Root Cause Analysis Of Productivity Losses In Manufacturing Systems Utilizing Ensemble Machine Learning

0
🏅
Sign in to get full access
Overview
- This study introduces a data-driven ensemble approach to analyze productivity losses in automation and manufacturing systems.
- The approach uses cyclic multivariate time series data from binary sensors and signals from Programmable Logic Controllers (PLCs) to automatically identify the root causes of productivity losses.
- The ensemble method integrates various techniques, including information theory and machine learning behavior models, to provide a robust analysis for each production cycle.
- The approach is designed for stream processing to enable quick resolution of productivity issues and can also be used for batch processing.
Plain English Explanation
The paper presents a new way to automatically identify the causes of productivity problems in automated manufacturing systems. These systems often have sensors and controllers that generate lots of data, but it can be challenging to use this data to figure out why productivity is lower than expected.
The researchers developed an "ensemble approach" that combines several different analysis techniques. This helps provide a more reliable and comprehensive understanding of what's causing the productivity issues. The approach can quickly analyze the data as it's being generated, rather than requiring extensive historical data analysis.
By quickly pinpointing the root causes of productivity losses, the manufacturers can take action to resolve the problems and get production back on track faster. The ensemble nature of the approach also means they don't have to rely as heavily on expert human judgement, which can be subjective and time-consuming.
The researchers tested their method on three different types of manufacturing systems - a welding line, an injection molding system, and some simulated PLC data. The results showed the approach was effective at identifying the key factors impacting productivity in each case.
Technical Explanation
The core of the researchers' approach is an "ensemble method" that integrates several different analytical techniques. This includes using "information theory" to understand relationships in the sensor and PLC data, as well as applying "machine learning behavior models" to identify patterns indicative of productivity losses.
By combining these methods, the approach can provide a more robust and comprehensive analysis of what's causing productivity issues in each production cycle. The researchers designed it for "stream processing" so the analysis can happen in real-time, without requiring extensive historical data.
To validate the method, the researchers tested it on three different manufacturing systems:
- A semi-automated welding line
- An injection molding automation system
- A synthetically generated PLC dataset
The results demonstrated the approach's ability to provide "data-driven" insights into the process behavior and identify the root causes of productivity losses in each case.
Critical Analysis
The paper provides a thorough technical explanation of the ensemble approach and its implementation, which seems well-designed to address the challenges of quickly identifying productivity issues in complex manufacturing systems.
One potential limitation is that the method relies on having the right sensor and PLC data available. In some cases, manufacturers may not have that level of instrumentation or historical data to train the models. Further research could explore how the approach might be adapted for systems with more limited data sources.
Additionally, while the ensemble nature of the method is meant to provide more reliable results than individual analysis techniques, there could still be cases where the underlying models make incorrect inferences. Ongoing monitoring and validation of the approach's performance would be important, especially as it gets applied to new manufacturing contexts.
Overall, the researchers present a promising data-driven solution to a significant challenge in modern manufacturing. With further development and real-world testing, this type of ensemble analytics approach could become an important tool for improving productivity and efficiency.
Conclusion
This study introduces a novel data-driven ensemble method for automatically analyzing productivity losses in automated manufacturing systems. By integrating multiple analytical techniques, the approach can quickly identify the root causes of productivity issues based on sensor and PLC data, without relying heavily on human expert judgment.
The validation across three different manufacturing use cases demonstrates the versatility and effectiveness of the method. While there are some potential limitations around data requirements and model reliability, the researchers have made an important contribution towards enabling more autonomous, data-driven optimization of complex production processes.
As automation continues to transform modern industry, tools like this ensemble analysis approach will become increasingly valuable for manufacturers seeking to maximize the efficiency and productivity of their systems.
This summary was produced with help from an AI and may contain inaccuracies - check out the links to read the original source documents!
Related Papers
🏅

