Design and Characterization of MRI-compatible Plastic Ultrasonic Motor

0

Sign in to get full access
Overview
- Presents the design and characterization of a magnetic resonance imaging (MRI)-compatible plastic ultrasonic motor.
- Highlights the development of a compact and lightweight actuator suitable for use in MRI environments.
- Focuses on the design, fabrication, and performance evaluation of the proposed ultrasonic motor.
Plain English Explanation
The paper describes the development of a special type of motor that can be used in MRI machines. MRI machines are large devices that use powerful magnetic fields to take detailed images of the human body. Traditional motors and actuators often contain metal parts, which can interfere with the magnetic fields in an MRI machine and distort the images.
To address this issue, the researchers designed an MRI-compatible plastic ultrasonic motor. This motor is made mostly of lightweight, non-magnetic plastic materials, which allows it to be used safely inside an MRI machine without causing any interference. The motor uses a unique "ultrasonic" mechanism to generate motion, which is different from the more common electric or magnetic motors.
The researchers carefully designed and tested this plastic ultrasonic motor to ensure it would work reliably and efficiently within the MRI environment. They evaluated its performance, including its speed, torque, and precision, to demonstrate its suitability for various medical and robotic applications that require precise control and movement in confined spaces, such as inside an MRI machine.
Technical Explanation
The paper presents the design and characterization of an MRI-compatible plastic ultrasonic motor. The motor is designed to be used in magnetic resonance imaging (MRI) environments, where traditional metal-based actuators can interfere with the magnetic fields and degrade image quality.
The motor uses a piezoelectric stator made of a Polydimethylsiloxane (PDMS) composite material to generate the ultrasonic vibrations that drive the rotor. The rotor is made of a high-density polyethylene (HDPE) material, which is also non-magnetic and compatible with MRI. The stator and rotor are designed to work together to produce the desired rotational motion.
The researchers fabricated and tested the motor, evaluating its performance characteristics, such as speed, torque, and positioning accuracy. They found that the motor can achieve a maximum speed of 120 rpm and a stall torque of 0.12 Nm, with a positioning accuracy of 0.1 degrees. These results demonstrate the suitability of the plastic ultrasonic motor for use in MRI-guided interventions, rehabilitation robotics, and other applications where precise control and compatibility with magnetic fields are required.
Critical Analysis
The paper provides a thorough design and characterization of the MRI-compatible plastic ultrasonic motor, addressing a important need for actuators that can operate reliably within the MRI environment. The use of non-magnetic, lightweight plastic materials is a key innovation that helps to minimize interference with the magnetic fields.
One potential limitation of the current design is the relatively low torque output compared to the size and weight of the motor. This may limit its usefulness in applications that require higher force capabilities. The researchers acknowledge this and suggest further optimization of the stator and rotor designs to improve the torque density.
Additionally, the paper does not extensively explore the long-term reliability and durability of the plastic ultrasonic motor when subjected to the harsh MRI environment over extended periods. This would be an important area for further investigation to ensure the motor's suitability for real-world medical and robotic applications.
Overall, the research presented in this paper represents a valuable contribution to the development of MRI-compatible actuators and highlights the potential of using innovative materials and mechanisms to overcome the challenges of operating in magnetic fields.
Conclusion
The paper introduces a novel MRI-compatible plastic ultrasonic motor designed to address the limitations of traditional metal-based actuators in magnetic resonance imaging environments. The use of non-magnetic, lightweight plastic materials and a piezoelectric ultrasonic actuation mechanism allows the motor to operate safely and effectively within the MRI setting.
The researchers have demonstrated the feasibility and performance characteristics of the plastic ultrasonic motor through detailed design, fabrication, and testing. The motor's ability to achieve precise control and positioning makes it a promising candidate for various medical and robotic applications, such as MRI-guided interventions and rehabilitation systems, where compatibility with magnetic fields is a critical requirement.
While the current design has some limitations in terms of torque output, the researchers have identified potential areas for further optimization. Continued development and evaluation of the plastic ultrasonic motor's long-term reliability and durability will be important to ensure its widespread adoption in real-world MRI-based applications.
This summary was produced with help from an AI and may contain inaccuracies - check out the links to read the original source documents!
Related Papers


