Stretchable Pneumatic Sleeve for Adaptable, Low-Displacement Anchoring in Exosuits

0
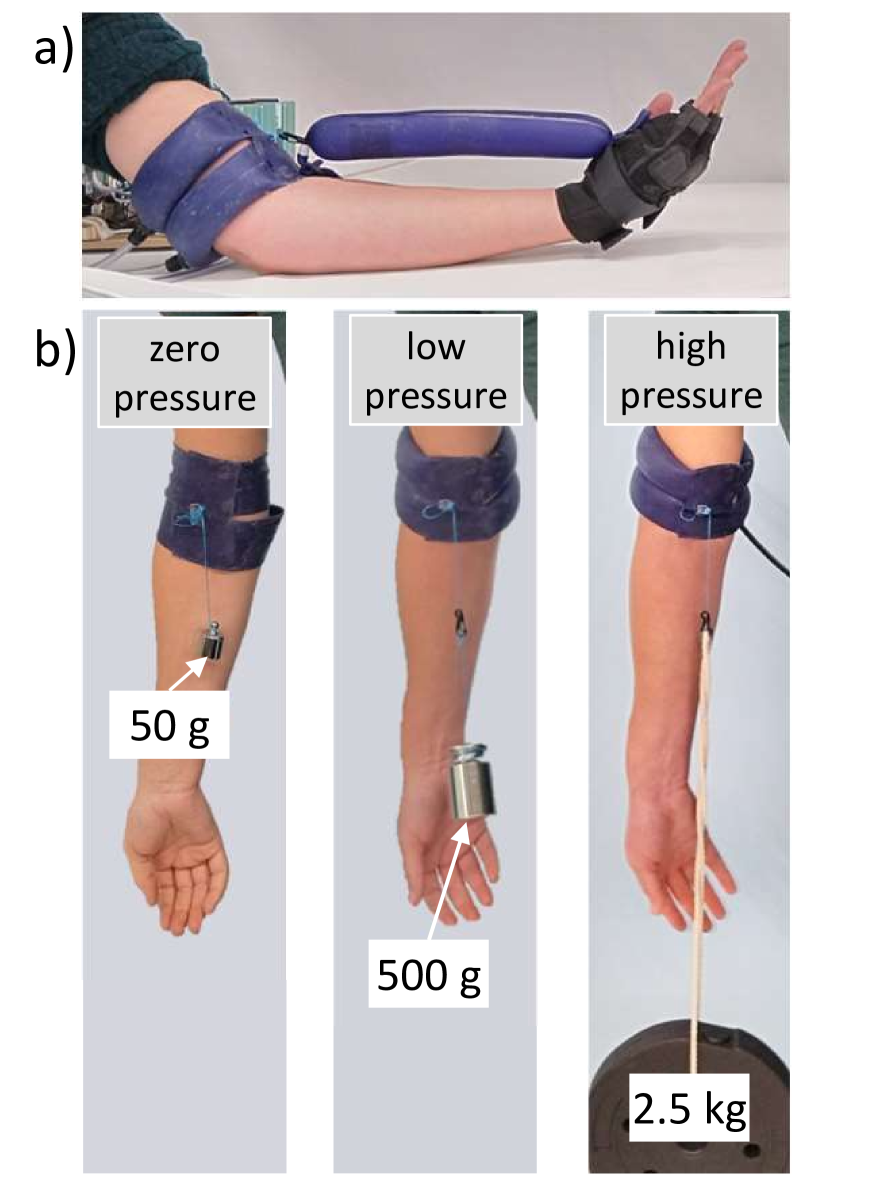
Sign in to get full access
Overview
- This paper presents the design and fabrication of a stretchable pneumatic sleeve for adaptable, low-displacement anchoring in exosuits.
- The sleeve is designed to provide a secure and adjustable interface between the exosuit and the user's limb, allowing for improved comfort and function.
- Key features include the use of a pneumatic chamber to conform to the user's limb and minimize relative displacement during movement.
Plain English Explanation
The paper describes a special sleeve that can be used with exosuits, which are wearable robotic devices that assist with movement. The sleeve is designed to comfortably and securely attach the exosuit to the user's arm or leg.
