AutoInspect: Towards Long-Term Autonomous Industrial Inspection

0

Sign in to get full access
Overview
- The paper "AutoInspect: Towards Long-Term Autonomous Industrial Inspection" presents a system for automating industrial inspection tasks over long periods.
- The system uses a mobile robot platform equipped with 3D scanning and change detection capabilities to autonomously inspect industrial environments.
- The key innovations include robust mapping, localization, and change detection algorithms that enable the system to operate reliably over extended durations.
Plain English Explanation
The paper describes a robotic system designed to automatically inspect industrial facilities like factories or warehouses over long periods of time. The system uses a mobile robot that can navigate through these environments and use 3D scanning sensors to capture detailed maps. By comparing new scans to the existing maps, the robot can detect any changes or anomalies that may indicate potential issues or problems.
This is useful because manually inspecting these large, complex facilities is time-consuming and expensive. With the automated real-time inspection capabilities of this system, companies can more efficiently monitor their operations and identify maintenance needs before they become serious problems. The autonomous terrestrial laser scanning abilities allow the robot to inspect areas that may be difficult or dangerous for human workers to access.
The key technical innovations are the algorithms that enable the robot to reliably navigate, map, and detect changes over long periods of time, even as the environments change. This allows the system to operate continuously without the need for manual intervention or recalibration, which is critical for practical deployment in real-world industrial settings.
Technical Explanation
The AutoInspect system is built on a mobile robot platform that is equipped with 3D scanning sensors, such as LIDAR. As the robot navigates through the environment, it builds a detailed 3D map using simultaneous localization and mapping (SLAM) techniques. This map serves as a reference for the robot to localize itself and detect changes over time.
To detect changes, the robot periodically rescans the environment and compares the new data to the original map. The researchers developed advanced change detection algorithms that can robustly identify differences, even in the presence of dynamic obstacles or environmental changes. This allows the system to reliably detect issues like structural damage, equipment malfunctions, or unauthorized modifications.
The mapping and change detection capabilities are critical for long-term autonomous operation, as they enable the robot to adapt to evolving environments without the need for manual intervention or recalibration. The researchers evaluated the system's performance in a series of experiments, demonstrating its ability to operate for extended periods while maintaining accurate localization and effective change detection.
Critical Analysis
The paper presents a compelling approach to automating industrial inspection tasks, addressing the key challenges of long-term robustness and adaptability. The researchers have made significant technical advances in areas like SLAM, change detection, and execution uncertainty handling.
However, the paper does not fully address the potential limitations of the system. For example, the change detection algorithms may struggle to differentiate between intentional modifications and genuine anomalies, leading to false positives or missed issues. Additionally, the system's reliance on 3D scanning sensors could be vulnerable to environmental factors like dust, lighting changes, or occlusions.
Further research could explore ways to improve the system's robustness, such as by incorporating additional sensor modalities or more advanced machine learning techniques for change detection. Additionally, the authors could investigate the system's performance in a wider range of industrial environments and address any practical challenges that may arise during real-world deployment.
Conclusion
The AutoInspect system represents a significant step towards long-term autonomous industrial inspection, with the potential to revolutionize how companies monitor and maintain their facilities. The core technical innovations in mapping, localization, and change detection enable the system to operate reliably over extended periods, addressing a critical need in the industrial automation field.
While the paper highlights the system's promising capabilities, further research is needed to address potential limitations and ensure the robust and reliable performance required for real-world deployment. Nonetheless, the AutoInspect approach demonstrates the power of combining advanced robotics, sensor technology, and algorithmic innovations to tackle complex industrial challenges.
This summary was produced with help from an AI and may contain inaccuracies - check out the links to read the original source documents!
Related Papers


0
AutoInspect: Towards Long-Term Autonomous Industrial Inspection
Michal Staniaszek, Tobit Flatscher, Joseph Rowell, Hanlin Niu, Wenxing Liu, Yang You, Robert Skilton, Maurice Fallon, Nick Hawes
We give an overview of AutoInspect, a ROS-based software system for robust and extensible mission-level autonomy. Over the past three years AutoInspect has been deployed in a variety of environments, including at a mine, a chemical plant, a mock oil rig, decommissioned nuclear power plants, and a fusion reactor for durations ranging from hours to weeks. The system combines robust mapping and localisation with graph-based autonomous navigation, mission execution, and scheduling to achieve a complete autonomous inspection system. The time from arrival at a new site to autonomous mission execution can be under an hour. It is deployed on a Boston Dynamics Spot robot using a custom sensing and compute payload called Frontier. In this work we go into detail of the system's performance in two long-term deployments of 49 days at a robotics test facility, and 35 days at the Joint European Torus (JET) fusion reactor in Oxfordshire, UK.
Read more4/24/2024


