to understand the model's limitations, particularly around its ability to handle more complex, nonlinear material behaviors. Comparing the deep learning approach to traditional numerical techniques, in terms of both accuracy and computational efficiency, would also provide valuable insights.
Conclusion
This work presents a promising deep learning approach for predicting the critical peak-stress clusters in heterogeneous polycrystalline materials. By focusing on these localized high-stress regions, the model provides valuable information for failure analysis and materials design that complements prior work on overall stress field prediction.
The demonstrated ability to accurately capture the geometric details of peak-stress clusters, especially for the most severe stress concentrations, suggests this technique could be a powerful tool for designing microstructures that are resistant to failure. Further research to validate the model on experimental data and explore its generalization to more complex material behaviors will be important next steps.
This summary was produced with help from an AI and may contain inaccuracies - check out the links to read the original source documents!
Related Papers
🗣️

0
Predicting Peak Stresses In Microstructured Materials Using Convolutional Encoder-Decoder Learning
Ankit Shrivastava, Jingxiao Liu, Kaushik Dayal, Hae Young Noh
This work presents a machine learning approach to predict peak-stress clusters in heterogeneous polycrystalline materials. Prior work on using machine learning in the context of mechanics has largely focused on predicting the effective response and overall structure of stress fields. However, their ability to predict peak stresses -- which are of critical importance to failure -- is unexplored, because the peak-stress clusters occupy a small spatial volume relative to the entire domain, and hence requires computationally expensive training. This work develops a deep-learning based Convolutional Encoder-Decoder method that focuses on predicting peak-stress clusters, specifically on the size and other characteristics of the clusters in the framework of heterogeneous linear elasticity. This method is based on convolutional filters that model local spatial relations between microstructures and stress fields using spatially weighted averaging operations. The model is first trained against linear elastic calculations of stress under applied macroscopic strain in synthetically-generated microstructures, which serves as the ground truth. The trained model is then applied to predict the stress field given a (synthetically-generated) microstructure and then to detect peak-stress clusters within the predicted stress field. The accuracy of the peak-stress predictions is analyzed using the cosine similarity metric and by comparing the geometric characteristics of the peak-stress clusters against the ground-truth calculations. It is observed that the model is able to learn and predict the geometric details of the peak-stress clusters and, in particular, performed better for higher (normalized) values of the peak stress as compared to lower values of the peak stress. These comparisons showed that the proposed method is well-suited to predict the characteristics of peak-stress clusters.
Read more5/10/2024
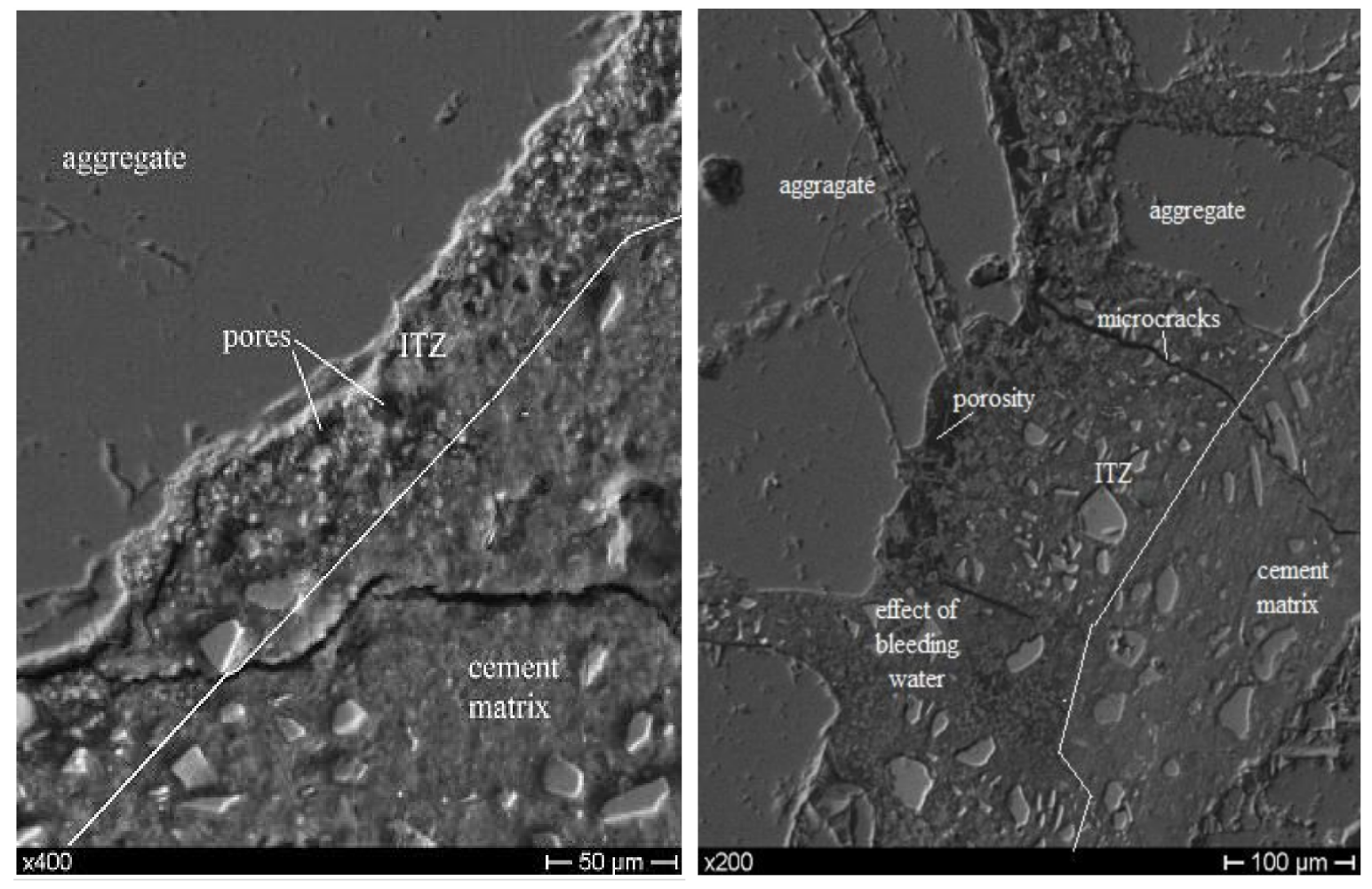

