Technical Report of Mobile Manipulator Robot for Industrial Environments

0
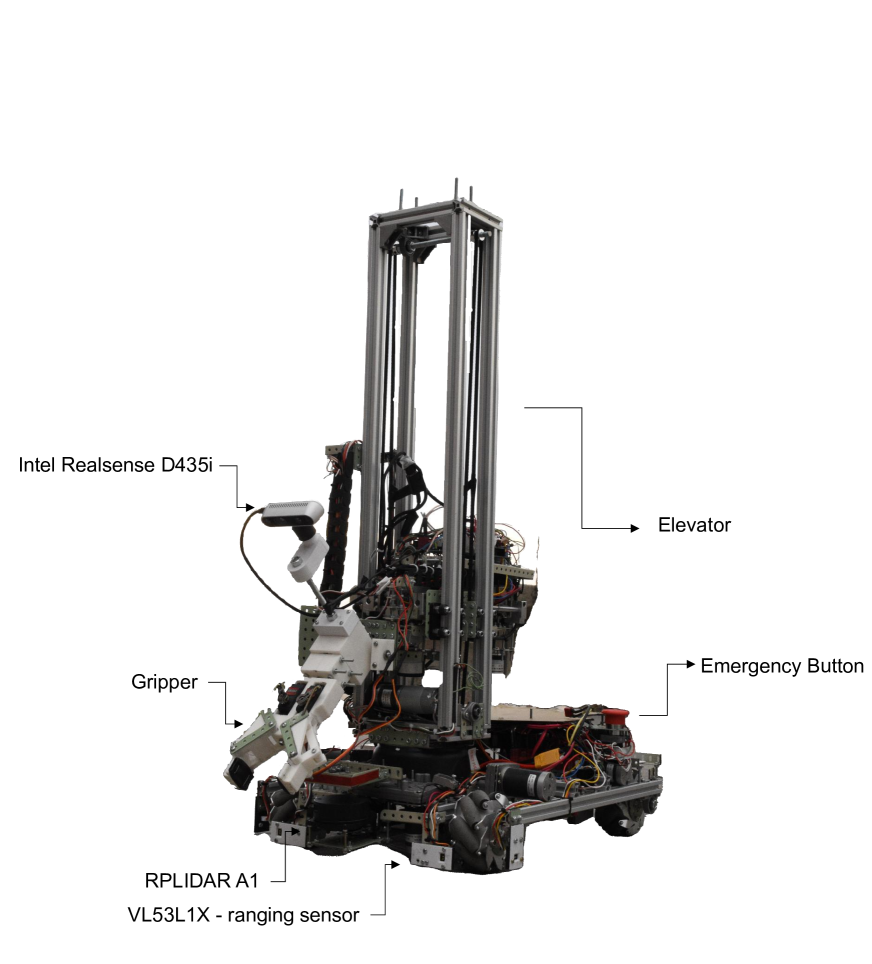
Sign in to get full access
Overview
- Concise bullet points summarizing the key points of the paper
- Introduces the mobile manipulator robot for industrial environments
- Describes the hardware and software components
- Discusses the robot's capabilities and potential applications
Plain English Explanation
The paper presents a technical report on a mobile manipulator robot designed for industrial environments. This robot is equipped with a robotic arm and mobile base, allowing it to navigate factory floors and interact with objects.
The hardware description covers the robot's modular design, including the mobile base, robotic arm, and various sensors. The mobile base provides the robot with mobility, while the robotic arm enables precise grasping and manipulation of objects. Sensors such as cameras and laser scanners allow the robot to perceive its surroundings and plan its actions accordingly.
The technical explanation delves into the specifics of the robot's architecture and capabilities. It describes the control system that coordinates the movement of the mobile base and robotic arm, as well as the computer vision algorithms used for object detection and recognition. The paper also outlines the robot's task-planning and navigation capabilities, which allow it to autonomously navigate the factory environment and complete assigned tasks.
Technical Explanation
The paper presents a detailed technical report on the design and implementation of a mobile manipulator robot for industrial environments. The robot is composed of a mobile base and a robotic arm, allowing it to navigate the factory floor and interact with objects.
The hardware description covers the modular design of the robot, including the mobile base, robotic arm, and various sensors. The mobile base is equipped with omnidirectional wheels, enabling the robot to move in any direction with high maneuverability. The robotic arm, which is mounted on the mobile base, has multiple degrees of freedom and can be used for precise grasping and manipulation of objects. The robot is also equipped with cameras, laser scanners, and other sensors to perceive its surroundings and plan its actions accordingly.
