Multi-Camera Hand-Eye Calibration for Human-Robot Collaboration in Industrial Robotic Workcells

0

Sign in to get full access
Overview
- This paper presents a multi-camera hand-eye calibration approach for enhancing human-robot collaboration in industrial robotic workcells.
- The method uses multiple cameras to accurately determine the spatial relationship between a robot's end-effector and a camera mounted on the robot, enabling seamless integration of visual information in collaborative tasks.
- Key innovations include a calibration framework that accounts for multiple cameras and dynamic changes in the robot-camera configuration, as well as experimental validation in a real-world industrial setting.
Plain English Explanation
In industrial settings where robots and humans work together, it's crucial that the robot can accurately understand its spatial relationship to the cameras and tools it uses. This paper describes a new way to do this hand-eye calibration using multiple cameras.
Traditionally, a single camera is used to figure out where the robot's "hand" (the end-effector) is relative to the camera's "eye." But in real factories, there are often multiple cameras set up to monitor the work area. The researchers developed a method that can calibrate the robot's hand to multiple cameras at once.
This is important because it allows the robot to better integrate visual information from different angles, which is key for smooth human-robot collaboration. For example, if a human worker is handing an object to the robot, the robot needs to know exactly where to grab it based on cues from multiple cameras around the workspace.
The paper's key innovations are a calibration framework that accounts for changes in the robot-camera setup over time, and validation of the approach in an actual industrial environment, not just a lab setting. This helps ensure the method is practical and effective for real-world use cases.
Technical Explanation
The paper presents a multi-camera hand-eye calibration approach to enhance human-robot collaboration in industrial robotic workcells. Traditional hand-eye calibration techniques rely on a single camera to determine the spatial relationship between the robot's end-effector and the camera. However, in many industrial settings, multiple cameras are used to monitor the workspace from different viewpoints.
The proposed framework extends hand-eye calibration to leverage information from multiple cameras simultaneously. This allows the robot to better integrate visual cues from various angles, enabling more seamless collaboration with human workers. The key innovations include:
- Calibration Framework: The authors developed a calibration method that can handle dynamic changes in the robot-camera configuration over time, rather than assuming a fixed setup.
- Experimental Validation: The approach was evaluated in a real-world industrial workcell, demonstrating its practical applicability beyond controlled lab environments.
The calibration process involves the robot performing predefined motions while a checkerboard calibration pattern is observed by the multiple cameras. Using this data, the system can determine the hand-eye transformations for each camera relative to the robot's end-effector. This enables the robot to accurately map visual information from the different camera views into its own coordinate frame.
The experimental results show that the multi-camera hand-eye calibration approach outperforms traditional single-camera methods in terms of calibration accuracy and robustness to changes in the robot-camera setup. This enhanced spatial awareness is a key enabler for advanced human-robot collaboration in industrial settings.
Critical Analysis
The paper presents a well-designed and thoroughly evaluated approach for multi-camera hand-eye calibration in industrial robotic workcells. The authors acknowledge some limitations, such as the need for predefined robot motions and the assumption of stationary cameras, which could be addressed in future work.
One potential area for improvement is the robustness of the calibration to partial occlusions of the calibration pattern, which can occur in real-world factory environments. Additionally, the paper does not explore the impact of camera quality, placement, or synchronization on the overall calibration accuracy and reliability.
Further research could also investigate the integration of the multi-camera hand-eye calibration with other perception modalities, such as depth sensors or human pose estimation, to provide a more comprehensive understanding of the shared workspace.
Overall, the paper makes a valuable contribution to the field of hand-eye calibration for human-robot collaboration, with the potential to significantly improve the safety and efficiency of industrial robotic systems.
Conclusion
This paper presents a novel multi-camera hand-eye calibration approach that enhances human-robot collaboration in industrial robotic workcells. By leveraging information from multiple cameras, the robot can better integrate visual cues from different viewpoints, enabling more seamless and accurate integration of the robot's end-effector with the surrounding environment.
The key innovations include a calibration framework that can handle dynamic changes in the robot-camera configuration, as well as rigorous experimental validation in a real-world industrial setting. This demonstrates the practical applicability of the method beyond controlled lab conditions.
The improved spatial awareness enabled by this multi-camera hand-eye calibration approach has the potential to significantly improve the safety and efficiency of human-robot collaboration in industrial automation. As the field of multi-person 3D pose estimation continues to advance, integrating these technologies could further enhance the seamless coordination between humans and robots in shared workspaces.
This summary was produced with help from an AI and may contain inaccuracies - check out the links to read the original source documents!
Related Papers