0
A spatiotemporal deep learning framework for prediction of crack dynamics in heterogeneous solids: efficient mapping of concrete microstructures to its fracture properties
Rasoul Najafi Koopas, Shahed Rezaei, Natalie Rauter, Richard Ostwald, Rolf Lammering
A spatiotemporal deep learning framework is proposed that is capable of 2D full-field prediction of fracture in concrete mesostructures. This framework not only predicts fractures but also captures the entire history of the fracture process, from the crack initiation in the interfacial transition zone to the subsequent propagation of the cracks in the mortar matrix. In addition, a convolutional neural network is developed which can predict the averaged stress-strain curve of the mesostructures. The UNet modeling framework, which comprises an encoder-decoder section with skip connections, is used as the deep learning surrogate model. Training and test data are generated from high-fidelity fracture simulations of randomly generated concrete mesostructures. These mesostructures include geometric variabilities such as different aggregate particle geometrical features, spatial distribution, and the total volume fraction of aggregates. The fracture simulations are carried out in Abaqus, utilizing the cohesive phase-field fracture modeling technique as the fracture modeling approach. In this work, to reduce the number of training datasets, the spatial distribution of three sets of material properties for three-phase concrete mesostructures, along with the spatial phase-field damage index, are fed to the UNet to predict the corresponding stress and spatial damage index at the subsequent step. It is shown that after the training process using this methodology, the UNet model is capable of accurately predicting damage on the unseen test dataset by using 470 datasets. Moreover, another novel aspect of this work is the conversion of irregular finite element data into regular grids using a developed pipeline. This approach allows for the implementation of less complex UNet architecture and facilitates the integration of phase-field fracture equations into surrogate models for future developments.
Read more7/25/2024
🧠

0
A Neural Network Transformer Model for Composite Microstructure Homogenization
Emil Pitz, Kishore Pochiraju
Heterogeneity and uncertainty in a composite microstructure lead to either computational bottlenecks if modeled rigorously or to solution inaccuracies in the stress field and failure predictions if approximated. Although methods suitable for analyzing arbitrary and non-linear microstructures exist, their computational cost makes them impractical to use in large-scale structural analysis. Surrogate models or Reduced Order Models (ROMs) commonly enhance efficiencies but are typically calibrated with a single microstructure. Homogenization methods, such as the Mori-Tanaka method, offer rapid homogenization for a wide range of constituent properties. However, simplifying assumptions, like stress and strain averaging in phases, render the consideration of both deterministic and stochastic variations in microstructure infeasible. This paper illustrates a transformer neural network architecture that captures the knowledge of various microstructures and constituents, enabling it to function as a computationally efficient homogenization surrogate model. Given an image or an abstraction of an arbitrary composite microstructure of linearly elastic fibers in an elastoplastic matrix, the transformer network predicts the history-dependent, non-linear, and homogenized stress-strain response. Two methods for encoding microstructure features were tested: calculating two-point statistics using Principal Component Analysis (PCA) for dimensionality reduction and employing an autoencoder with a Convolutional Neural Network (CNN). Both methods accurately predict the homogenized material response. The developed transformer neural network offers an efficient means for microstructure-to-property translation, generalizable and extendable to a variety of microstructures. The paper describes the network architecture, training and testing data generation, and performance under cycling and random loadings.
Read more5/30/2024
👨🏫

0
A finite operator learning technique for mapping the elastic properties of microstructures to their mechanical deformations
Shahed Rezaei, Reza Najian Asl, Shirko Faroughi, Mahdi Asgharzadeh, Ali Harandi, Rasoul Najafi Koopas, Gottfried Laschet, Stefanie Reese, Markus Apel
To obtain fast solutions for governing physical equations in solid mechanics, we introduce a method that integrates the core ideas of the finite element method with physics-informed neural networks and concept of neural operators. This approach generalizes and enhances each method, learning the parametric solution for mechanical problems without relying on data from other resources (e.g. other numerical solvers). We propose directly utilizing the available discretized weak form in finite element packages to construct the loss functions algebraically, thereby demonstrating the ability to find solutions even in the presence of sharp discontinuities. Our focus is on micromechanics as an example, where knowledge of deformation and stress fields for a given heterogeneous microstructure is crucial for further design applications. The primary parameter under investigation is the Young's modulus distribution within the heterogeneous solid system. Our investigations reveal that physics-based training yields higher accuracy compared to purely data-driven approaches for unseen microstructures. Additionally, we offer two methods to directly improve the process of obtaining high-resolution solutions, avoiding the need to use basic interpolation techniques. First is based on an autoencoder approach to enhance the efficiency for calculation on high resolution grid point. Next, Fourier-based parametrization is utilized to address complex 2D and 3D problems in micromechanics. The latter idea aims to represent complex microstructures efficiently using Fourier coefficients. Comparisons with other well-known operator learning algorithms, further emphasize the advantages of the newly proposed method.
Read more6/4/2024