The technical explanation delves into the details of the robot's architecture and capabilities. It describes the control system that coordinates the movement of the mobile base and robotic arm, as well as the computer vision algorithms used for object detection and recognition. The paper also outlines the robot's task-planning and navigation capabilities, which enable it to autonomously navigate the factory environment and complete assigned tasks, such as object manipulation and transportation.
Critical Analysis
The paper provides a comprehensive technical overview of the mobile manipulator robot, but it also acknowledges some potential limitations and areas for further research.
One limitation mentioned is the reliability of the robot's perception and navigation systems in complex, dynamic industrial environments. The authors suggest that further research is needed to improve the robot's ability to handle unexpected obstacles and changes in its surroundings.
Additionally, the paper does not provide a detailed evaluation of the robot's performance in real-world industrial settings. While the authors describe the robot's capabilities, more empirical data on its effectiveness and efficiency in typical industrial tasks would be valuable for assessing its practical viability.
Conclusion
The technical report presents a comprehensive description of a mobile manipulator robot designed for industrial environments. The robot's modular hardware design, including a mobile base and robotic arm, allows it to navigate factory floors and interact with objects. The paper outlines the robot's control systems, computer vision algorithms, and task-planning capabilities, demonstrating its potential to autonomously complete a variety of industrial tasks.
While the paper provides a detailed technical explanation, it also acknowledges areas for further research, such as improving the robot's perception and navigation in dynamic environments. Additional empirical evaluation of the robot's performance in real-world industrial settings would also help to validate its practical applications and identify any remaining challenges.
Overall, this mobile manipulator robot represents an important step forward in the development of autonomous systems for industrial environments, with the potential to enhance productivity, efficiency, and safety in manufacturing and logistics operations.
This summary was produced with help from an AI and may contain inaccuracies - check out the links to read the original source documents!
Related Papers
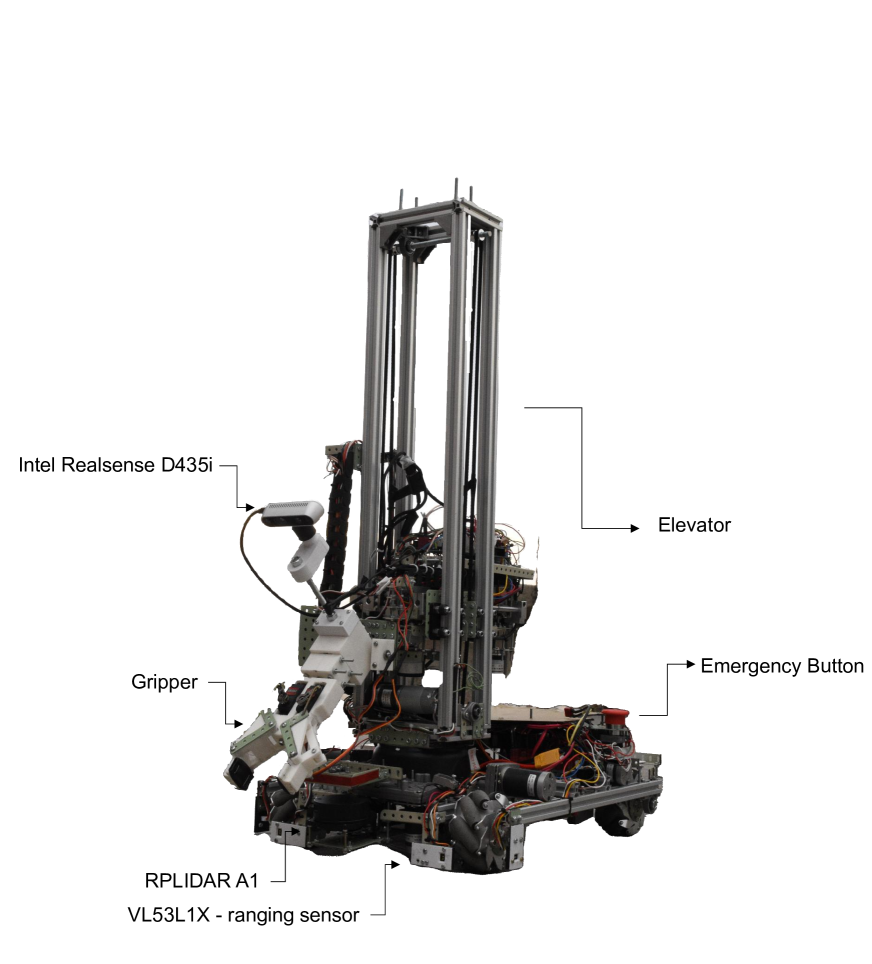

