GBEC: Geometry-Based Hand-Eye Calibration

0
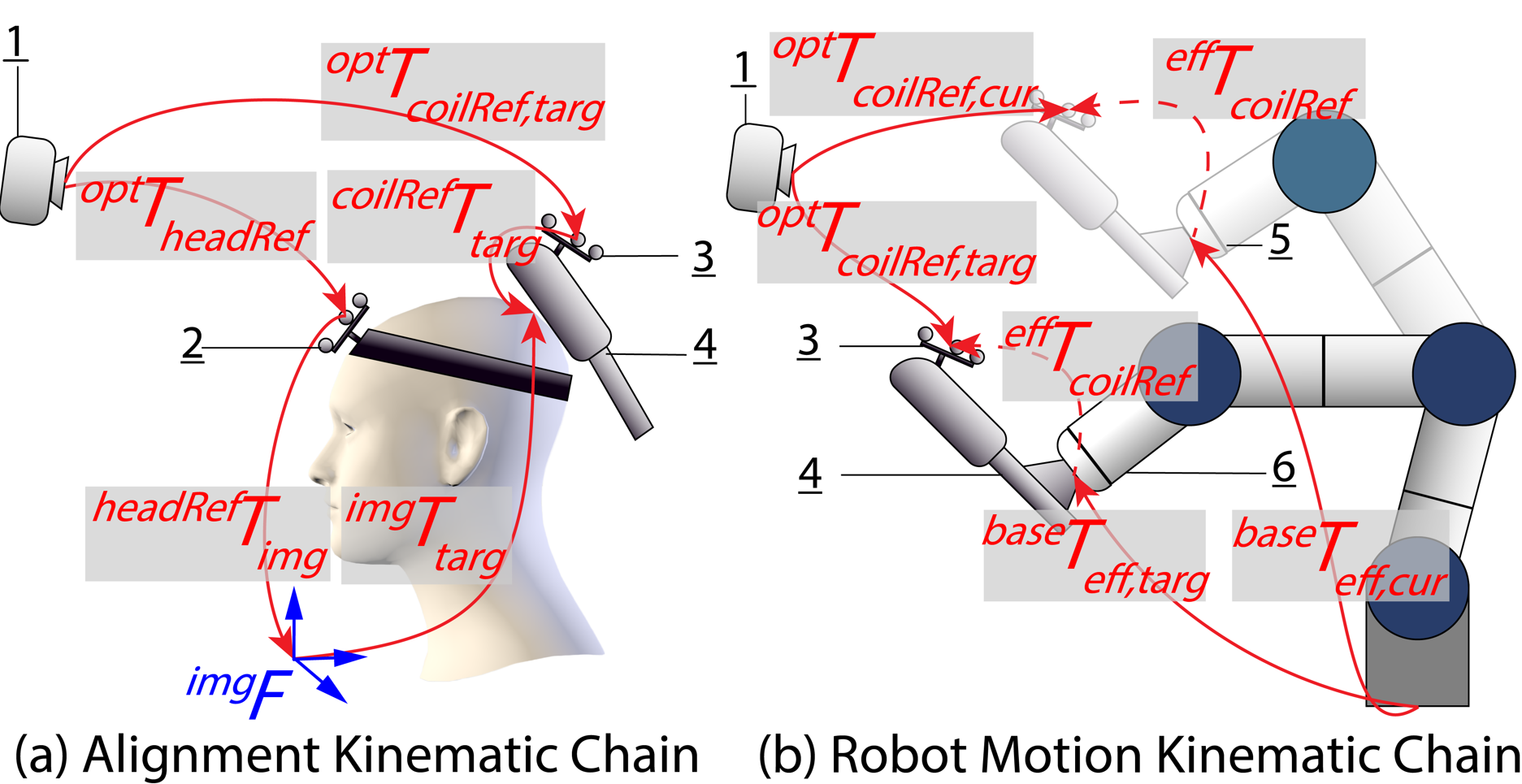
Sign in to get full access
Overview
- This paper presents a geometry-based hand-eye calibration (GBEC) method for accurately aligning a robot's end-effector with its camera.
- GBEC uses geometric constraints to estimate the transformation between the end-effector and camera, without requiring complex calibration objects or procedures.