0
Design and Characterization of MRI-compatible Plastic Ultrasonic Motor
Zhanyue Zhao, Charles Bales, Gregory Fischer
Precise surgical procedures may benefit from intra-operative image guidance using magnetic resonance imaging (MRI). However, the MRI's strong magnetic fields, fast switching gradients, and constrained space pose the need for an MR-guided robotic system to assist the surgeon. Piezoelectric actuators can be used in an MRI environment by utilizing the inverse piezoelectric effect for different application purposes. Piezoelectric ultrasonic motor (USM) is one type of MRI-compatible actuator that can actuate these robots with fast response times, compactness, and simple configuration. Although the piezoelectric motors are mostly made of nonferromagnetic material, the generation of eddy currents due to the MRI's gradient fields can lead to magnetic field distortions causing image artifacts. Motor vibrations due to interactions between the MRI's magnetic fields and those generated by the eddy currents can further degrade image quality by causing image artifacts. In this work, a plastic piezoelectric ultrasonic (USM) motor with more degree of MRI compatibility was developed and induced with preliminary optimization. Multiple parameters, namely teeth number, notch size, edge bevel or straight, and surface finish level parameters were used versus the prepressure for the experiment, and the results suggested that using 48 teeth, thin teeth notch with 0.39mm, beveled edge and a surface finish using grit number of approximate 1000 sandpaper performed a better output both in rotary speed and torque. Under this combination, the highest speed reached up to 436.6665rpm when the prepressure was low, and the highest torque reached up to 0.0348Nm when the prepressure was approximately 500g.
Read more9/9/2024


0
Study of MRI-compatible Notched Plastic Ultrasonic Stator with FEM Simulation and Holography Validation
Zhanyue Zhao, Haimi Tang, Paulo Carvalho, Cosme Furlong, Gregory S. Fischer
Intra-operative image guidance using magnetic resonance imaging (MRI) can significantly enhance the precision of surgical procedures, such as deep brain tumor ablation. However, the powerful magnetic fields and limited space within an MRI scanner require the use of robotic devices to aid surgeons. Piezoelectric motors are commonly utilized to drive these robots, with piezoelectric ultrasonic motors being particularly notable. These motors consist of a piezoelectric ring stator that is bonded to a rotor through frictional coupling. When the stator is excited at specific frequencies, it generates distinctive mode shapes with surface waves that exhibit both in-plane and out-of-plane displacement, leading to the rotation of the rotor. In this study, we continue our previous work and refine the motor design and performance, we combine finite element modeling (FEM) with stroboscopic and time-averaged digital holography to validate a further plastic-based ultrasonic motor with better rotary performance.
Read more8/19/2024
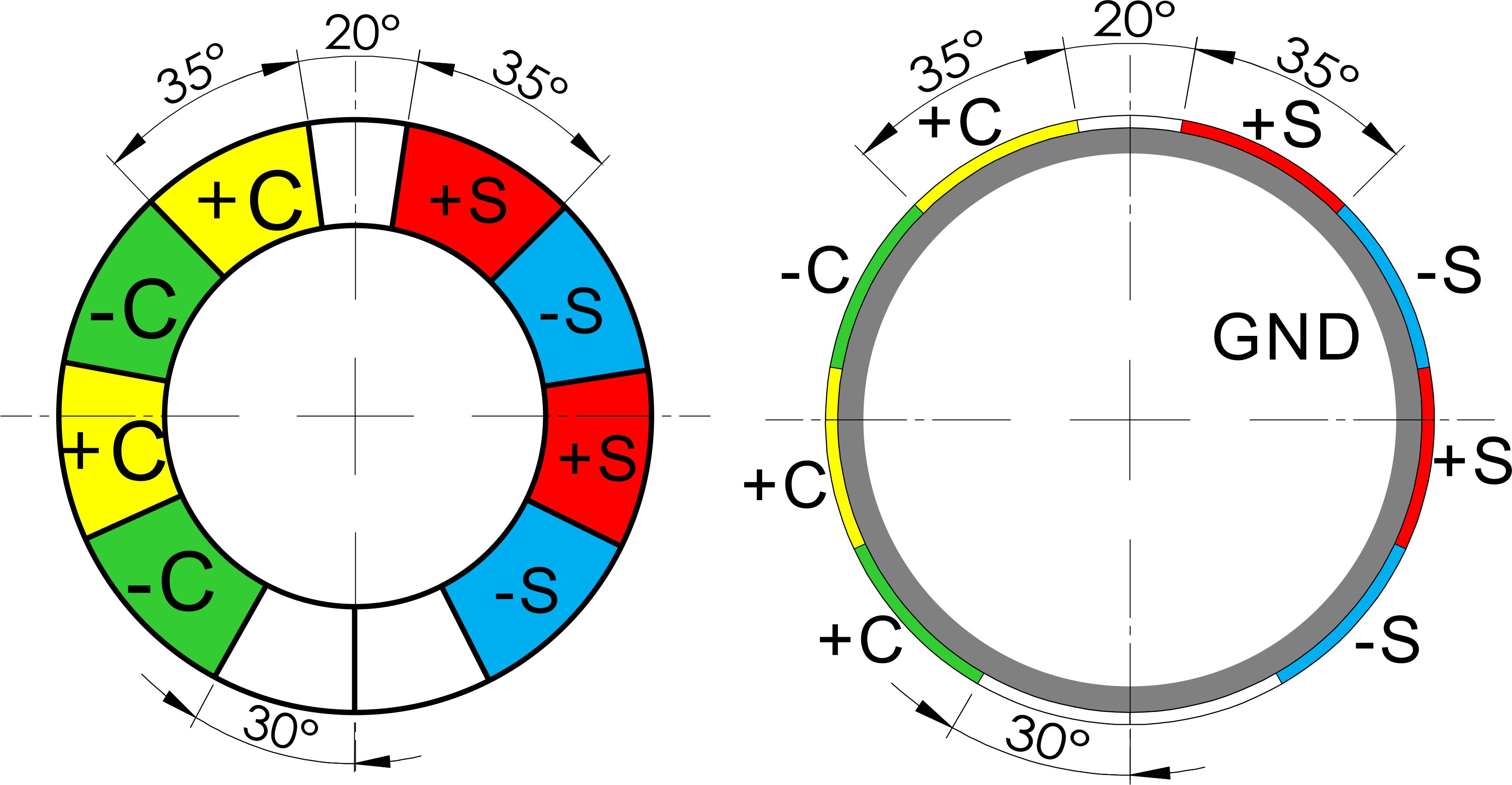