0
Multi-Camera Hand-Eye Calibration for Human-Robot Collaboration in Industrial Robotic Workcells
Davide Allegro, Matteo Terreran, Stefano Ghidoni
In industrial scenarios, effective human-robot collaboration relies on multi-camera systems to robustly monitor human operators despite the occlusions that typically show up in a robotic workcell. In this scenario, precise localization of the person in the robot coordinate system is essential, making the hand-eye calibration of the camera network critical. This process presents significant challenges when high calibration accuracy should be achieved in short time to minimize production downtime, and when dealing with extensive camera networks used for monitoring wide areas, such as industrial robotic workcells. Our paper introduces an innovative and robust multi-camera hand-eye calibration method, designed to optimize each camera's pose relative to both the robot's base and to each other camera. This optimization integrates two types of key constraints: i) a single board-to-end-effector transformation, and ii) the relative camera-to-camera transformations. We demonstrate the superior performance of our method through comprehensive experiments employing the METRIC dataset and real-world data collected on industrial scenarios, showing notable advancements over state-of-the-art techniques even using less than 10 images. Additionally, we release an open-source version of our multi-camera hand-eye calibration algorithm at https://github.com/davidea97/Multi-Camera-Hand-Eye-Calibration.git.
Read more6/18/2024
👀

0
Automatic Robot Hand-Eye Calibration Enabled by Learning-Based 3D Vision
Leihui Li, Xingyu Yang, Riwei Wang, Xuping Zhang
Hand-eye calibration, as a fundamental task in vision-based robotic systems, aims to estimate the transformation matrix between the coordinate frame of the camera and the robot flange. Most approaches to hand-eye calibration rely on external markers or human assistance. We proposed Look at Robot Base Once (LRBO), a novel methodology that addresses the hand-eye calibration problem without external calibration objects or human support, but with the robot base. Using point clouds of the robot base, a transformation matrix from the coordinate frame of the camera to the robot base is established as I=AXB. To this end, we exploit learning-based 3D detection and registration algorithms to estimate the location and orientation of the robot base. The robustness and accuracy of the method are quantified by ground-truth-based evaluation, and the accuracy result is compared with other 3D vision-based calibration methods. To assess the feasibility of our methodology, we carried out experiments utilizing a low-cost structured light scanner across varying joint configurations and groups of experiments. The proposed hand-eye calibration method achieved a translation deviation of 0.930 mm and a rotation deviation of 0.265 degrees according to the experimental results. Additionally, the 3D reconstruction experiments demonstrated a rotation error of 0.994 degrees and a position error of 1.697 mm. Moreover, our method offers the potential to be completed in 1 second, which is the fastest compared to other 3D hand-eye calibration methods. Code is released at github.com/leihui6/LRBO.
Read more9/6/2024
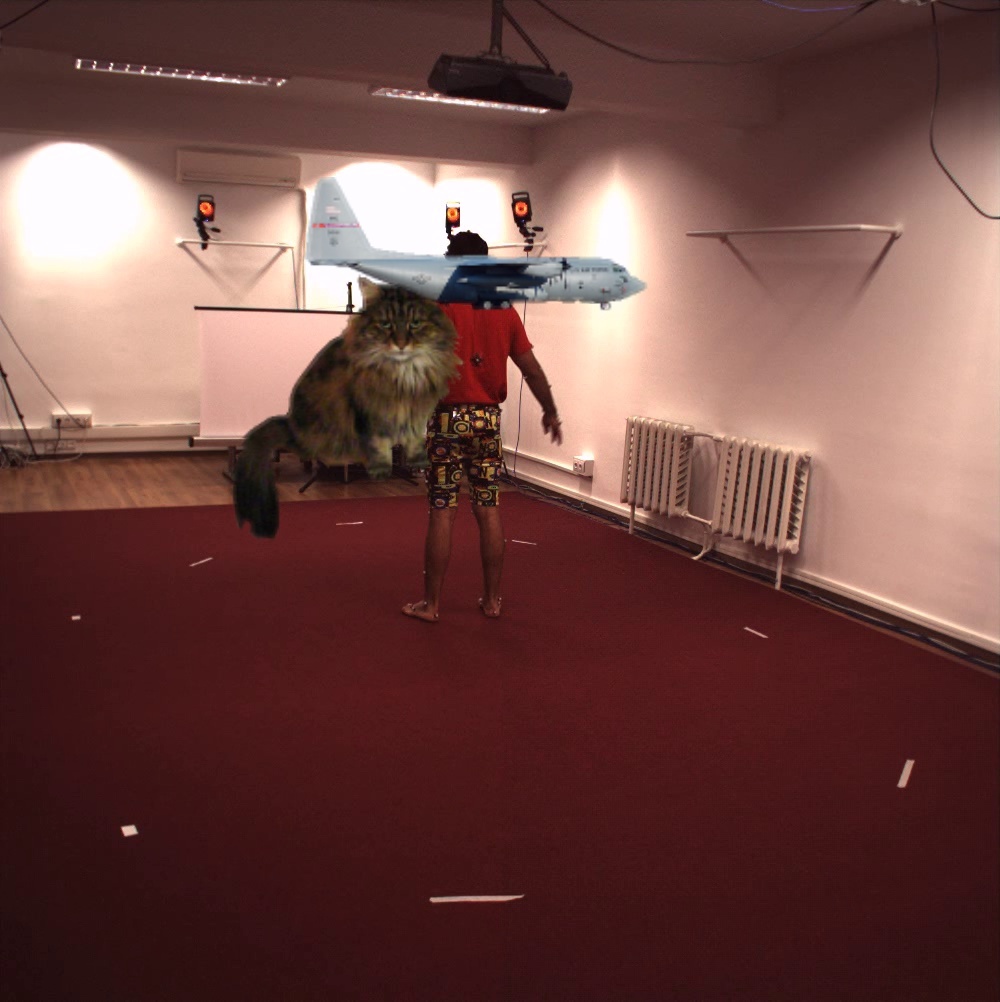

