Cyclic Fusion of Measuring Information in Curved Elastomer Contact via Vision-Based Tactile Sensing

0
š²
Sign in to get full access
Overview
- Elastomer deformation can be used for effective tactile sensing by capturing microscale deformations through optical imaging sensors.
- Curved elastomer surfaces are designed to adjust to changes in contact area, but this leads to uneven deformations, distorting tactile images and reducing the utility of the data.
- This work proposes a cyclic fusion strategy to extract precise contact data and integrate shape features at the pixel level, enhancing information content and preserving structural consistency.
Plain English Explanation
Tactile sensing, or the ability to feel and detect physical contact, is an important capability for robots and other autonomous systems. One approach to tactile sensing is to use elastomers, which are stretchy, rubber-like materials. When an elastomer touches an object, it deforms or changes shape slightly, and these deformations can be detected by optical imaging sensors.
However, a challenge with this approach is that the elastomer's curved surface can lead to uneven deformations, distorting the tactile images and making it hard to accurately measure the object's features. To address this, the researchers propose a cyclic fusion strategy that combines information from the deformed elastomer surface to create a more accurate representation of the object's shape and texture.
By using frequency domain fusion, the system is able to extract detailed micro-scale contact features and enhance the information content by over 40%, while preserving the structural consistency of the tactile data. This allows the system to more effectively detect and classify the object's surface features, achieving a detection accuracy of over 90% and a classification accuracy of almost 100%.
By minimizing data interference and accurately depicting the object's shape and texture, this tactile sensing approach can enhance the ability of robots and other systems to perceive and interact with their environment in a more natural and intuitive way.
Technical Explanation
The key elements of this research are:
-
Elastomer Deformation for Tactile Sensing: The researchers leverage the ability of elastomers to deform when in contact with objects, and use optical imaging sensors to detect these microscale deformations. This allows for effective tactile sensing, as the deformations capture detailed information about the object's surface features.
-
Curved Elastomer Surfaces: To enable continuous contact recognition, the researchers design the elastomer surfaces to be curved, which helps the material conform to changes in the contact area. However, this curved design leads to uneven deformations, distorting the tactile images and reducing the accuracy of the data.
-
Cyclic Fusion Strategy: To address the distortion issue, the researchers propose a cyclic fusion strategy that combines information from the deformed elastomer surface in the frequency domain. This enhances the information content by over 40% and preserves the structural consistency of the tactile data.
-
Micro-scale Feature Extraction and Classification: By effectively extracting and summarizing the micro-scale contact features using neural networks, the system is able to achieve a detection mean average precision (mAP) of 90.90% and a classification accuracy of 99.83%. This demonstrates the system's ability to accurately perceive and characterize the object's surface morphology.
-
Minimizing Data Interference: The cyclic fusion strategy minimizes data interference, allowing the tactile images to more accurately depict the object's shape and texture. This enhances the system's ability to restore the tactile sensation and perception of the object's physical properties.
Critical Analysis
The researchers have presented a compelling approach to addressing the challenges of using elastomer deformation for tactile sensing. By proposing the cyclic fusion strategy, they have demonstrated a way to mitigate the distortion issues caused by the curved elastomer surfaces, leading to more accurate and consistent tactile data.
One potential area for further exploration is the robustness of this approach to different types of objects and surface features. The researchers mention that the system was effective in extracting micro-scale contact features, but it would be valuable to understand how it performs with a wider range of object shapes, textures, and materials.
Additionally, while the system achieves impressive detection and classification accuracy, it would be beneficial to understand the computational and memory requirements of the proposed approach, as well as its scalability to larger-scale tactile sensing applications. Exploring the trade-offs between performance and resource usage could help inform the practical implementation of this technology in real-world robotic systems.
Overall, this research represents an important step forward in the field of tactile sensing, and the proposed cyclic fusion strategy offers a promising solution for enhancing the utility and accuracy of elastomer-based tactile data.
Conclusion
This work presents a novel approach to tackling the challenges of using elastomer deformation for effective tactile sensing. By proposing a cyclic fusion strategy that combines information from the deformed elastomer surface in the frequency domain, the researchers have demonstrated a way to enhance the information content and preserve the structural consistency of the tactile data.