0
Root Cause Analysis Of Productivity Losses In Manufacturing Systems Utilizing Ensemble Machine Learning
Jonas Gram, Brandon K. Sai, Thomas Bauernhansl
In today's rapidly evolving landscape of automation and manufacturing systems, the efficient resolution of productivity losses is paramount. This study introduces a data-driven ensemble approach, utilizing the cyclic multivariate time series data from binary sensors and signals from Programmable Logic Controllers (PLCs) within these systems. The objective is to automatically analyze productivity losses per cycle and pinpoint their root causes by assigning the loss to a system element. The ensemble approach introduced in this publication integrates various methods, including information theory and machine learning behavior models, to provide a robust analysis for each production cycle. To expedite the resolution of productivity losses and ensure short response times, stream processing becomes a necessity. Addressing this, the approach is implemented as data-stream analysis and can be transferred to batch processing, seamlessly integrating into existing systems without the need for extensive historical data analysis. This method has two positive effects. Firstly, the result of the analysis ensures that the period of lower productivity is reduced by identifying the likely root cause of the productivity loss. Secondly, these results are more reliable due to the ensemble approach and therefore avoid dependency on technical experts. The approach is validated using a semi-automated welding manufacturing system, an injection molding automation system, and a synthetically generated test PLC dataset. The results demonstrate the method's efficacy in offering a data-driven understanding of process behavior and mark an advancement in autonomous manufacturing system analysis.
Read more8/1/2024


0
Ensemble Method for System Failure Detection Using Large-Scale Telemetry Data
Priyanka Mudgal, Rita H. Wouhaybi
The growing reliance on computer systems, particularly personal computers (PCs), necessitates heightened reliability to uphold user satisfaction. This research paper presents an in-depth analysis of extensive system telemetry data, proposing an ensemble methodology for detecting system failures. Our approach entails scrutinizing various parameters of system metrics, encompassing CPU utilization, memory utilization, disk activity, CPU temperature, and pertinent system metadata such as system age, usage patterns, core count, and processor type. The proposed ensemble technique integrates a diverse set of algorithms, including Long Short-Term Memory (LSTM) networks, isolation forests, one-class support vector machines (OCSVM), and local outlier factors (LOF), to effectively discern system failures. Specifically, the LSTM network with other machine learning techniques is trained on Intel Computing Improvement Program (ICIP) telemetry software data to distinguish between normal and failed system patterns. Experimental evaluations demonstrate the remarkable efficacy of our models, achieving a notable detection rate in identifying system failures. Our research contributes to advancing the field of system reliability and offers practical insights for enhancing user experience in computing environments.
Read more7/2/2024
⚙️