The key innovation is that the sleeve has an air-filled chamber that can expand and contract to adapt to the shape of the user's limb. This allows the sleeve to fit snugly without restricting movement or causing discomfort. The adaptable design helps minimize any unwanted shifting or displacement between the exosuit and the user's body during physical activity.
By creating a reliable, comfortable connection between the exosuit and the user, this stretchable pneumatic sleeve could help improve the overall performance and usability of exosuits for applications like rehabilitation or assisting with heavy lifting.
Technical Explanation
The paper outlines the design and fabrication of a stretchable pneumatic sleeve intended to serve as an adaptable anchoring interface for exosuits.
The sleeve features a pneumatic chamber that can conform to the user's limb, reducing relative displacement between the exosuit and the body during movement. This is achieved through careful material selection and fabrication techniques, including the use of elastomeric materials and airtight seals.
Experiments are described to evaluate the sleeve's performance in terms of adaptability, force transmission, and kinematic fidelity. The results demonstrate the sleeve's ability to maintain a stable interface while accommodating a range of limb sizes and shapes.
The technical details cover the design parameters, manufacturing process, and experimental validation of this novel pneumatic anchoring approach for enhancing the functionality of exosuits.
Critical Analysis
The paper provides a thorough examination of the stretchable pneumatic sleeve design and its potential benefits for exosuit applications. However, the authors acknowledge some limitations, such as the need to further optimize the sleeve's weight and bulk to minimize encumbrance for the user.
Additionally, the experiments conducted were primarily focused on static loading conditions, so further research may be needed to fully characterize the sleeve's performance during dynamic, high-force activities. Exploring long-term reliability and the effect of repeated use would also be valuable extensions of this work.
Overall, the presented approach represents an promising step towards improving the human-exosuit interface and enhancing the comfort and functionality of exosuits for a range of applications.
Conclusion
This paper introduces a stretchable pneumatic sleeve designed to provide a secure and adaptable anchoring interface between exosuits and the user's limbs. The key innovation is the use of a conformable air-filled chamber that can accommodate variations in limb size and shape, helping to minimize unwanted relative displacement during movement.
The technical details and experimental validation demonstrate the potential of this approach to enhance the overall performance and usability of exosuits, with potential applications in areas like rehabilitation, assistive technology, and industrial exoskeletons. Further research to optimize the sleeve design and explore its long-term durability could help unlock even greater benefits for users of these advanced wearable robotic systems.
This summary was produced with help from an AI and may contain inaccuracies - check out the links to read the original source documents!
Related Papers