The ability to accurately extract and characterize micro-scale contact features, achieving high detection and classification accuracy, highlights the potential of this approach to improve the perception and interaction capabilities of robotic systems. By minimizing data interference and more accurately depicting object morphology, this tactile sensing strategy can contribute to the development of more intuitive and natural human-robot interfaces, as well as enhance the overall dexterity and manipulation skills of autonomous systems.
Further research into the robustness and scalability of this approach, as well as exploring the trade-offs between performance and resource usage, could help to unlock the full potential of this tactile sensing technology and pave the way for its broader adoption in real-world applications.
This summary was produced with help from an AI and may contain inaccuracies - check out the links to read the original source documents!
Related Papers
š²

0
Cyclic Fusion of Measuring Information in Curved Elastomer Contact via Vision-Based Tactile Sensing
Zilan Li, Zhibin Zou, Weiliang Xu, Yuanzhi Zhou, Guoyuan Zhou, Muxing Huang, Xuan Huang, Xinming Li
Using elastomer deformation to measure object surface features in tactile sensing is effective, as it captures microscale deformations through densely arranged optical imaging sensors that detect subtle data variations. To enable continuous contact recognition, elastomers are crafted with curved surfaces to adjust to changes in the contact area. However, this design leads to uneven deformations, distorting tactile images and inaccurately reflecting the true elastomer deformations. This inconsistency considerably reduces the utility of the tactile data. In this work, we propose a cyclic fusion strategy for vision-based tactile sensing for precise contact data extraction and shape feature integration at the pixel level. Utilizing frequency domain fusion, the system merges topography as indicated by elastomer deformation, enhancing information content by over 40% and preserving structural consistency. Further, this system could effectively extract and summarize micro-scale contact features, using neural networks to achieve a detection mAP of 90.90% and classification accuracy of 99.83%. Using this strategy, the measurement minimizes data interference, accurately depicting object morphology on tactile images and enhancing tactile sensation restoration.