0
Automated Real-Time Inspection in Indoor and Outdoor 3D Environments with Cooperative Aerial Robots
Andreas Anastasiou, Angelos Zacharia, Savvas Papaioannou, Panayiotis Kolios, Christos G. Panayiotou, Marios M. Polycarpou
This work introduces a cooperative inspection system designed to efficiently control and coordinate a team of distributed heterogeneous UAV agents for the inspection of 3D structures in cluttered, unknown spaces. Our proposed approach employs a two-stage innovative methodology. Initially, it leverages the complementary sensing capabilities of the robots to cooperatively map the unknown environment. It then generates optimized, collision-free inspection paths, thereby ensuring comprehensive coverage of the structure's surface area. The effectiveness of our system is demonstrated through qualitative and quantitative results from extensive Gazebo-based simulations that closely replicate real-world inspection scenarios, highlighting its ability to thoroughly inspect real-world-like 3D structures.
Read more4/19/2024
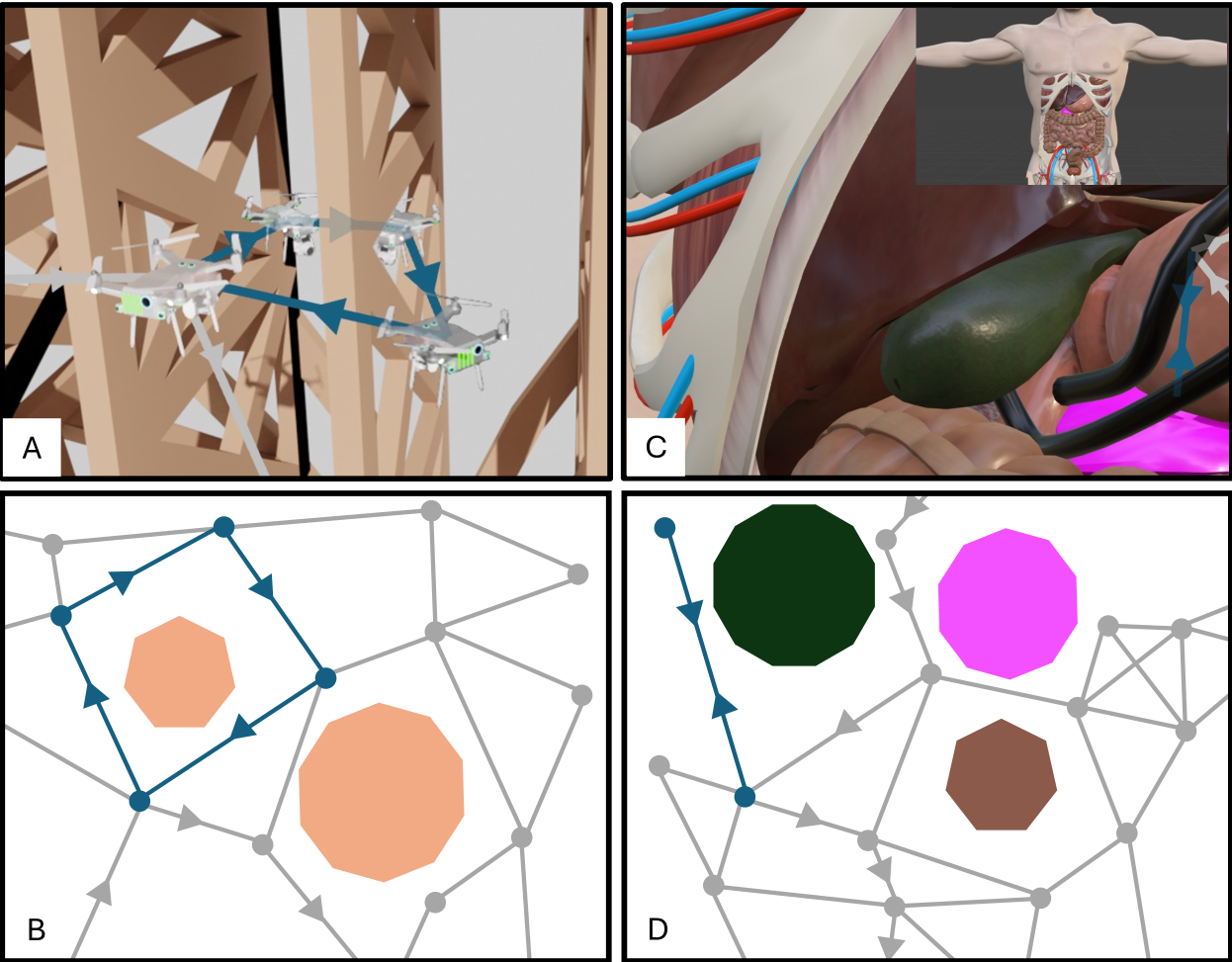