0
Machine Learning in High Volume Media Manufacturing
Siddarth Reddy Karuka, Abhinav Sunderrajan, Zheng Zheng, Yong Woon Tiean, Ganesh Nagappan, Allan Luk
Errors or failures in a high-volume manufacturing environment can have significant impact that can result in both the loss of time and money. Identifying such failures early has been a top priority for manufacturing industries and various rule-based algorithms have been developed over the years. However, catching these failures is time consuming and such algorithms cannot adapt well to changes in designs, and sometimes variations in everyday behavior. More importantly, the number of units to monitor in a high-volume manufacturing environment is too big for manual monitoring or for a simple program. Here we develop a novel program that combines both rule-based decisions and machine learning models that can not only learn and adapt to such day-to-day variations or long-term design changes, but also can be applied at scale to the high number of manufacturing units in use today. Using the current state-of-the-art technologies, we then deploy this program at-scale to handle the needs of ever-increasing demand from the manufacturing environment.
Read more7/15/2024
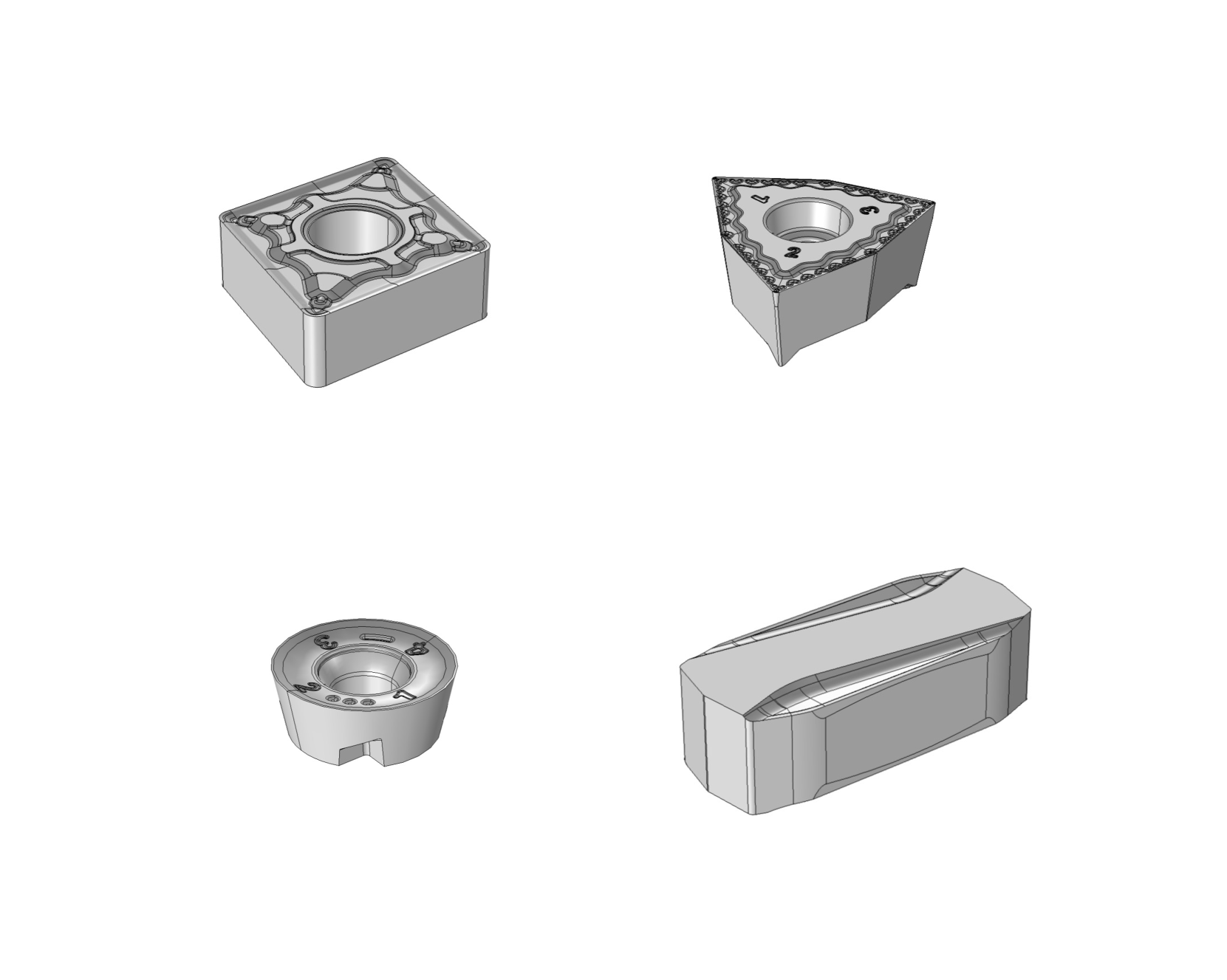

0
Integrating supervised and unsupervised learning approaches to unveil critical process inputs
Paris Papavasileiou, Dimitrios G. Giovanis, Gabriele Pozzetti, Martin Kathrein, Christoph Czettl, Ioannis G. Kevrekidis, Andreas G. Boudouvis, St'ephane P. A. Bordas, Eleni D. Koronaki
This study introduces a machine learning framework tailored to large-scale industrial processes characterized by a plethora of numerical and categorical inputs. The framework aims to (i) discern critical parameters influencing the output and (ii) generate accurate out-of-sample qualitative and quantitative predictions of production outcomes. Specifically, we address the pivotal question of the significance of each input in shaping the process outcome, using an industrial Chemical Vapor Deposition (CVD) process as an example. The initial objective involves merging subject matter expertise and clustering techniques exclusively on the process output, here, coating thickness measurements at various positions in the reactor. This approach identifies groups of production runs that share similar qualitative characteristics, such as film mean thickness and standard deviation. In particular, the differences of the outcomes represented by the different clusters can be attributed to differences in specific inputs, indicating that these inputs are critical for the production outcome. Leveraging this insight, we subsequently implement supervised classification and regression methods using the identified critical process inputs. The proposed methodology proves to be valuable in scenarios with a multitude of inputs and insufficient data for the direct application of deep learning techniques, providing meaningful insights into the underlying processes.
Read more5/14/2024