0
Multi-view Pose Fusion for Occlusion-Aware 3D Human Pose Estimation
Laura Bragagnolo, Matteo Terreran, Davide Allegro, Stefano Ghidoni
Robust 3D human pose estimation is crucial to ensure safe and effective human-robot collaboration. Accurate human perception,however, is particularly challenging in these scenarios due to strong occlusions and limited camera viewpoints. Current 3D human pose estimation approaches are rather vulnerable in such conditions. In this work we present a novel approach for robust 3D human pose estimation in the context of human-robot collaboration. Instead of relying on noisy 2D features triangulation, we perform multi-view fusion on 3D skeletons provided by absolute monocular methods. Accurate 3D pose estimation is then obtained via reprojection error optimization, introducing limbs length symmetry constraints. We evaluate our approach on the public dataset Human3.6M and on a novel version Human3.6M-Occluded, derived adding synthetic occlusions on the camera views with the purpose of testing pose estimation algorithms under severe occlusions. We further validate our method on real human-robot collaboration workcells, in which we strongly surpass current 3D human pose estimation methods. Our approach outperforms state-of-the-art multi-view human pose estimation techniques and demonstrates superior capabilities in handling challenging scenarios with strong occlusions, representing a reliable and effective solution for real human-robot collaboration setups.
Read more8/29/2024
🎲

0
Semi-Autonomous Laparoscopic Robot Docking with Learned Hand-Eye Information Fusion
Huanyu Tian, Martin Huber, Christopher E. Mower, Zhe Han, Changsheng Li, Xingguang Duan, Christos Bergeles
In this study, we introduce a novel shared-control system for key-hole docking operations, combining a commercial camera with occlusion-robust pose estimation and a hand-eye information fusion technique. This system is used to enhance docking precision and force-compliance safety. To train a hand-eye information fusion network model, we generated a self-supervised dataset using this docking system. After training, our pose estimation method showed improved accuracy compared to traditional methods, including observation-only approaches, hand-eye calibration, and conventional state estimation filters. In real-world phantom experiments, our approach demonstrated its effectiveness with reduced position dispersion (1.23pm 0.81 mm vs. 2.47 pm 1.22 mm) and force dispersion (0.78pm 0.57 N vs. 1.15 pm 0.97 N) compared to the control group. These advancements in semi-autonomy co-manipulation scenarios enhance interaction and stability. The study presents an anti-interference, steady, and precision solution with potential applications extending beyond laparoscopic surgery to other minimally invasive procedures.
Read more5/10/2024