- The method is demonstrated to be effective for applications like robot-assisted transcranial magnetic stimulation and robot-assisted femoroplasty.
Plain English Explanation
The paper describes a new technique called geometry-based hand-eye calibration (GBEC) that helps a robot's camera and end-effector (the part that interacts with objects) work together smoothly. Typically, getting a robot's camera and end-effector to be perfectly aligned is tricky and requires complex setup procedures. GBEC solves this by using the geometric properties of the robot's parts to figure out how the camera and end-effector are related, without needing special calibration tools.
This is important for applications where a robot needs to precisely interact with the world, like administering transcranial magnetic stimulation to the brain or performing femoroplasty surgery. By automatically calibrating the camera and end-effector, GBEC helps the robot carry out these delicate tasks more accurately and reliably.
Technical Explanation
The key idea behind GBEC is to leverage the geometric constraints between the robot's end-effector and camera to estimate their relative transformation, without requiring explicit calibration objects or procedures. The method works by first moving the end-effector to various positions and orientations, and recording the corresponding camera observations.
From this data, GBEC constructs a set of geometric constraints that the end-effector-camera transformation must satisfy. These constraints are then used to solve for the optimal transformation parameters that best fit the observed data. The authors show that this approach can accurately estimate the end-effector-camera relationship using only the robot's own movements, without needing external calibration tools.
GBEC is demonstrated on two robotic systems: one for robot-assisted transcranial magnetic stimulation and another for robot-assisted femoroplasty. In both cases, the GBEC method was able to achieve accurate hand-eye calibration, enabling the robots to precisely interact with their environments.
Critical Analysis
The key strength of the GBEC method is its ability to perform hand-eye calibration without requiring specialized calibration objects or complex procedures. This makes it easier to deploy in real-world robotic systems, where simplicity and ease of use are important.
However, the paper does not extensively explore the limits of GBEC's accuracy or robustness. For example, it's unclear how the method would perform in the presence of significant noise or other real-world disturbances. The experiments also focus on relatively simple, constrained robot motions, so further research may be needed to understand GBEC's behavior in more complex or unconstrained environments.
Additionally, the paper does not provide a detailed comparison to other hand-eye calibration techniques, such as those based on feature matching or tool pose estimation. A more thorough benchmarking against state-of-the-art methods could help better situate the GBEC approach and identify its unique strengths and limitations.
Conclusion
The GBEC method presented in this paper offers a promising new approach to hand-eye calibration for robotic systems. By leveraging the inherent geometric constraints of the robot's structure, GBEC can accurately align the end-effector and camera without requiring complex setup or calibration procedures. This simplicity and ease of use could make GBEC an attractive choice for a variety of robotic applications, such as transcranial magnetic stimulation and femoroplasty surgery, where precise end-effector control is crucial.
Further research is needed to fully understand the limits and potential of the GBEC method, but this work represents an important contribution to the field of robot calibration and control.
This summary was produced with help from an AI and may contain inaccuracies - check out the links to read the original source documents!