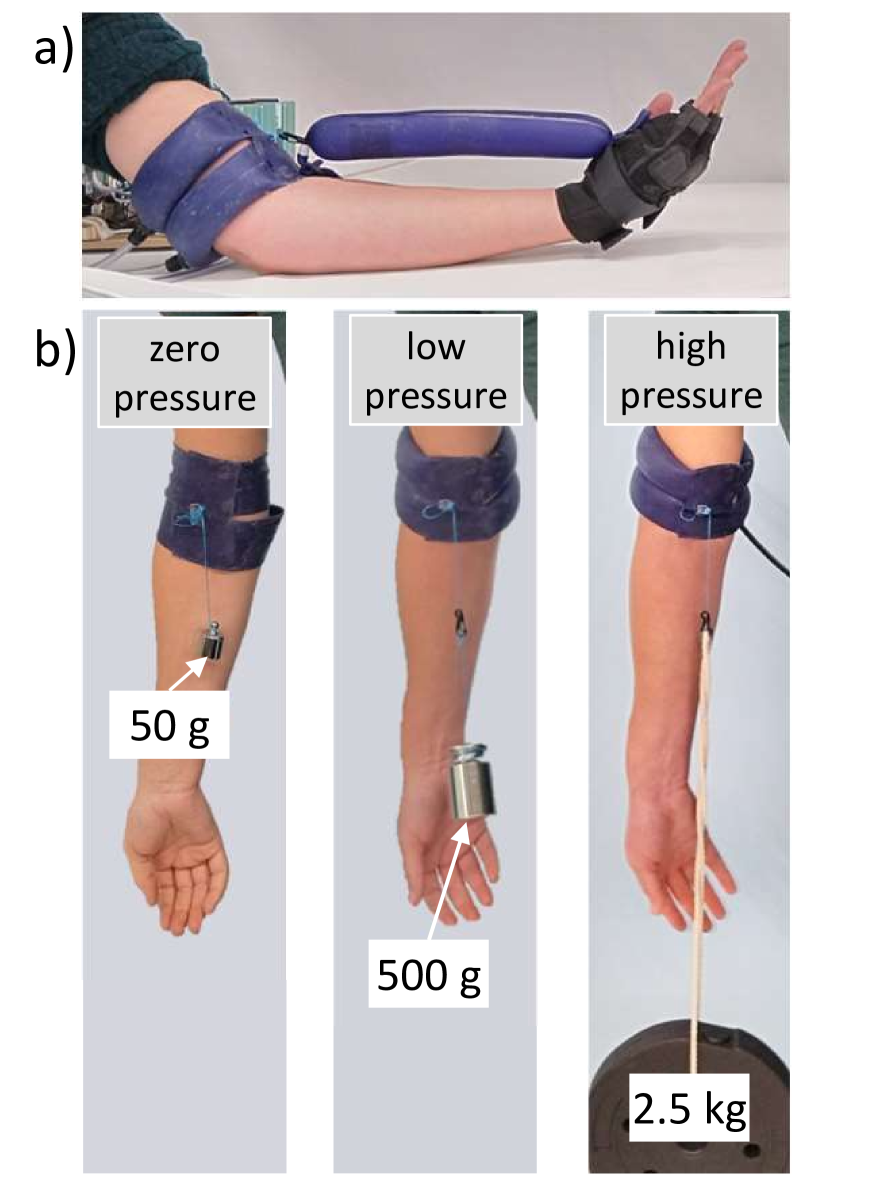

0
Stretchable Pneumatic Sleeve for Adaptable, Low-Displacement Anchoring in Exosuits
Katalin Schaffer, Ultan Fallon, Margaret M. Coad
Despite recent advances in wearable technology, interfacing movement assistance devices with the human body remains challenging. We present a stretchable pneumatic sleeve that can anchor an exosuit actuator to the human arm with a low displacement of the actuator's mounting point relative to the body during operation. Our sleeve has the potential to serve as an adaptable attachment mechanism for exosuits, since it can adjust its pressure to only compress the arm as much as needed to transmit the applied exosuit forces without a large displacement. We discuss the design of our sleeve, which is made of fabric pneumatic artificial muscle (fPAM) actuators formed into bands. We quantify the performance of nine fPAM bands of various lengths and widths, as well as three sleeves (an fPAM sleeve, a series pouch motor (SPM) sleeve as in previous literature, and an off the shelf hook and loop sleeve), through the measurement of the compressing force as a function of pressure and the localized pulling force that can be resisted as a function of both pressure and mounting point displacement. Our experimental results show that fPAM bands with smaller resting length and/or larger resting width produce higher forces. Also, when inflated, an fPAM sleeve that has equivalent dimensions to the SPM sleeve while fully stretched has similar performance to the SPM sleeve. While inflated, both pneumatic sleeves decrease the mounting point displacement compared to the hook and loop sleeve. Compared to the SPM sleeve, the fPAM sleeve is able to hold larger internal pressure before bursting, increasing its possible force range. Also, when not inflated, the fPAM sleeve resists the pulling force well, indicating its ability to provide anchoring when not actuated.
Read more4/9/2024
📶

0
Soft Wrist Exosuit Actuated by Fabric Pneumatic Artificial Muscles
Katalin Schaffer, Yasemin Ozkan-Aydin, Margaret M. Coad
Recently, soft actuator-based exosuits have gained interest, due to their high strength-to-weight ratio, inherent safety, and low cost. We present a novel wrist exosuit actuated by fabric pneumatic artificial muscles that has lightweight wearable components (160 g) and can move the wrist in flexion/extension and ulnar/radial deviation. We derive a model representing the torque exerted by the exosuit and demonstrate the use of the model to choose an optimal design for an example user. We evaluate the accuracy of the model by measuring the exosuit torques throughout the full range of wrist flexion/extension. We show the importance of accounting for the displacement of the mounting points, as this helps to achieve the smallest mean absolute error (0.283 Nm) compared to other models. Furthermore, we present the measurement of the exosuit-actuated range of motion on a passive human wrist. Finally, we demonstrate the device controlling the passive human wrist to move to a desired orientation along a one and a two-degree-of-freedom trajectory. The evaluation results show that, compared to other pneumatically actuated wrist exosuits, the presented exosuit is lightweight and strong (with peak torque of 3.3 Nm) but has a limited range of motion.