Read more7/23/2024
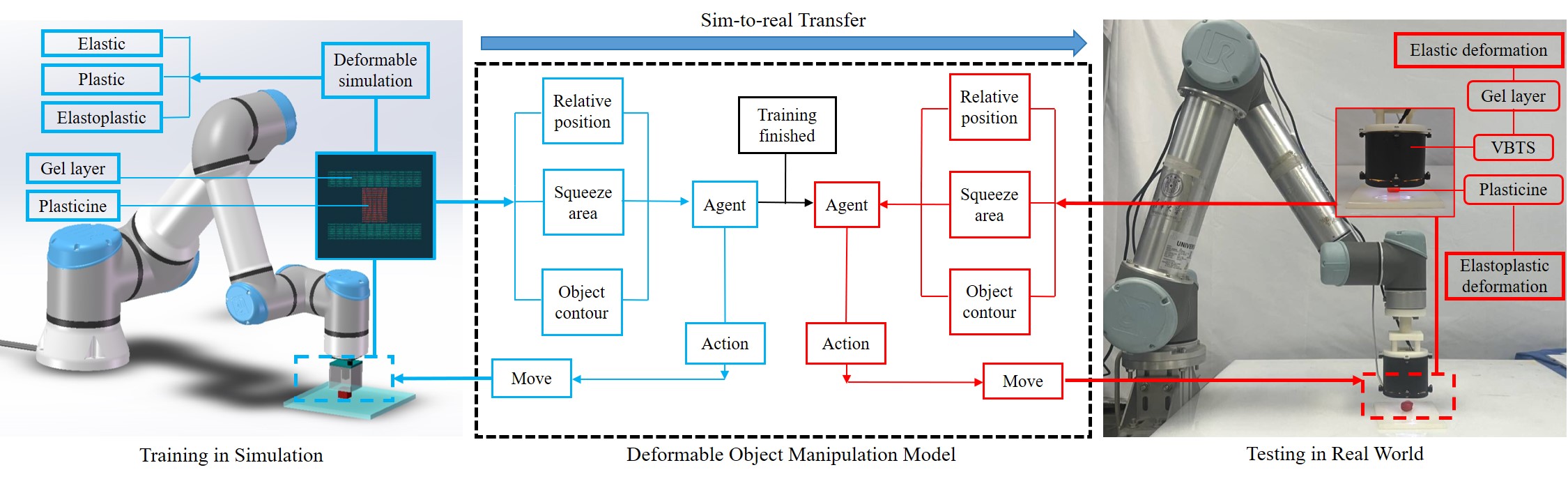

0
Soft Contact Simulation and Manipulation Learning of Deformable Objects with Vision-based Tactile Sensor
Jianhua Shan, Yuhao Sun, Shixin Zhang, Fuchun Sun, Zixi Chen, Zirong Shen, Cesare Stefanini, Yiyong Yang, Shan Luo, Bin Fang
Deformable object manipulation is a classical and challenging research area in robotics. Compared with rigid object manipulation, this problem is more complex due to the deformation properties including elastic, plastic, and elastoplastic deformation. In this paper, we describe a new deformable object manipulation method including soft contact simulation, manipulation learning, and sim-to-real transfer. We propose a novel approach utilizing Vision-Based Tactile Sensors (VBTSs) as the end-effector in simulation to produce observations like relative position, squeezed area, and object contour, which are transferable to real robots. For a more realistic contact simulation, a new simulation environment including elastic, plastic, and elastoplastic deformations is created. We utilize RL strategies to train agents in the simulation, and expert demonstrations are applied for challenging tasks. Finally, we build a real experimental platform to complete the sim-to-real transfer and achieve a 90% success rate on difficult tasks such as cylinder and sphere. To test the robustness of our method, we use plasticine of different hardness and sizes to repeat the tasks including cylinder and sphere. The experimental results show superior performances of deformable object manipulation with the proposed method.
Read more5/14/2024
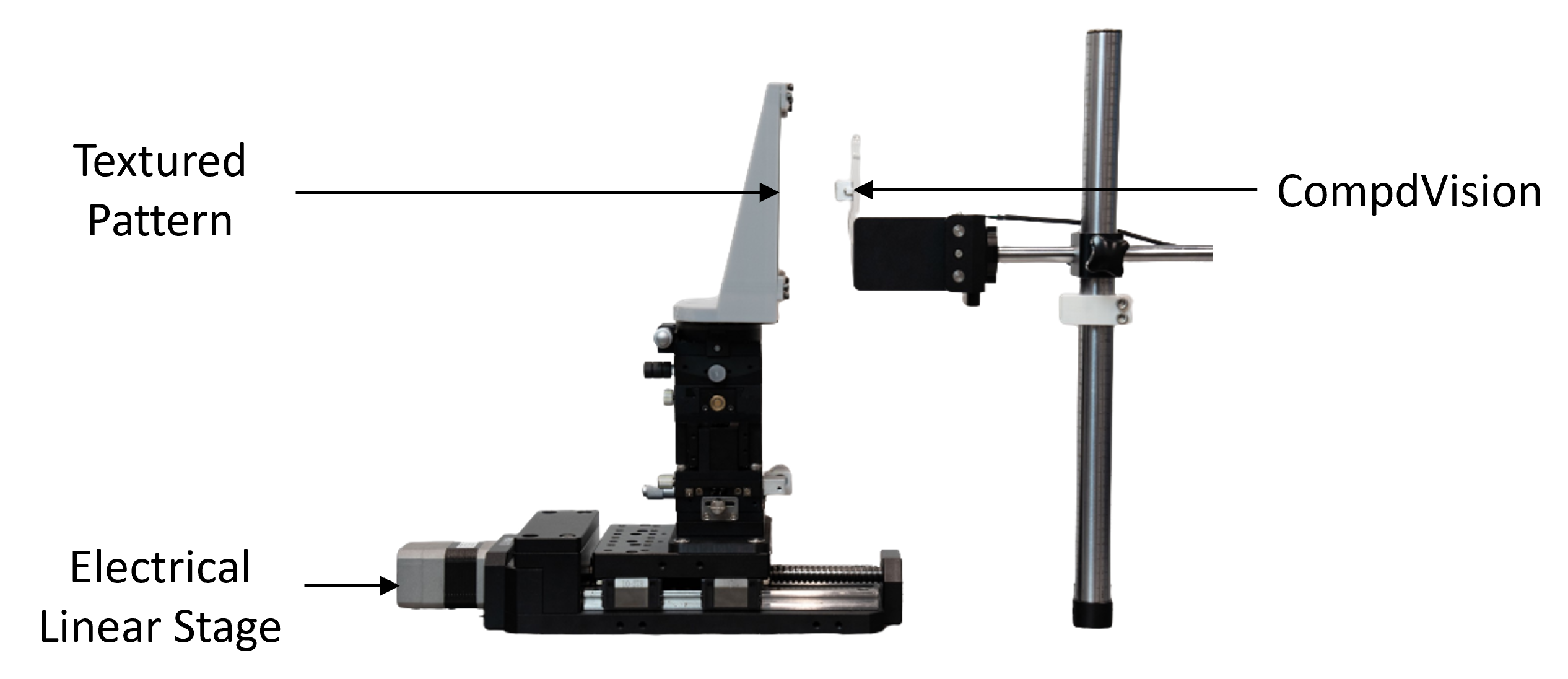

0
CompdVision: Combining Near-Field 3D Visual and Tactile Sensing Using a Compact Compound-Eye Imaging System
Lifan Luo, Boyang Zhang, Zhijie Peng, Yik Kin Cheung, Guanlan Zhang, Zhigang Li, Michael Yu Wang, Hongyu Yu
As automation technologies advance, the need for compact and multi-modal sensors in robotic applications is growing. To address this demand, we introduce CompdVision, a novel sensor that employs a compound-eye imaging system to combine near-field 3D visual and tactile sensing within a compact form factor. CompdVision utilizes two types of vision units to address diverse sensing needs, eliminating the need for