0
Leveraging Fixed-Parameter Tractability for Robot Inspection Planning
Yosuke Mizutani, Daniel Coimbra Salomao, Alex Crane, Matthias Bentert, P{aa}l Gr{o}n{aa}s Drange, Felix Reidl, Alan Kuntz, Blair D. Sullivan
Autonomous robotic inspection, where a robot moves through its environment and inspects points of interest, has applications in industrial settings, structural health monitoring, and medicine. Planning the paths for a robot to safely and efficiently perform such an inspection is an extremely difficult algorithmic challenge. In this work we consider an abstraction of the inspection planning problem which we term Graph Inspection. We give two exact algorithms for this problem, using dynamic programming and integer linear programming. We analyze the performance of these methods, and present multiple approaches to achieve scalability. We demonstrate significant improvement both in path weight and inspection coverage over a state-of-the-art approach on two robotics tasks in simulation, a bridge inspection task by a UAV and a surgical inspection task using a medical robot.
Read more9/19/2024
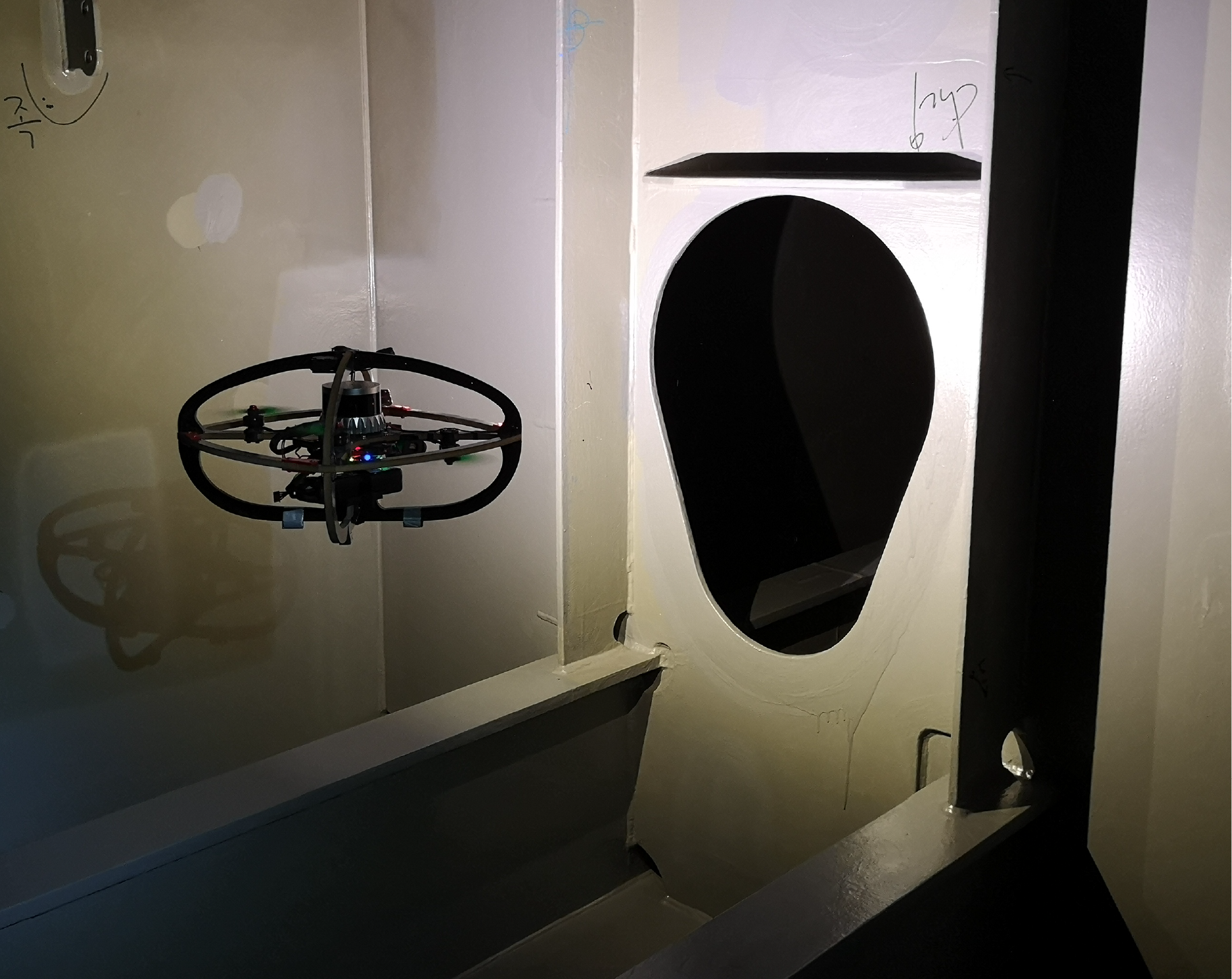

0
Maritime Vessel Tank Inspection using Aerial Robots: Experience from the field and dataset release
Mihir Dharmadhikari, Nikhil Khedekar, Paolo De Petris, Mihir Kulkarni, Morten Nissov, Kostas Alexis
This paper presents field results and lessons learned from the deployment of aerial robots inside ship ballast tanks. Vessel tanks including ballast tanks and cargo holds present dark, dusty environments having simultaneously very narrow openings and wide open spaces that create several challenges for autonomous navigation and inspection operations. We present a system for vessel tank inspection using an aerial robot along with its autonomy modules. We show the results of autonomous exploration and visual inspection in 3 ships spanning across 7 distinct types of sections of the ballast tanks. Additionally, we comment on the lessons learned from the field and possible directions for future work. Finally, we release a dataset consisting of the data from these missions along with data collected with a handheld sensor stick.
Read more5/1/2024