0
Technical Report of Mobile Manipulator Robot for Industrial Environments
Erfan Amoozad Khalili, Kiarash Ghasemzadeh, Hossein Gohari, Mohammadreza Jafari, Matin Jamshidi, Mahdi Khaksar, AmirReza AkramiFard, Mana Hatamzadeh, Saba Sadeghi, Mohammad Hossein Moaiyeri
This paper presents the development of the Auriga @Work robot, designed by the Robotics and Intelligent Automation Lab at Shahid Beheshti University, Department of Electrical Engineering, for the RoboCup 2024 competition. The robot is tailored for industrial applications, focusing on enhancing efficiency in repetitive or hazardous environments. It is equipped with a 4-wheel Mecanum drive system for omnidirectional mobility and a 5-degree-of-freedom manipulator arm with a custom 3D-printed gripper for object manipulation and navigation tasks. The robot's electronics are powered by custom-designed boards utilizing ESP32 microcontrollers and an Nvidia Jetson Nano for real-time control and decision-making. The key software stack integrates Hector SLAM for mapping, the A* algorithm for path planning, and YOLO for object detection, along with advanced sensor fusion for improved navigation and collision avoidance.
Read more9/11/2024
🧪

0
A quantitative investigation for deployment of mobile collaborative robots in high-value manufacturing
Amine Hifi, W. Jackson, C. Loukas, M. Shields, A. Poole, E. Mohseni, C. N. MacLeod, G. Dobie, S. G. Pierce, T. O'Hare, G. Munro, J. O'Brian-O'Reilly, R. W. K. Vithanage
Component inspection is often the bottleneck in high-value manufacturing, driving industries like aerospace toward automated inspection technologies. Current systems often employ fixed arm robots, but they lack the flexibility in adapting to new components or orientations Advanced mobile robotic platforms with updated sensor technologies and algorithms have improved localization and path planning capabilities, making them ideal for bringing inspection processes directly to parts. However, mobile platforms introduce challenges in localization and maneuverability, leading to potential errors. Their positional uncertainty is higher than fixed systems due to the lack of a fixed calibrated location, posing challenges for position-sensitive inspection sensors. Therefore, it's essential to assess the positional accuracy and repeatability of mobile manipulator platforms. The KUKA KMR iiwa was chosen for its collaborative features, robust build, and scalability within the KUKA product range. The accuracy and repeatability of the mobile platform were evaluated through a series of tests to evaluate the performance of its integrated feature mapping, the effect of various speeds on positional accuracy, and the efficiency of the omnidirectional wheels for a range of translation orientations. Experimental evaluation revealed that enabling feature mapping substantially improves the KUKA KMR iiwa's performance, with accuracy gains and error reductions exceeding 90%. Repeatability errors were under 7 mm with mapping activated and around 2.5 mm in practical scenarios, demonstrating that mobile manipulators, incorporating both the manipulator and platform, can fulfil the precise requirements of industries with high precision needs. Providing a highly diverse alternative to traditional fixed-base industrial manipulators.
Read more6/11/2024


0
Integrated Hardware and Software Architecture for Industrial AGV with Manual Override Capability
Pietro Iob, Mauro Schiavo, Angelo Cenedese
This paper presents a study on transforming a traditional human-operated vehicle into a fully autonomous device. By leveraging previous research and state-of-the-art technologies, the study addresses autonomy, safety, and operational efficiency in industrial environments. Motivated by the demand for automation in hazardous and complex industries, the autonomous system integrates sensors, actuators, advanced control algorithms, and communication systems to enhance safety, streamline processes, and improve productivity. The paper covers system requirements, hardware architecture, software framework and preliminary results. This research offers insights into designing and implementing autonomous capabilities in human-operated vehicles, with implications for improving safety and efficiency in various industrial sectors.
Read more8/23/2024


0
UruBots Autonomous Cars Team One Description Paper for FIRA 2024
Pablo Moraes, Christopher Peters, Any Da Rosa, Vinicio Melgar, Franco Nu~nez, Maximo Retamar, William Moraes, Victoria Saravia, Hiago Sodre, Sebastian Barcelona, Anthony Scirgalea, Juan Deniz, Bruna Guterres, Andr'e Kelbouscas, Ricardo Grando
This document presents the design of an autonomous car developed by the UruBots team for the 2024 FIRA Autonomous Cars Race Challenge. The project involves creating an RC-car sized electric vehicle capable of navigating race tracks with in an autonomous manner. It integrates mechanical and electronic systems alongside artificial intelligence based algorithms for the navigation and real-time decision-making. The core of our project include the utilization of an AI-based algorithm to learn information from a camera and act in the robot to perform the navigation. We show that by creating a dataset with more than five thousand samples and a five-layered CNN we managed to achieve promissing performance we our proposed hardware setup. Overall, this paper aims to demonstrate the autonomous capabilities of our car, highlighting its readiness for the 2024 FIRA challenge, helping to contribute to the field of autonomous vehicle research.
Read more6/14/2024