complex modality conversion. Stereo units with far-focus lenses can see through the transparent elastomer for depth estimation beyond the contact surface. Simultaneously, tactile units with near-focus lenses track the movement of markers embedded in the elastomer to obtain contact deformation. Experimental results validate the sensor's superior performance in 3D visual and tactile sensing, proving its capability for reliable external object depth estimation and precise measurement of tangential and normal contact forces. The dual modalities and compact design make the sensor a versatile tool for robotic manipulation.
Read more7/19/2024


0
Visuo-Tactile Exploration of Unknown Rigid 3D Curvatures by Vision-Augmented Unified Force-Impedance Control
Kubra Karacan, Anran Zhang, Hamid Sadeghian, Fan Wu, Sami Haddadin
Despite recent advancements in torque-controlled tactile robots, integrating them into manufacturing settings remains challenging, particularly in complex environments. Simplifying robotic skill programming for non-experts is crucial for increasing robot deployment in manufacturing. This work proposes an innovative approach, Vision-Augmented Unified Force-Impedance Control (VA-UFIC), aimed at intuitive visuo-tactile exploration of unknown 3D curvatures. VA-UFIC stands out by seamlessly integrating vision and tactile data, enabling the exploration of diverse contact shapes in three dimensions, including point contacts, flat contacts with concave and convex curvatures, and scenarios involving contact loss. A pivotal component of our method is a robust online contact alignment monitoring system that considers tactile error, local surface curvature, and orientation, facilitating adaptive adjustments of robot stiffness and force regulation during exploration. We introduce virtual energy tanks within the control framework to ensure safety and stability, effectively addressing inherent safety concerns in visuo-tactile exploration. Evaluation using a Franka Emika research robot demonstrates the efficacy of VA-UFIC in exploring unknown 3D curvatures while adhering to arbitrarily defined force-motion policies. By seamlessly integrating vision and tactile sensing, VA-UFIC offers a promising avenue for intuitive exploration of complex environments, with potential applications spanning manufacturing, inspection, and beyond.
Read more8/27/2024