0
Characterization and Design of A Hollow Cylindrical Ultrasonic Motor
Zhanyue Zhao, Yang Wang, Charles Bales, Daniel Ruiz-Cadalso, Howard Zheng, Cosme Furlong-Vazquez, Gregory Fischer
Piezoelectric ultrasonic motors perform the advantages of compact design, faster reaction time, and simpler setup compared to other motion units such as pneumatic and hydraulic motors, especially its non-ferromagnetic property makes it a perfect match in MRI-compatible robotics systems compared to traditional DC motors. Hollow shaft motors address the advantages of being lightweight and comparable to solid shafts of the same diameter, low rotational inertia, high tolerance to rotational imbalance due to low weight, and tolerance to high temperature due to low specific mass. This article presents a prototype of a hollow cylindrical ultrasonic motor (HCM) to perform direct drive, eliminate mechanical non-linearity, and reduce the size and complexity of the actuator or end effector assembly. Two equivalent HCMs are presented in this work, and under 50g prepressure on the rotor, it performed 383.3333rpm rotation speed and 57.3504mNm torque output when applying 282$V_{pp}$ driving voltage.
Read more9/14/2024
🏋️

0
Design and Control of a Compact Series Elastic Actuator Module for Robots in MRI Scanners
Binghan He, Naichen Zhao, David Y. Guo, Charles H. Paxson, Ronald S. Fearing
In this study, we introduce a novel MRI-compatible rotary series elastic actuator module utilizing velocity-sourced ultrasonic motors for force-controlled robots operating within MRI scanners. Unlike previous MRI-compatible SEA designs, our module incorporates a transmission force sensing series elastic actuator structure, with four off-the-shelf compression springs strategically placed between the gearbox housing and the motor housing. This design features a compact size, thus expanding possibilities for a wider range of MRI robotic applications. To achieve precise torque control, we develop a controller that incorporates a disturbance observer tailored for velocity-sourced motors. This controller enhances the robustness of torque control in our actuator module, even in the presence of varying external impedance, thereby augmenting its suitability for MRI-guided medical interventions. Experimental validation demonstrates the actuator's torque control performance in both 3 Tesla MRI and non-MRI environments, achieving a settling time of 0.1 seconds and a steady-state error within 2% of its maximum output torque. Notably, our force controller exhibits consistent performance across low and high external impedance scenarios, in contrast to conventional controllers for velocity-sourced series elastic actuators, which struggle with steady-state performance under low external impedance conditions.
Read more6/13/2024