Related Papers
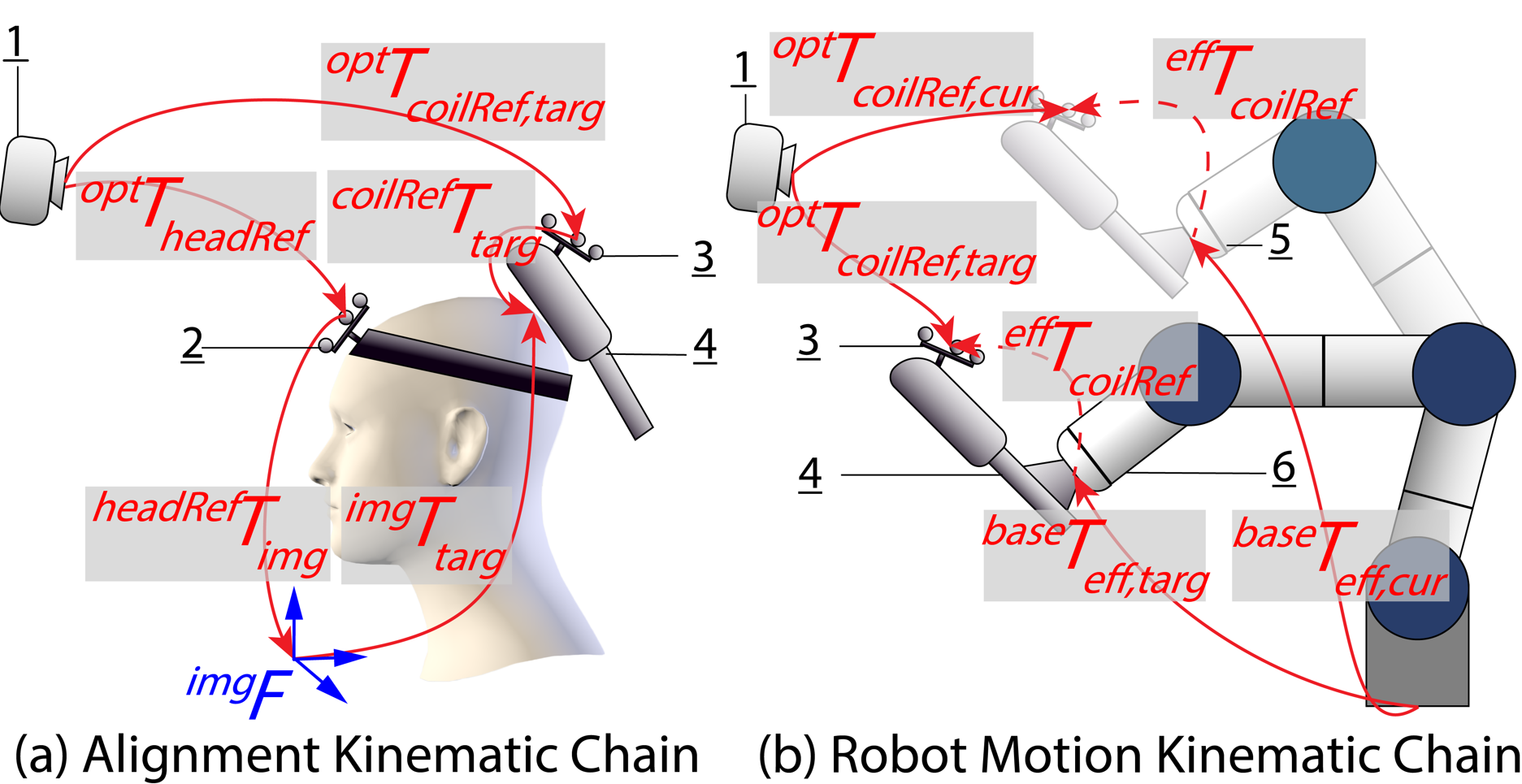

0
GBEC: Geometry-Based Hand-Eye Calibration
Yihao Liu, Jiaming Zhang, Zhangcong She, Amir Kheradmand, Mehran Armand
Hand-eye calibration is the problem of solving the transformation from the end-effector of a robot to the sensor attached to it. Commonly employed techniques, such as AXXB or AXZB formulations, rely on regression methods that require collecting pose data from different robot configurations, which can produce low accuracy and repeatability. However, the derived transformation should solely depend on the geometry of the end-effector and the sensor attachment. We propose Geometry-Based End-Effector Calibration (GBEC) that enhances the repeatability and accuracy of the derived transformation compared to traditional hand-eye calibrations. To demonstrate improvements, we apply the approach to two different robot-assisted procedures: Transcranial Magnetic Stimulation (TMS) and femoroplasty. We also discuss the generalizability of GBEC for camera-in-hand and marker-in-hand sensor mounting methods. In the experiments, we perform GBEC between the robot end-effector and an optical tracker's rigid body marker attached to the TMS coil or femoroplasty drill guide. Previous research documents low repeatability and accuracy of the conventional methods for robot-assisted TMS hand-eye calibration. When compared to some existing methods, the proposed method relies solely on the geometry of the flange and the pose of the rigid-body marker, making it independent of workspace constraints or robot accuracy, without sacrificing the orthogonality of the rotation matrix. Our results validate the accuracy and applicability of the approach, providing a new and generalizable methodology for obtaining the transformation from the end-effector to a sensor.