Read more4/15/2024
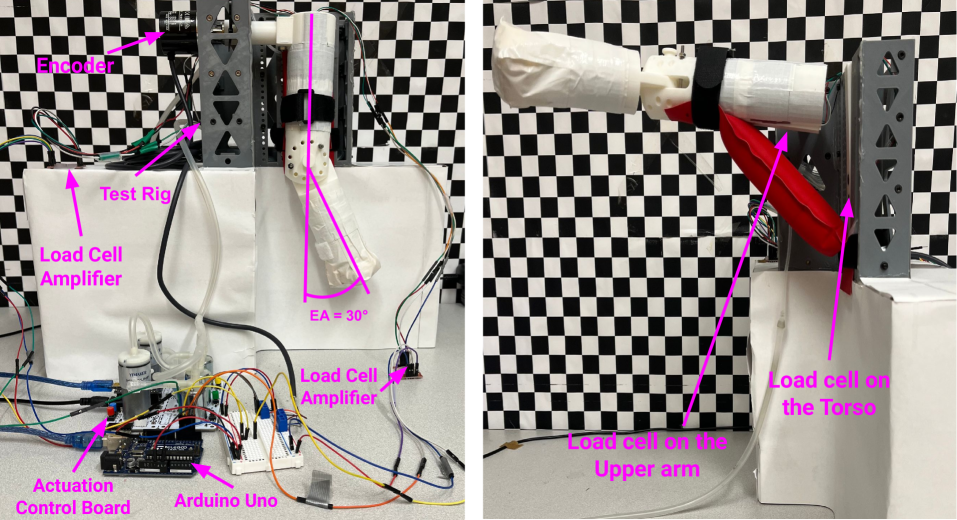

0
Force Profiling of a Shoulder Bidirectional Fabric-based Pneumatic Actuator for a Pediatric Exosuit
Mehrnoosh Ayazi, Ipsita Sahin, Caio Mucchiani, Elena Kokkoni, Konstantinos Karydis
This paper presents a comprehensive analysis of the contact force profile of a single-cell bidirectional soft pneumatic actuator, specifically designed to aid in the abduction and adduction of the shoulder for pediatric exosuits. The actuator was embedded in an infant-scale test rig featuring two degrees of freedom: an actuated revolute joint supporting shoulder abduction/adduction and a passive (but lockable) revolute joint supporting elbow flexion/extension. Integrated load cells and an encoder within the rig were used to measure the force applied by the actuator and the shoulder joint angle, respectively. The actuator's performance was evaluated under various anchoring points and elbow joint angles. Experimental results demonstrate that optimal performance, characterized by maximum range of motion and minimal force applied on the torso and upper arm, can be achieved when the actuator is anchored at two-thirds the length of the upper arm, with the elbow joint positioned at a 90-degree angle. The force versus pressure and joint angle graphs reveal nonlinear and hysteresis behaviors. The findings of this study yield insights about optimal anchoring points and elbow angles to minimize exerted forces without reducing the range of motion.
