Fast and Accurate Relative Motion Tracking for Two Industrial Robots
2404.06687

0

0
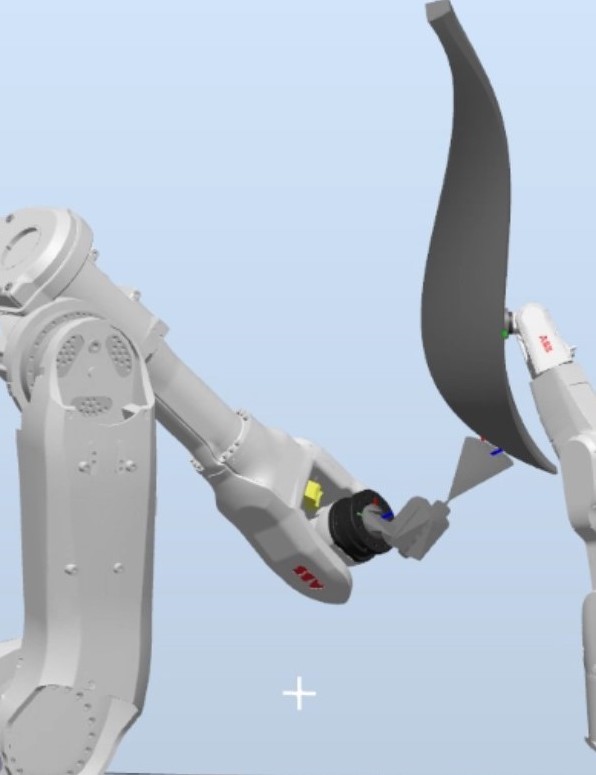
Abstract
Industrial robotic applications such as spraying, welding, and additive manufacturing frequently require fast, accurate, and uniform motion along a 3D spatial curve. To increase process throughput, some manufacturers propose a dual-robot setup to overcome the speed limitation of a single robot. Industrial robot motion is programmed through waypoints connected by motion primitives (Cartesian linear and circular paths and linear joint paths at constant Cartesian speed). The actual robot motion is affected by the blending between these motion primitives and the pose of the robot (an outstretched/close to singularity pose tends to have larger path-tracking errors). Choosing the waypoints and the speed along each motion segment to achieve the performance requirement is challenging. At present, there is no automated solution, and laborious manual tuning by robot experts is needed to approach the desired performance. In this paper, we present a systematic three-step approach to designing and programming a dual-robot system to optimize system performance. The first step is to select the relative placement between the two robots based on the specified relative motion path. The second step is to select the relative waypoints and the motion primitives. The final step is to update the waypoints iteratively based on the actual relative motion. Waypoint iteration is first executed in simulation and then completed using the actual robots. For performance measures, we use the mean path speed subject to the relative position and orientation constraints and the path speed uniformity constraint. We have demonstrated the effectiveness of this method with ABB and FANUC robots on two challenging test curves. The performance improvement over the current industrial practice baseline is over 300%. Compared to the optimized single-arm case that we have previously reported, the improvement is over 14%.
Create account to get full access
Overview
- This paper presents a fast and accurate method for tracking the relative motion between two industrial robots.
- The method uses visual information from cameras mounted on the robots to estimate their relative position and orientation in real-time.
- The authors demonstrate the effectiveness of their approach through experiments on industrial robot platforms.
Plain English Explanation
The paper describes a new way to track how two industrial robots are moving in relation to each other. The key idea is to use cameras mounted on the robots to continuously monitor their relative position and orientation. This allows the robots to know where they are compared to one another, which is important for coordinating their movements during tasks like assembly or manufacturing.
The authors' approach is designed to be both fast and accurate, meaning it can track the robots' motions in real-time without sacrificing precision. This is crucial for industrial applications where the robots need to move quickly and precisely to be efficient and avoid collisions.
The authors test their method on actual industrial robot platforms and show that it outperforms existing techniques in terms of speed and accuracy. This suggests their approach could be a valuable tool for industries that rely on coordinated robot movements, such as automotive manufacturing or robotic surgery.
Technical Explanation
The paper proposes a visual-inertial fusion approach for fast and accurate relative motion tracking between two industrial robots. The method uses cameras mounted on the robots to capture visual information about their relative pose (position and orientation). This data is combined with inertial measurements from sensors on the robots to estimate their relative motion in real-time.
The authors formulate the relative pose estimation as an optimization problem, which they solve efficiently using a novel iterative framework. This allows the system to track the robots' motions at high frequencies, essential for industrial applications where speed and precision are crucial.
The authors evaluate their approach through experiments on two industrial robot platforms. They compare the performance of their method to alternative techniques and demonstrate significant improvements in terms of tracking accuracy and update rate. The results suggest the proposed approach could be a valuable tool for coordinating the movements of multiple robots in manufacturing, assembly, and other industrial settings.
Critical Analysis
The paper presents a compelling solution for the important problem of accurately tracking the relative motion between industrial robots. The authors' visual-inertial fusion approach appears well-designed and the experimental results are promising.
However, the paper does not thoroughly address some potential limitations or caveats. For example, the method may struggle in environments with poor lighting or visual features, which could degrade the accuracy of the visual tracking. Additionally, the reliance on specialized cameras and sensors on the robots could limit the scalability and cost-effectiveness of the approach, especially for smaller-scale operations.
The authors also do not discuss how their method might handle occlusions, where one robot blocks the view of the other from the cameras. This could be a significant challenge in cluttered industrial environments. Further research into addressing these types of real-world constraints would help strengthen the practicality of the proposed solution.
Additionally, the paper could benefit from a more in-depth discussion of the potential sources of error in the relative motion tracking and how the authors' approach mitigates these issues. A deeper technical analysis of the strengths and limitations of the method would help readers better understand its capabilities and potential applications.
Conclusion
Overall, this paper presents a promising new approach for fast and accurate relative motion tracking between industrial robots. The authors' visual-inertial fusion method demonstrates strong performance in experimental evaluations, suggesting it could be a valuable tool for improving the coordination and efficiency of multi-robot systems in manufacturing and other industrial settings.
While the paper does not address all potential limitations, the core idea and implementation appear to be a meaningful contribution to the field of robotics and automation. Further research and refinement of the approach could lead to even more robust and practical solutions for industrial applications that rely on the precise control and coordination of multiple robotic manipulators.
This summary was produced with help from an AI and may contain inaccuracies - check out the links to read the original source documents!
Related Papers