Read more4/10/2024
👀

0
Automatic Robot Hand-Eye Calibration Enabled by Learning-Based 3D Vision
Leihui Li, Xingyu Yang, Riwei Wang, Xuping Zhang
Hand-eye calibration, as a fundamental task in vision-based robotic systems, aims to estimate the transformation matrix between the coordinate frame of the camera and the robot flange. Most approaches to hand-eye calibration rely on external markers or human assistance. We proposed Look at Robot Base Once (LRBO), a novel methodology that addresses the hand-eye calibration problem without external calibration objects or human support, but with the robot base. Using point clouds of the robot base, a transformation matrix from the coordinate frame of the camera to the robot base is established as I=AXB. To this end, we exploit learning-based 3D detection and registration algorithms to estimate the location and orientation of the robot base. The robustness and accuracy of the method are quantified by ground-truth-based evaluation, and the accuracy result is compared with other 3D vision-based calibration methods. To assess the feasibility of our methodology, we carried out experiments utilizing a low-cost structured light scanner across varying joint configurations and groups of experiments. The proposed hand-eye calibration method achieved a translation deviation of 0.930 mm and a rotation deviation of 0.265 degrees according to the experimental results. Additionally, the 3D reconstruction experiments demonstrated a rotation error of 0.994 degrees and a position error of 1.697 mm. Moreover, our method offers the potential to be completed in 1 second, which is the fastest compared to other 3D hand-eye calibration methods. Code is released at github.com/leihui6/LRBO.
Read more9/6/2024


0
On Flange-based 3D Hand-Eye Calibration for Soft Robotic Tactile Welding
Xudong Han, Ning Guo, Yu Jie, He Wang, Fang Wan, Chaoyang Song
This paper investigates the direct application of standardized designs on the robot for conducting robot hand-eye calibration by employing 3D scanners with collaborative robots. The well-established geometric features of the robot flange are exploited by directly capturing its point cloud data. In particular, an iterative method is proposed to facilitate point cloud processing toward a refined calibration outcome. Several extensive experiments are conducted over a range of collaborative robots, including Universal Robots UR5 & UR10 e-series, Franka Emika, and AUBO i5 using an industrial-grade 3D scanner Photoneo Phoxi S & M and a commercial-grade 3D scanner Microsoft Azure Kinect DK. Experimental results show that translational and rotational errors converge efficiently to less than 0.28 mm and 0.25 degrees, respectively, achieving a hand-eye calibration accuracy as high as the camera's resolution, probing the hardware limit. A welding seam tracking system is presented, combining the flange-based calibration method with soft tactile sensing. The experiment results show that the system enables the robot to adjust its motion in real-time, ensuring consistent weld quality and paving the way for more efficient and adaptable manufacturing processes.
Read more7/30/2024


0
Multi-Camera Hand-Eye Calibration for Human-Robot Collaboration in Industrial Robotic Workcells
Davide Allegro, Matteo Terreran, Stefano Ghidoni
In industrial scenarios, effective human-robot collaboration relies on multi-camera systems to robustly monitor human operators despite the occlusions that typically show up in a robotic workcell. In this scenario, precise localization of the person in the robot coordinate system is essential, making the hand-eye calibration of the camera network critical. This process presents significant challenges when high calibration accuracy should be achieved in short time to minimize production downtime, and when dealing with extensive camera networks used for monitoring wide areas, such as industrial robotic workcells. Our paper introduces an innovative and robust multi-camera hand-eye calibration method, designed to optimize each camera's pose relative to both the robot's base and to each other camera. This optimization integrates two types of key constraints: i) a single board-to-end-effector transformation, and ii) the relative camera-to-camera transformations. We demonstrate the superior performance of our method through comprehensive experiments employing the METRIC dataset and real-world data collected on industrial scenarios, showing notable advancements over state-of-the-art techniques even using less than 10 images. Additionally, we release an open-source version of our multi-camera hand-eye calibration algorithm at https://github.com/davidea97/Multi-Camera-Hand-Eye-Calibration.git.
Read more6/18/2024