Read more7/19/2024
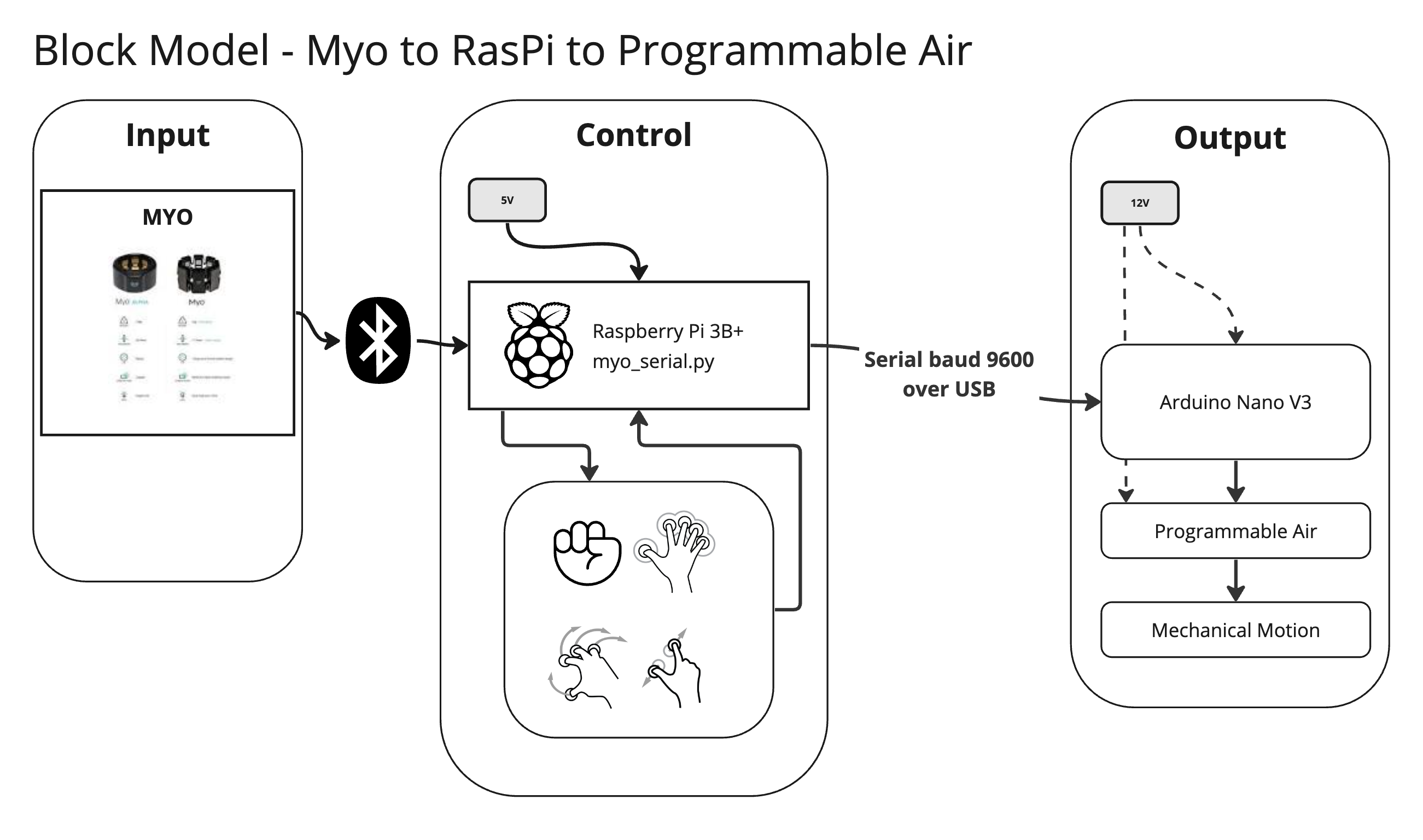

0
Ephemeral Myographic Motion: Repurposing the Myo Armband to Control Disposable Pneumatic Sculptures
Celia Chen, Alex Leitch
This paper details the development of an interactive sculpture built from deprecated hardware technology and intentionally decomposable, transient materials. We detail a case study of Strain - an emotive prototype that reclaims two orphaned digital artifacts to power a kinetic sculpture made of common disposable objects. We use the Myo, an abandoned myoelectric armband, in concert with the Programmable Air, a soft-robotics prototyping project, to manipulate a pneumatic bladder array constructed from condoms, bamboo skewers, and a small library of 3D printed PLA plastic connectors designed to work with these generic parts. The resulting sculpture achieves surprisingly organic actuation. The goal of this project is to produce several reusable components: software to resuscitate the Myo Armband, homeostasis software for the Programmable Air or equivalent pneumatic projects, and a library of easily-printed parts that will work with generic bamboo disposables for sculptural prototyping. This project works to develop usable, repeatable engineering by applying it to a slightly whimsical object that promotes a strong emotional response in its audience. Through this, we transform the disposable into the sustainable. In this paper, we reflect on project-based insights into rescuing and revitalizing abandoned consumer electronics for future works.
Read more4/15/2024