Path Planning and Motion Control for Accurate Positioning of Car-like Robots
Jin Dai, Zejiang Wang, Yebin Wang, Rien Quirynen, Stefano Di Cairano

0

0
This paper investigates the planning and control for accurate positioning of car-like robots. We propose a solution that integrates two modules: a motion planner, facilitated by the rapidly-exploring random tree algorithm and continuous-curvature (CC) steering technique, generates a CC trajectory as a reference; and a nonlinear model predictive controller (NMPC) regulates the robot to accurately track the reference trajectory. Based on the $mu$-tangency conditions in prior art, we derive explicit existence conditions and develop associated computation methods for a special class of CC paths which not only admit the same driving patterns as Reeds-Shepp paths but also consist of cusp-free clothoid turns. Afterwards, we create an autonomous vehicle parking scenario where the NMPC endeavors to follow the reference trajectory. Feasibility and computational efficiency of the CC steering are validated by numerical simulation. CarSim-Simulink joint simulations statistically verify that with exactly same NMPC, the closed-loop system with CC trajectories as references substantially outperforms the case where Reeds-Shepp trajectories are used as references.
6/11/2024
📉
A Hybrid Task-Constrained Motion Planning for Collaborative Robots in Intelligent Remanufacturing
Wansong Liu, Chang Liu, Xiao Liang, Minghui Zheng

0

0
Industrial manipulators have extensively collaborated with human operators to execute tasks, e.g., disassembly of end-of-use products, in intelligent remanufacturing. A safety task execution requires real-time path planning for the manipulator's end-effector to autonomously avoid human operators. This is even more challenging when the end-effector needs to follow a planned path while avoiding the collision between the manipulator body and human operators, which is usually computationally expensive and limits real-time application. This paper proposes an efficient hybrid motion planning algorithm that consists of an A$^*$ algorithm and an online manipulator reconfiguration mechanism (OMRM) to tackle such challenges in task and configuration spaces respectively. The A$^*$ algorithm is first leveraged to plan the shortest collision-free path of the end-effector in task space. When the manipulator body is risky to the human operator, our OMRM then selects an alternative joint configuration with minimum reconfiguration effort from a database to assist the manipulator to follow the planned path and avoid the human operator simultaneously. The database of manipulator reconfiguration establishes the relationship between the task and configuration space offline using forward kinematics, and is able to provide multiple reconfiguration candidates for a desired end-effector's position. The proposed new hybrid algorithm plans safe manipulator motion during the whole task execution. Extensive numerical and experimental studies, as well as comparison studies between the proposed one and the state-of-the-art ones, have been conducted to validate the proposed motion planning algorithm.
6/13/2024
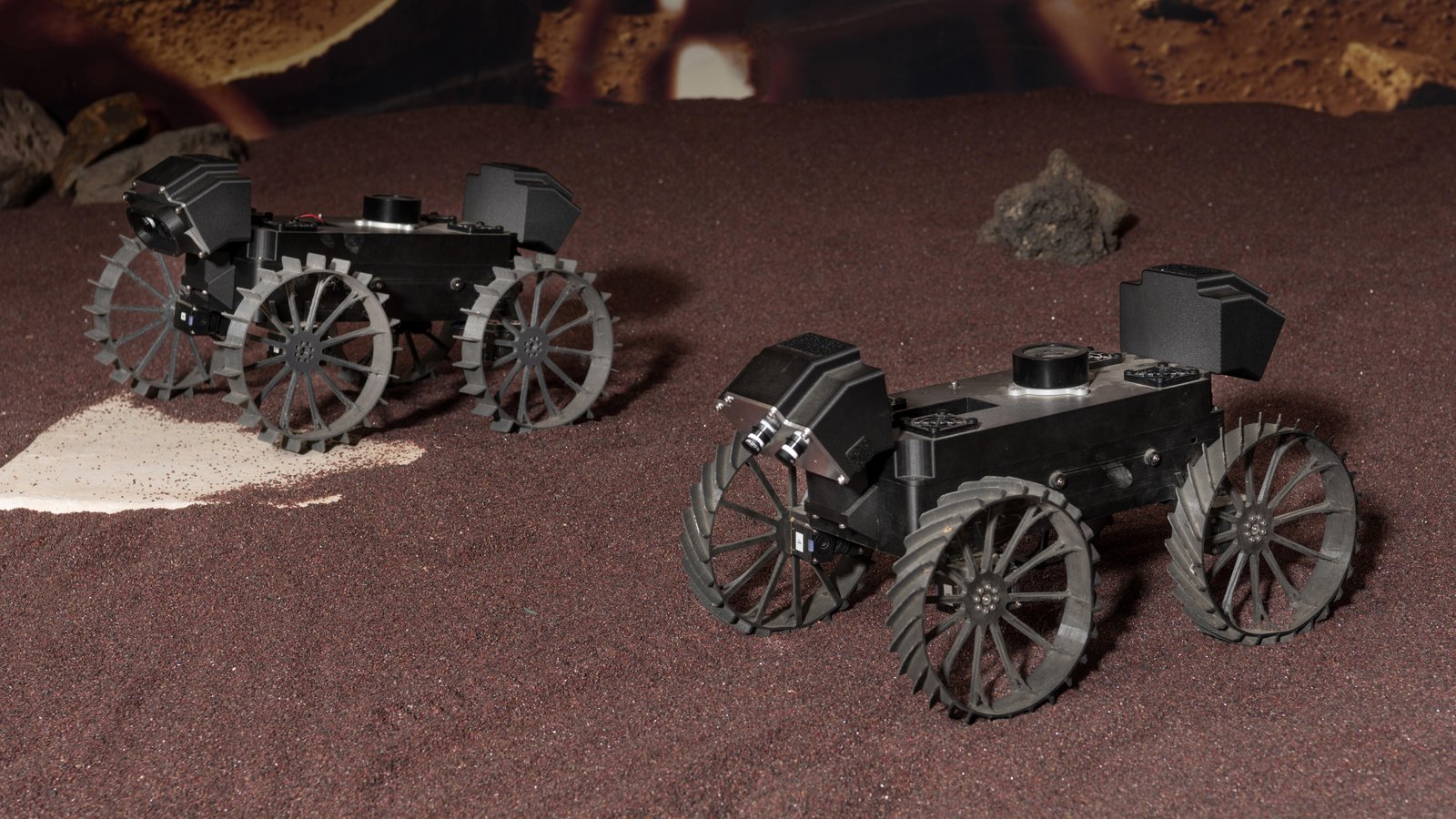
Multi-Robot Collaborative Localization and Planning with Inter-Ranging
Derek Knowles, Adam Dai, Grace Gao

0

0
Robots often use feature-based image tracking to identify their position in their surrounding environment; however, feature-based image tracking is prone to errors in low-textured and poorly lit environments. Specifically, we investigate a scenario where robots are tasked with exploring the surface of the Moon and are required to have an accurate estimate of their position to be able to correctly geotag scientific measurements. To reduce localization error, we complement traditional feature-based image tracking with ultra-wideband (UWB) distance measurements between the robots. The robots use an advanced mesh-ranging protocol that allows them to continuously share distance measurements amongst each other rather than relying on the common anchor and tag UWB architecture. We develop a decentralized multi-robot coordination algorithm that actively plans paths based on measurement line-of-sight vectors amongst all robots to minimize collective localization error. We then demonstrate the emergent behavior of the proposed multi-robot coordination algorithm both in simulation and hardware to lower a geometry-based uncertainty metric and reduce localization error.
6/26/2024
📊
Fast Estimation of Relative Transformation Based on Fusion of Odometry and UWB Ranging Data
Yuan Fu, Zheng Zhang, Guangyang Zeng, Chun Liu, Junfeng Wu, Xiaoqiang Ren

0

0
In this paper, we investigate the problem of estimating the 4-DOF (three-dimensional position and orientation) robot-robot relative frame transformation using odometers and distance measurements between robots. Firstly, we apply a two-step estimation method based on maximum likelihood estimation. Specifically, a good initial value is obtained through unconstrained least squares and projection, followed by a more accurate estimate achieved through one-step Gauss-Newton iteration. Additionally, the optimal installation positions of Ultra-Wideband (UWB) are provided, and the minimum operating time under different quantities of UWB devices is determined. Simulation demonstrates that the two-step approach offers faster computation with guaranteed accuracy while effectively addressing the relative transformation estimation problem within limited space constraints. Furthermore, this method can be applied to real-time relative transformation estimation when a specific number of UWB devices are installed.
5/22/2024